Huaxia Deng, CAS Key Laboratory of Mechanical Behavior and Design of Materials, Department of Modern Mechanics, University of Science and Technology of China, Hefei 230027, Anhui, China. E-mail: hxdeng@ustc.edu.cn
Xinglong Gong, CAS Key Laboratory of Mechanical Behavior and Design of Materials, Department of Modern Mechanics, University of Science and Technology of China, Hefei 230027, Anhui, China. E-mail: gongxl@ustc.edu.cn
Abstract
Magnetorheological fluid (MRF) has broad application prospects in the field of engineering vibration damping due to its magnet-sensitive characteristics. However, owing to its dependence on external electric or magnetic fields, devices based on MRF can't work once the power is turned off. Here we developed a magnetorheological shear thickening fluid (MRSTF) with both the magnet-sensitive and rate-sensitive characteristics. The shear thickening effect of MRSTF was examined, revealing that the critical shear rate
Keywords
1. Introduction
Magnetorheological fluid (MRF) represents an advanced smart material known for its adjustable viscosity and fast response time. It is primarily composed of magnetic particles, carrier liquid, and various additives[1,2]. Characterized by its transition from a low-viscosity to a high-viscosity state under external magnetic fields, MRF exhibits a pronounced magnetorheological effect[3,4]. Once the external magnetic field is removed, MRF immediately reverts to its initial low-viscosity state. Therefore, the mechanical properties of MRF can be easily controlled by the external applied magnetic field.
Due to the magnet-sensitive characteristics, MRF-based devices have been designed and used in the fields of automotive applications[5-8], architectural structures[9-11] and high-speed train[12-15]. As a type of semi-active control device, the magnetorheological (MR) damper has the advantages of simple structure, controllable damping force and fast response[16,17], and has attracted more attention since it has been used in the commercial market. In the environment of external magnetic field, the magnetic particles in the MRF system will be oriented, leading to an increase in viscosity. However, in the absence of a magnetic field, these particles fail to respond. Therefore, MRF relies on the presence of an external magnetic or electric field to undergo a transition from liquid to quasi-solid state, implying that the functionality of dampers may be compromised in the event of an electrical failure.
Shear thickening fluid (STF) is a class of non-Newtonian suspension, predominantly consisting of dispersed particles within a dispersing medium, which exhibits a viscosity increase in response to elevated external shear rate or shear stress[18,19]. When subjected to external stress, the particles inside the STF change from uniform distribution to particle cluster structure[20-22], triggering a transition from liquid to quasi-solid state and a corresponding significant rise in viscosity of suspension. Once the external stimulus is removed, STF swiftly reverts to their original state. Owing to its distinctive mechanical properties, STF has been widely used in the polishing[23], dampers[24] and flexible wearable protective materials[25-28]. STF is capable of transforming from liquid to quasi-solid state when the suspension is subjected to external shear stress, and simultaneously exhibits the fast response times[29-31], reversible properties[32,33] and efficient energy dissipation[34-36]. Combining the advantages of MRF and STF, magnetorheological shear thickening fluid (MRSTF) has both rate sensitive and magnetic sensitive properties, which makes it have potential applications in the fields of dampers[24] and polishing[37]. Due to the strong inclusiveness of MRF and STF systems, the combination of the two materials can improve the disadvantage of no protection after power failure of devices based on magnetorheological materials, and help devices to achieve self-reinforcing and self-regulating functions.
In this study, MRSTF with both shear thickening and magnetorheological effects was obtained by ball milling method. The mechanical properties of MRSTF were evaluated by a rheometer, and a comparative analysis was conducted on the rheological changes in STF and MRSTF. Additionally, we measured the rheological characteristics of MRSTF with varying carbonyl iron powder (CIP) concentrations and investigated the influence mechanism of external magnetic field on the shear thickening and magnetorheological effects of MRSTF. Ultimately, we tested the mechanical properties of MRSTF-based dampers and analyzed the influence of frequency, amplitude and magnetic field on their performance.
2. Experimental Section
2.1 Materials
The commercial SiO2 was purchased from Andy Metal Materials Co., Ltd. and polyethylene glycol (PEG200) was purchased from Sinopharm Chemical Reagent Co., Ltd. The CIP was purchased from Jiangsu Tianyi Ultra-fine Metal Powder Co., Ltd.
2.2 Characterization
The microstructures of commercial SiO2 particles and CIP were characterized by using a Scanning Electron Microscope (SEM, Gemini SEM 500) at an acceleration voltage of 3 kV. As depicted in Figure 1a,b,c, SiO2 exhibits a uniform dispersion with an average diameter of 300 nm, which is beneficial to forming a stable suspension. Concurrently, the average particle size of CIP is identified as 3.5 μm.

Figure 1. The SEM micrographs of (a), (b) SiO2 and (c) CIP. Preparation process of (d) STF and (e) MRSTF. SEM: scanning electron microscope; CIP: carbonyl iron powder; STF: shear thickening fluid; MRSTF: magnetorheological shear thickening fluid; PEG: polyethylene glycol.
2.3 Preparation process of STF and MRSTF
Commercial SiO2 particles were dried in an oven at 100 °C for 10 h before use. According to different mass fractions, SiO2 of different mass was weighed and put into the ball mill tank, and the corresponding volume of PEG200 was measured and put into the ball mill for 24 h, and STF was obtained after uniform mixing (Figure 1d). The CIP with different volume fractions was weighed and put into the prepared STF, and then put into the ball mill for 24 h to obtain MRSTF (Figure 1e).
