Abstract
Triaxial tactile sensing technology overcomes the limitations of conventional single-axis sensors by enabling real-time decoupling of normal and shear forces, thereby supporting multi-dimensional perception in robotics, wearable devices, and human-computer interaction. By integrating flexible electronics with high-density sensor arrays, this technology enables precise object manipulation, environmental mapping, and physiological monitoring. Current applications include haptic feedback in virtual reality/augmented reality, electronic skin, and robotic slip control, demonstrating high sensitivity, fast response, and high spatial resolution. The core challenge lies in simultaneously optimizing sensing performance, long-term durability, and integration feasibility. Advances in nanomaterial engineering and machine learning algorithms are improving the accuracy of force decoupling and the efficiency of signal processing. This review systematically examines the working principles, strategies for performance enhancement, data processing methods, and cross-domain applications of triaxial tactile sensing. Instead of focusing primarily on materials or individual sensing mechanisms, it highlights critical performance trade-offs and co-optimization frameworks involving sensing performance, durability, and integration, to promote the widespread adoption of intelligent tactile systems across various industries.
Keywords
1. Introduction
Triaxial tactile sensing technology enables the simultaneous measurement of three-dimensional force vectors in triaxial space[1-3]. In contrast, traditional uniaxial tactile sensors have inherent limitations: their single-axis measurement requires complex calibration procedures and restricts mechanical adaptability[4]. These limitations become particularly critical in applications involving dynamic deformation, such as soft robotics[5,6] and epidermal wearable devices[7,8]. The increasing demand for high-dimensional tactile perception is driving innovation in robotics, wearable technologies, and human-machine interaction[9-11]. Flexible electronics[12] and electronic skin (e-skin) technologies[13] enable the development of high-density sensor arrays that replicate human tactile acuity. Robots can now perform delicate tasks such as manipulating fragile objects and reconstructing 3D terrains. Concurrently, advanced composite systems such as hybrid elastomers embedded with metal particles or graphene nanosheets[6,14,15] have significantly enhanced sensor sensitivity and durability, addressing long-standing challenges in mechanical strength and signal fidelity.
Triaxial tactile sensors are particularly effective in real-time force decoupling. This capability enables the simultaneous detection of pressure and shear stress. Such real-time processing allows dynamic adaptation to environmental changes, which is essential for applications involving variable interaction scenarios, including robotic manipulation of delicate objects and responsive control of prosthetic limbs. By offering comprehensive spatiotemporal force monitoring and timely feedback, triaxial sensing technology significantly improves precision grasping, human-robot collaborative tasks, and the responsiveness of interactive systems in healthcare, virtual reality (VR), and smart device applications.
Practical implementations have demonstrated the transformative potential of this technology. In VR[16,17] and augmented reality (AR) enabled robotic teleoperation systems, embedded triaxial force sensors capture environmental interaction signals to reconstruct accurate virtual object dynamics. This real-time force-moment feedback enables precise human-robot collaborative control and enhances the immersive user experience through synchronized mapping between virtual and physical interactions. E-skin devices utilize these sensors to replicate the mechanoreceptive functions of human skin[18,19], enabling naturalistic environmental interaction in both prosthetic and robotic applications. Wearable applications show similar versatility. For example, in tactile feedback bracelets, the sensors deliver real-time physical sensations to the user, facilitating intuitive control in digital environments. These sensors are also widely integrated into wearable health monitors for continuous physiological signal tracking with medical-grade accuracy[20,21]. Robotic manipulation systems, in particular, benefit from real-time slip detection based on the monitoring of tangential-to-normal force ratios. This enables autonomous adjustment of grip force to maintain object stability during high-speed operations (Figure 1). In summary, these cross-domain applications collectively demonstrate the unique capability of triaxial tactile sensors for self-decoupled 3D force measurement, which forms a foundational component of next-generation robotics and wearable devices[22].