2.4 Rheological test
The rheological properties of STF were tested using the rheometer (Anton-Paar MCR 302) with plate geometry (25 mm in diameter), and the experiments were conducted with a gap size of 1 mm at 25 °C under shear rate ranging from 0.1 to 1,000 s-1. In the test phase, the shear rate of 0.1 s-1 was pre-shear for 20 s until the viscosity of the system was stable, and then the formal shear test began. The rheological properties of MRSTF were tested using the rheometer (Anton-Paar MCR 302) with plate geometry at 25 °C, controlled by the shear rate of 0.1 to 1,000 s-1, and with a gap size of 1 mm. The magnetic flux density was controlled by the magnetic field device. Meantime, tests were also carried out at 15 °C, 25 °C, 35 °C, 45 °C, 55 °C and 65 °C. The on-site photo of the testing system of the material rheological property is shown in Figure S1.
2.5 The mechanical properties test
The mechanical performance of dampers was measured by testing machine and the test system includes a universal testing machine, an extrusion and tensile test device, a temperature sensor, and a power supply. In the presence and absence of an external magnetic field, several groups of comparison experiments were carried out, and the corresponding curves were recorded and analyzed. The on-site photo of the testing system of the mechanical property is shown in Figure S2.
3. Results and Discussion
3.1 The rheological properties of STF
The rheological properties of the prepared STF were tested using the rheometer MCR 302. The primary components of this testing system are displayed in Figure 2a, mainly including the MCR 302 rheometer, the magnetic field device, and the temperature control unit.
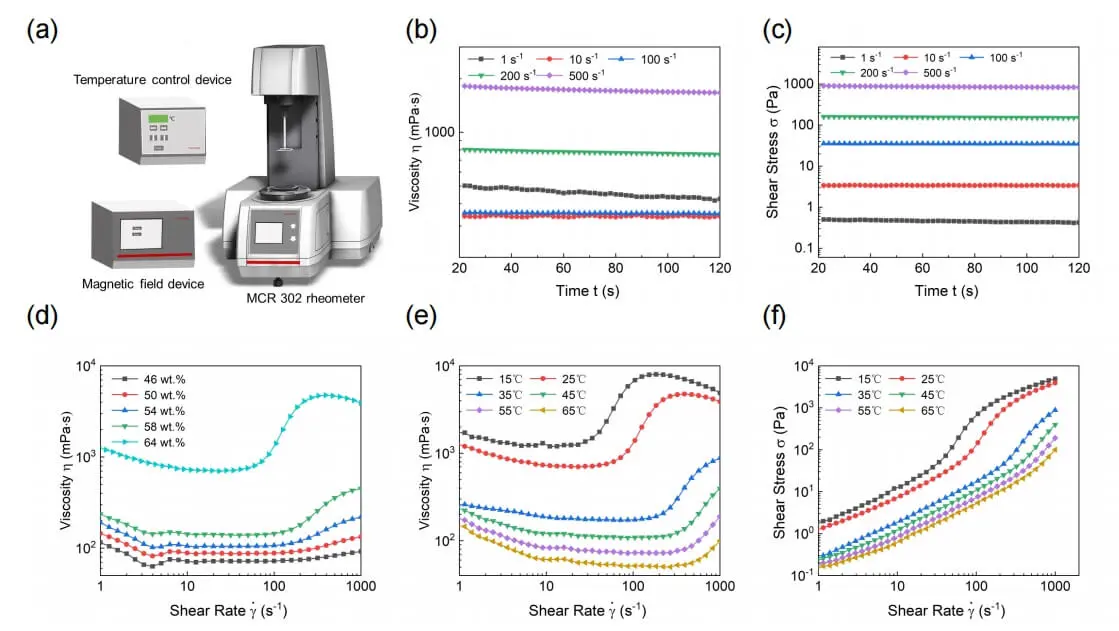
Figure 2. (a) Schematic diagram of MCR 302 rheometer and related devices; The stability of STF (64 wt.%): the curves of (b) viscosity and (c) shear stress versus time under different shear rates; (d) The curves of viscosity versus shear rate at different mass fractions of STF; The curves of (e) viscosity and (f) shear stress versus shear rate under different temperatures of STF (64 wt.%). STF: shear thickening fluid.
Initially, the STF with a mass fraction of 64 wt.% was subjected to steady-state shearing at varying shear rates to assess its stability, and the consequent viscosity changes were meticulously documented, as illustrated in Figure 2b. It was observed that at the initial shear rate of 1 s-1, the viscosity of STF is stable around 450 mPa·s, maintaining stability upon continued shearing. These viscosity-time curves were also observed at other shear rates, indicating the stability of prepared STF. Notably, at shear rates of 10 and 100 s-1, the viscosity stabilizes at 335 and 355 mPa·s, respectively, marking a significant reduction from the viscosity at the initial shear rate of 1 s-1 (450 mPa·s), which is attributed to the shear thinning behavior of the STF (when the shear rate is less than critical shear rate). Concurrently, when the shear rate is set to 200 s-1, the viscosity stabilizes at 780 mPa·s, indicating a pronounced increase due to the shear thickening effect of STF. Upon further increasing the shear rate to 500 s-1, the viscosity stabilizes at 1,700 mPa·s, which shows the four times increase compared to the viscosity at the initial shear rate of 1 s-1. The real-time shear stress variations of the STF under different shear rates were also presented in Figure 2c, showing that the shear stress of STF remains consistent in 120 seconds.
Besides, the rheological properties of STF with different mass fractions of SiO2 were further evaluated, as shown in Figure 2d. It was shown that an increase in the dispersed phase mass fraction benefits the shear thickening effect of the STF, characterized by a decrease in the critical shear rate and an increase in the maximum viscosity of suspension. Moreover, the STF was tested at a broad temperature range, as demonstrated in Figure 2e,f, the STF exhibits a shear thickening effect over the temperature range of 15 °C to 65 °C. It was observed that the shear thickening effect of the STF increases as the temperature decreases. This is primarily attributed to the reduction in temperature, which weakens the Brownian motion of the dispersed phase particles in the suspension and reduces the repulsive forces between particles[38].
3.2 The rheological properties of MRSTF
3.2.1 MRSTF with 20 vol.% CIP
MRSTF with both shear thickening and magnetorheological effects was successfully prepared by incorporating an amount of CIP into STF. The rheological behavior of MRSTF (20 vol.% CIP) is presented in Figure 3a, and the results show that the overall viscosity of MRSTF is significantly higher than that of STF. Concurrently, the rheological behavior of MRSTF (SiO2: 54 wt.%, CIP: 20 vol.%) was tested over a wide temperature range, as shown in Figure S3, where the MRSTF showed a shear thickening effect over a temperature range of 15 °C to 65 °C.
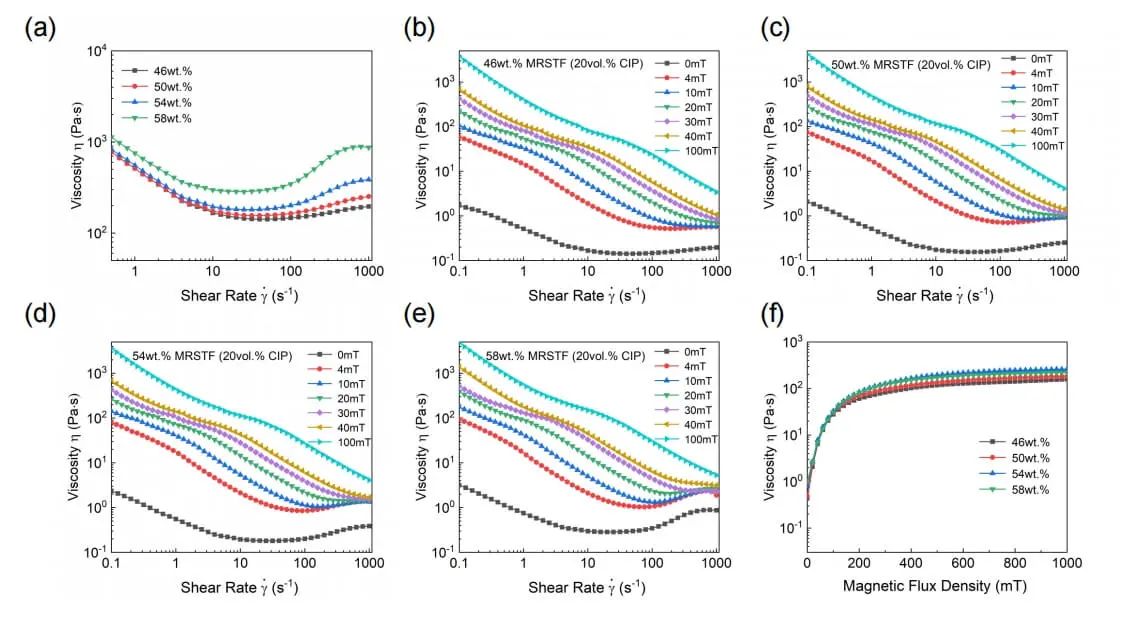
Figure 3. (a) The curves of viscosity versus shear rate of MRSTF at different mass fractions of SiO2 ; rheological properties of MRSTF (20 vol.% CIP) with different mass fractions of SiO2 under different magnetic field strengths: (b) 46 wt.%; (c) 50 wt.%; (d) 54 wt.%; (e) 58 wt.%; (f) rheological curves of MRSTF with different mass fractions of SiO2 under magnetic field scanning. MRSTF: magnetorheological shear thickening fluid; CIP: carbonyl iron powder.
Subsequently, the rheological properties of MRSTF were conducted under various magnetic field intensities. Figure 3b,c,d,e illustrate the viscosity-shear rate curves of MRSTF (20 vol.% CIP) with varying mass fractions of SiO2 under different magnetic field strengths. It was shown that the viscosity of MRSTF incrementally increases with the enhancement of magnetic field intensity, which is attributed to the polarization of CIP particles within the system under the influence of an external magnetic field, leading to the formation of an orderly chain-like arrangement. The emergence of this chain structure results in a rise of viscosity, endowing the suspension with solid-like properties. Additionally, it is evident that MRSTF exhibits a pronounced shear thickening effect at a relatively low magnetic field intensity. When the mass fraction of SiO2 is set as 46 wt.%, 50 wt.%, 54 wt.% and 58 wt.%, the shear thickening effect disappears at magnetic field intensities of 10 mT, 20 mT, 30 mT and 40 mT, respectively. This is predominantly due to the fact that chain structures within the system are easier to form at higher magnetic field strengths, which prevents the formation of particle cluster structures necessary for shear thickening. Therefore, when CIP volume fraction is 20 vol.%, MRSTF exhibits shear thickening effect over a wider range of magnetic field intensity with the increase of SiO2 mass fraction.
The shear stress-shear rate curves of MRSTF (20 vol.% CIP) were presented in Figure S4. The analysis revealed that the shear stress of MRSTF escalates with the augmentation of external magnetic field intensity, which can be primarily divided into three distinct stages: At low shear rates (0 <
3.2.2 MRSTF with 30 vol.% CIP
To further evaluate the effect of CIP particles on shear thickening performance of the suspension, the CIP content was increased to 30 vol.%. The viscosity-shear rate curves of MRSTF (30 vol.% CIP), at mass fractions of 54 wt.% and 58 wt.% of SiO2, are depicted in Figure 4a,b, respectively. In the absence of a magnetic field, the viscosity of MRSTF (30 vol.% CIP) exhibits an initial decline followed by an ascent with increasing shear rate. Concurrently, the viscosity of the system experiences increases significantly due to a higher CIP concentration. Upon the application of an external magnetic field, the viscosity of MRSTF is improved by three orders of magnitude, demonstrating a pronounced magnetorheological effect. Meanwhile, the shear thickening effect disappears, and the viscosity of MRSTF decreases with the increase in shear rate, manifesting shear thinning characteristics within the entire range. This transition is primarily attributed to the formation of a magnetic field-induced chain structure, which prevents the aggregation of particles into clusters, thereby nullifying the shear thickening effect.

Figure 4. The curves of viscosity versus shear rate of MRSTF (30 vol.% CIP) with different SiO2 mass fractions under different magnetic field strengths: (a) 54 wt.% and (b) 58 wt.%. The curves of shear stress versus shear rate of MRSTF (30 vol.% CIP) with different SiO2 mass fractions under different magnetic field strengths: (c) 54 wt.% and (d) 58 wt.%. The curves of (e) viscosity and (f) shear stress versus magnetic flux density of MRSTF (30 vol.% CIP) with different SiO2 mass fractions under different shear rates. MRSTF: magnetorheological shear thickening fluid; CIP: carbonyl iron powder.
For comparison, the viscosity-shear rate curves of MRSTF (20 vol.% CIP) under identical magnetic field conditions are shown in Figure S6a and Figure S6b. Notably, at equivalent shear rates, the viscosity of MRSTF (30 vol.% CIP) substantially exceeds that of MRSTF (20 vol.% CIP). This enhancement is primarily ascribed to the increased CIP content of magnetic particles in MRSTF, which accelerates the formation of extensive particle chains under the same magnetic field.
The shear stress-shear rate curves for MRSTF (30 vol.% CIP) are illustrated in Figure 4c,d. The data revealed that the shear stress increases with the shear rate, with the rate of increase intensifying as the magnetic field intensity augments. Additionally, the rate at which shear stress increases exhibits a gradual deceleration with the progression of shear rate, mirroring the transition of MRSTF from a solid-like state at low shear rates to a flowing plastic fluid. Upon reaching the yield stress, the escalation rate of shear stress markedly diminishes, underscoring the pronounced yield behavior characteristic of plastic fluids. Concurrently, the yield stress of MRSTF (30 vol.% CIP) is higher than that in the MRSTF (20 vol.% CIP) (Figure S6c and Figure S6d). This enhancement is predominantly attributed to the fact that MRSTF with a higher concentration of CIP forms a more extensive network of particle chains under the same magnetic field, thereby enhancing the microstructural strength. The correlation between the viscosity and shear stress of MRSTF (30 vol.% CIP) and magnetic field intensity was depicted in Figure 4e,f. Different from the MRSTF (20 vol.% CIP), the increased presence of CIP magnetic particles in the MRSTF (30 vol.% CIP) system facilitates the formation of a greater number of chain structures under equivalent magnetic field conditions. This results in higher terminal values of viscosity and shear stress for the system when the increments cease.
To delve deeper into the impact of CIP particle incorporation on the shear thickening behavior of STF, a comparative analysis of the viscosity-shear rate curves for STF with SiO2 mass fractions of 54 wt.% and 58 wt.% across various volume fractions of CIP was conducted, as depicted in Figure 5a,b. The results showed that an increase in the volume fraction of CIP leads to a significant improvement in the viscosity of the suspension. Furthermore, to provide a clearer comparison of the effect of CIP addition on the shear thickening performance of STF, the critical shear rate
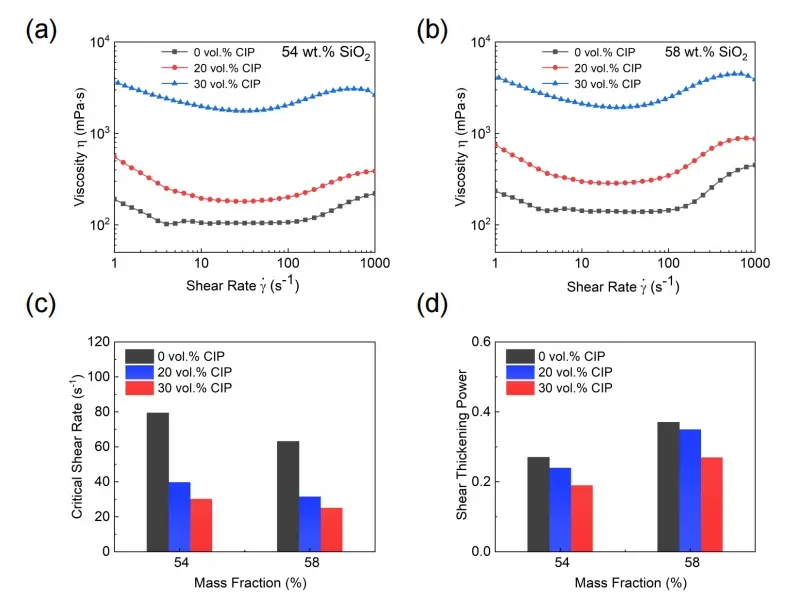
Figure 5. Viscosity and shear rate curves of STF with SiO2 mass fractions of (a) 54 wt.% and (b) 58 wt.% after adding different volume fractions CIP. Comparison of (c) critical shear rate
3.3 Mechanical properties of MRSTF damper
3.3.1 The structure of MRSTF damper
The diagram of the damper is shown in Figure S8. The damper is mainly composed of four parts: shell, coil, piston and piston rod. The cavity inside the shell contains MRSTF fluid. When current passes through the coil, a magnetic field is generated, causing the CIP particles in fluid to form a chain structure under the influence of the magnetic field. Meanwhile, when the damper is operating, the MRSTF will flow back and forth between several cavity areas in the housing with the movement of the piston. Due to the magnet-sensitive and rate-dependent properties of MRSTF, the damper based on this type of smart materials can achieve active control under a magnetic field and passive energy consumption of the system after a power failure.
3.3.2 The damping force-displacement curves of MRSTF damper at 0 A current
The prepared MRSTF was poured into the cavity of the damper, where it moved up and down with the piston during the damper's operation. To test the mechanical properties of MRSTF dampers, the influences of frequency, current, and amplitude on the damping force of the dampers were studied.
Initially, the damping force of the MRSTF damper was measured without applying an electric current. Figure 6a,b show the force-displacement curves of MRSTF damper at two distinct frequencies, with amplitudes of 25 mm and 50 mm, respectively. The horizontal axis indicates the piston's displacement, while the vertical axis represents the damping force. Forces above the 0 axis correspond to the rebound force, and those below correspond to the compression force. Additionally, the area enclosed by the damping force-displacement curve is indicative of the damper's energy dissipation capacity. The results showed that the rebound force of the MRSTF damper exceeds the compression force, indicating that the damper exhibits damping capabilities. Furthermore, when the damper's frequency is elevated from 0.318 Hz to 0.955 Hz, the area enclosed by the damping force-displacement curve expands significantly, indicating that the damper's energy dissipation capacity increases with higher frequency. The results also showed that the damping force and energy dissipation capacity of the damper increase with velocity. This is primarily due to the increasing speed of the damper piston, which raises the shear stress on the MRSTF within the cavity, thereby enhancing the damping force.
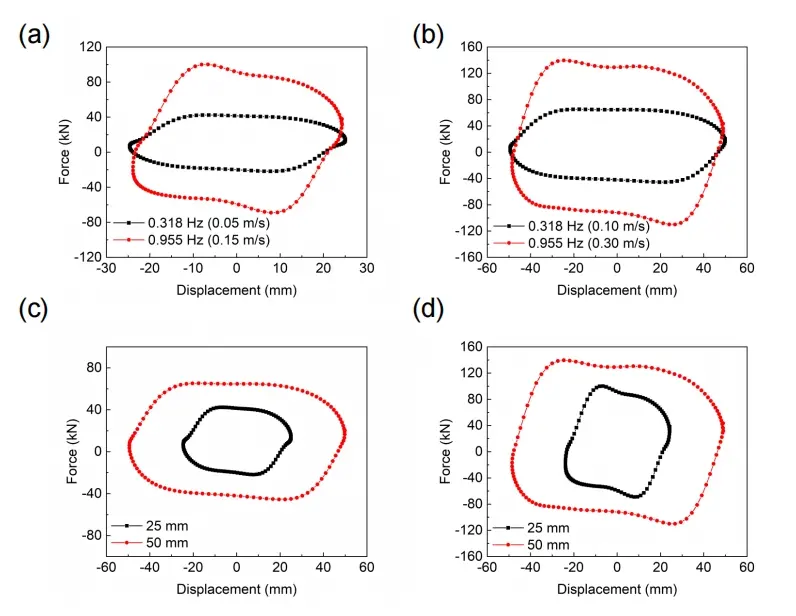
Figure 6. Damping force-displacement curves of MRSTF damper at different frequencies at 0 A current at (a) 25 mm and (b) 50 mm amplitude. Damping force-displacement curves of MRSTF damper at different amplitudes at 0 A current at (c) 0.318 Hz and (d) 0.955 Hz. MRSTF: magnetorheological shear thickening fluid.
Moreover, it was observed that the damping force exhibits linear variation at a frequency of 0.318 Hz, but transitions to a nonlinear variation with significant fluctuations as the frequency increases to 0.955 Hz. This is mainly due to the shear thickening of MRSTF in the range of 30.2 s-1-1,000 s-1 (0.0133 m/s - 0.44 m/s), along with the nonlinear increase in MRSTF viscosity as the velocity rises within this range.
Figure 6c,d present the damping force-displacement curves at different amplitudes for frequencies of 0.318 Hz and 0.955 Hz, respectively. The results demonstrated that at the lower frequency (0.318 Hz), the damping force displays linear behavior at amplitudes of 25 mm and 50 mm, with a notable increase in damping force as the amplitude increases. The area circumscribed by the damping force-displacement curve also expands significantly, signifying that the damper's energy dissipation capacity increases with frequency. Conversely, at the higher frequency (0.955 Hz), the damping force exhibits nonlinear variations at both 25 mm and 50 mm amplitudes, with notable fluctuations. This suggests that the nonlinear mechanical properties of the MRSTF damper are more sensitive to changes in frequency.
3.3.3 The damping force-displacement curves of MRSTF damper in the presence of current
The influence of frequency and amplitude on the damping force of MRSTF damper under a magnetic field was studied by applying current to the damper.
Figure 7a,b show the force-displacement curves of the MRSTF damper after applying current at various frequencies (0.318 Hz to 0.955 Hz) and amplitudes (25 mm to 50 mm), respectively. The analysis revealed that at a frequency of 0.318 Hz, the damping force of the MRSTF damper increases significantly after applying current, compared to the damper force with no current applied (Figure 6a), with a substantial expansion of the area enclosed by the damping force-displacement curve. This increase signifies a boosted energy dissipation capacity of the damper. This enhancement is primarily attributed to the formation of chain-like structures by the CIP particles within the MRSTF under the influence of a magnetic field, causing a transition from liquid to quasi-solid state and a consequent increase in viscosity, which consequently amplifies the damping force.
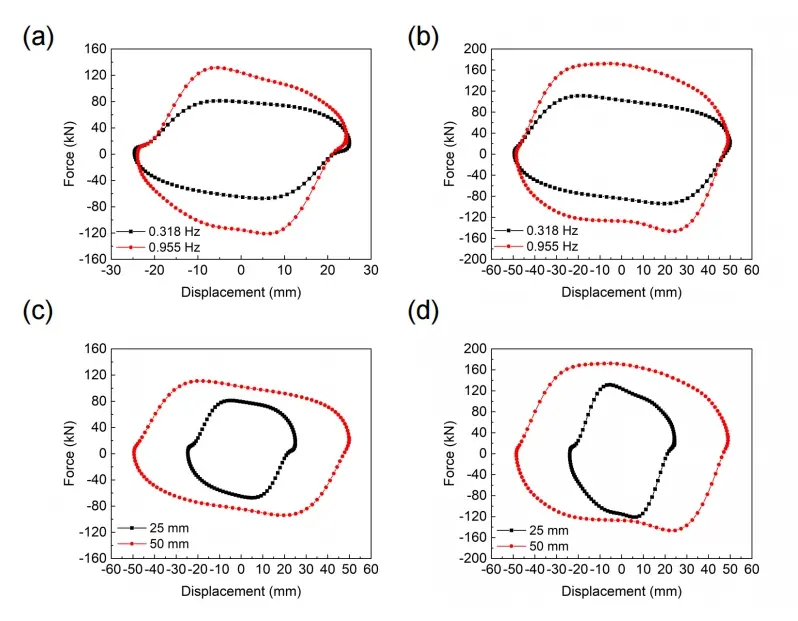
Figure 7. Damping force-displacement curves of MRSTF dampers after applying current at different frequencies at (a) 25 mm and (b) 50 mm amplitude. Damping force-displacement curves of MRSTF damper after applying current at different amplitudes at (c) 0.318 Hz and (d) 0.955 Hz. MRSTF: magnetorheological shear thickening fluid.
At the higher frequency of 0.955 Hz, without the application of current, the MRSTF damper exhibits nonlinear changes at both 25 mm and 50 mm amplitudes, with the damping force-displacement curves showing a wide range of fluctuations (Figure 6a,b). This variability may stem from the random distribution of CIP particles within the MRSTF in the absence of a magnetic field, where the unrestricted movement of particles causes significant fluctuations in the damping force. After the application of current, the fluctuation range of the damping force is reduced, mainly because the CIP particles align along the magnetic field lines, forming chain-like structures, which reduces the shear thickening effect and results in a narrower fluctuation range in the damping force. Furthermore, as shown in Figure 7a,b, the damping force of the MRSTF damper is more sensitive to changes in frequency than to the application of current.
The damping force-displacement curves of the MRSTF damper with different amplitudes after applying current at frequencies of 0.318 Hz and 0.955 Hz are shown in Figure 7c,d, respectively. At low frequency (0.318 Hz), as the amplitude increases, the change in damping force-displacement curve remains consistent with the increasing amplitude. The area enclosed by the curve expands significantly with the increasing damping force, suggesting that the application of current does not alter the overall pattern of damping force changes in the MRSTF damper. At the higher frequency (0.955 Hz), without the application of current, the damping force of the MRSTF damper displays pronounced fluctuations and nonlinear behavior, with these fluctuations intensifying as the amplitude increases (Figure 6d). Upon the application of current, there is a marked increase in damping force and a reduction in fluctuations. This is predominantly due to the fact that the CIP particles within the MRSTF align into an ordered chain-like structure under the influence of current, which reduces the fluctuations in the damping force of the MRSTF damper.
4. Conclusion
In this research, a type of smart material with both magnet-sensitive and rate-dependent characteristics was prepared by the ball-milling method. The results showed that the addition of CIP weakens the shear thickening effect of STF, as indicated by the gradual decrease in the critical shear rate
Supplementary materials
The supplementary material for this article is available at: Supplementary materials.
Authors contribution
Liu Q: Formal analysis, conceptualization, investigation, writing-original draft.
Liu B: Formal analysis, writing-review & editing.
Pan Y, Zhao Y, Wang K: Investigation.
Deng H: Methodology, funding acquisition, writing-review & editing.
Gong X: Supervision, project administration, resources, funding acquisition, writing-review & editing.
All authors approved the final version of the manuscript.
Conflicts of interest
The authors declare no conflicts of interest.
Ethical approval
Not applicable.
Consent to participate
Not applicable.
Consent for publication
Not applicable.
Availability of data and materials
The data and materials could be obtained from the corresponding authors upon request.
Funding
This study was supported by the National Natural Science Foundation of China (Grant Nos. 12302250, 12372187, 12132016, 12427802, and 52321003); the China Postdoctoral Science Foundation (Grant No. 2023M733388); the Fundamental Research Fund for the Central Universities (Grant Nos. WK2480000010 and WK2090000075); the CAS Talent Introduction Program (Grant No. KJ2090007006); and the University Synergy Innovation Program of Anhui Province (Grant No. GXXT-2023-024).
Copyright
© The Author(s) 2025.
References
-
1. Lee TH, Choi SB. On the response time of a new permanent magnet based magnetorheological damper: experimental investigation. Smart Mater Struct. 2019;28(1):014001.
[DOI] -
2. Sun S, Yang J, Li W, Deng H, Du H, Alici G. Development of a novel variable stiffness and damping magnetorheological fluid damper. Smart Mater Struct. 2015;24(8):085021.
[DOI] -
3. Liu B, Du C, Deng H, Fan Z, Zhang J, Zeng F, et al. Mechanical properties of magneto-sensitive shear thickening fluid absorber and application potential in a vehicle. Compos Part A Appl Sci Manuf. 2022;154:106782.
[DOI] -
4. Mawkhlieng U, Majumdar A. Deconstructing the role of shear thickening fluid in enhancing the impact resistance of high-performance fabrics. Compos Part B Eng. 2019;175:107167.
[DOI] -
5. Sassi S, Cherif K, Mezghani L, Thomas M, Kotrane A. An innovative magnetorheological damper for automotive suspension: from design to experimental Characterization. Smart Mater Struct. 2005;14:811-822.
[DOI] -
6. Yu M, Dong XM, Choi SB, Liao CR. Human simulated intelligent control of vehicle suspension system with MR dampers. J Sound Vib. 2009;319:753-767.
[DOI] -
7. Bai XX, Jiang P, Qian LJ. Integrated semi-active seat suspension for both longitudinal and vertical vibration isolation. J Intell Mater Syst Struct. 2017;28:1036-1049.
[DOI] -
8. Lee HS, Choi SB. Control and response characteristics of a magneto-rheological fluid damper for passenger vehicles. J Intell Mater Syst Struct. 2000;11:80-87.
[DOI] -
9. Dyke SJ, Spencer BFJr, Sain MK, Carlson JD. Modeling and control of magnetorheological dampers for seismic response reduction. Smart Mater Struct. 1996;5:565-575.
[DOI] -
10. Jing C, Youlin X, Weilian Q, Zhilun W. Seismic response control of a complex structure using multiple MR dampers: experimental investigation. Earthq Eng Eng Vib. 2004;3:181-193.
[DOI] -
11. Chen ZH, Lam KH, Ni YQ. Enhanced damping for bridge cables using a self-sensing MR damper. Smart Mater Struct. 2016;25:085019.
[DOI] -
12. Cao X, Xuan S, Li J, Li Z, Hu T, Liang H, et al. Magnetic-tunable sound absorber based on micro-perforated magnetorheological elastomer. Smart Mater Struct. 2020;29:015024.
[DOI] -
13. Choi YT, Wereley NM. Biodynamic response mitigation to shock loads using magnetorheological helicopter crew seat suspensions. J Aircr. 2005;42:1288-1295.
[DOI] -
14. Li WH, Du H, Guo NQ. Design and testing of an MR steering damper for motorcycles. Int J Adv Manuf Technol. 2003;22:288-294.
[DOI] -
15. Sun S, Deng H, Li W, Du H, Ni YQ, Zhang J, et al. Improving the critical speeds of high-speed trains using magnetorheological technology. Smart Mater Struct. 2013;22:115012.
[DOI] -
16. Desai RM, Jamadar MEH, Kumar H, Joladarashi S, Sekaran SCR. Design and experimental characterization of a twin-tube MR damper for a passenger van. J Braz Soc Mech Sci. 2019;41(8):332.
[DOI] -
17. Abdul Aziz M, Mohtasim SM, Ahammed R. State-of-the-art recent developments of large magnetorheological (MR) dampers: a review. Korea-Aust Rheol J. 2022;34(2):105-136.
[DOI] -
18. Liu B, Liu Q, Pan Y, Zhou J, Zhang J, Liu S, et al. An impact-resistant and flame-retardant CNTs/STF/Kevlar composite with conductive property for safe wearable design. Compos Part A Appl Sci Manuf. 2023;168:107489.
[DOI] -
19. Liu Q, Liu B, Pan Y, Zhang J, Wang K, Lou C, et al. Probing the roles of surface characteristic of suspended nanoparticle in shear thickening suspensions. Appl Surf Sci. 2024;659:159910.
[DOI] -
20. Zhang X, Zhou J, Wu K, Zhang S, Xie L, Gong X, et al. Simultaneous Enhancement of Thermal Insulation and Impact Resistance in Transparent Bulk Composites. Adv Mater. 2024;36(16):e2311817.
[DOI] -
21. Chen Q, Xuan S, Jiang W, Cao S, Gong X. Shear time dependent viscosity of polystyrene-ethylacrylate based shear thickening fluid. Smart Mater Struct. 2016;25(4):045005.
[DOI] -
22. Crawford NC, Williams SKR, Boldridge D, Liberatore MW. Shear-Induced Structures and Thickening in Fumed Silica Slurries. Langmuir. 2013;29(42):12915-12923.
[DOI] -
23. Gürgen S, Sert A. Polishing operation of a steel bar in a shear thickening fluid medium. Compos Part B Eng. 2019;175:107127.
[DOI] -
24. Liu B, Du C, Wang L, Fu Y, Song L. The rheological properties of multifunctional shear thickening materials and their application in vehicle shock absorbers. Smart Mater Struct. 2021;30(8):085028.
[DOI] -
25. Gürgen S, Kuşhan MC, Li W. Shear thickening fluids in protective applications: A review. Prog Polym Sci. 2017;75:48-72.
[DOI] -
26. Pan Y, Sang M, Zhang J, Sun Y, Liu S, Hu Y, et al. Flexible and lightweight Kevlar composites towards flame retardant and impact resistance with excellent thermal stability. Chem Eng J. 2023;452:139565.
[DOI] -
27. Pinto F, Meo M. Design and Manufacturing of a Novel Shear Thickening Fluid Composite (STFC) with Enhanced out-of-Plane Properties and Damage Suppression. Appl Compos Mater. 2017;24(3):643-660.
[DOI] -
28. Ye Y, Xiao H, Reaves K, McCulloch B, Mike JF, Lutkenhaus JL. Effect of Nanorod Aspect Ratio on Shear Thickening Electrolytes for Safety-Enhanced Batteries. ACS Appl Nano Mater. 2018;1(6):2774-2784.
[DOI] -
29. Wu Y, Wang W, Zhang J, Sang M, Xu Y, Zhou J, et al. Liquid or solid? a biologically inspired concentrated suspension for protective coating. Chem Eng J. 2022;428:131793.
[DOI] -
30. Morris JF. Shear Thickening of Concentrated Suspensions: Recent Developments and Relation to Other Phenomena. Annu Rev Fluid Mech. 2020;52(1):121-144.
[DOI] -
31. Dong H, Hu X, He G. A shear-thickening colloidal electrolyte for aqueous zinc-ion batteries with resistance on impact. Nanoscale. 2022;14(39):14544-14551.
[DOI] -
32. Barnes HA. Shear‐Thickening ("Dilatancy") in Suspensions of Nonaggregating Solid Particles Dispersed in Newtonian Liquids. J Rheol. 1989;33(2):329-366.
[DOI] -
33. Chang L, Friedrich K, Schlarb AK, Tanner R, Ye L. Shear-thickening behaviour of concentrated polymer dispersions under steady and oscillatory shear. J Mater Sci. 2011;46(2):339-346.
[DOI] -
34. Ding J, Tian T, Meng Q, Guo Z, Li W, Zhang P, et al. Smart Multifunctional Fluids for Lithium Ion Batteries: Enhanced Rate Performance and Intrinsic Mechanical Protection. Sci Rep. 2013;3(1):2485.
[DOI] -
35. Veith GM, Armstrong BL, Wang H, Kalnaus S, Tenhaeff WE, Patterson ML. Shear Thickening Electrolytes for High Impact Resistant Batteries. ACS Energy Lett. 2017;2(9):2084-2088.
[DOI] -
36. Chen Z, Chao Y, Sayyar S, Tian T, Wang K, Xu Y, et al. Polyethylene Oxide (PEO) Provides Bridges to Silica Nanoparticles to Form a Shear Thickening Electrolyte for High Performance Impact Resistant Lithium‐ion Batteries. Adv Sci. 2023;10(28):e2302844.
[DOI] -
37. Yuan X, Tian Y, Qian C, Ahmad S, Ma Z, Li L, et al. Rheology of magnetorheological shear thickening polishing fluids with micro diamond abrasive particles. J Magn Magn Mater. 2024;598:172065.
[DOI] -
38. Liu XQ, Bao RY, Wu XJ, Yang W, Xie BH, Yang MB. Temperature induced gelation transition of a fumed silica/PEG shear thickening fluid. RSC Adv. 2015;5(24):18367-18374.
[DOI] -
39. Royer JR, Blair DL, Hudson SD. Rheological Signature of Frictional Interactions in Shear Thickening Suspensions. Phys Rev Lett. 2016;116(18):188301.
[DOI] -
40. Huang W, Wu Y, Qiu L, Dong C, Ding J, Li D. Tuning Rheological Performance of Silica Concentrated Shear Thickening Fluid by Using Graphene Oxide. Adv Cond Matter Phys. 2015;2015:1-5.
[DOI]
Copyright
© The Author(s) 2025. This is an Open Access article licensed under a Creative Commons Attribution 4.0 International License (https://creativecommons.org/licenses/by/4.0/), which permits unrestricted use, sharing, adaptation, distribution and reproduction in any medium or format, for any purpose, even commercially, as long as you give appropriate credit to the original author(s) and the source, provide a link to the Creative Commons license, and indicate if changes were made.
Share And Cite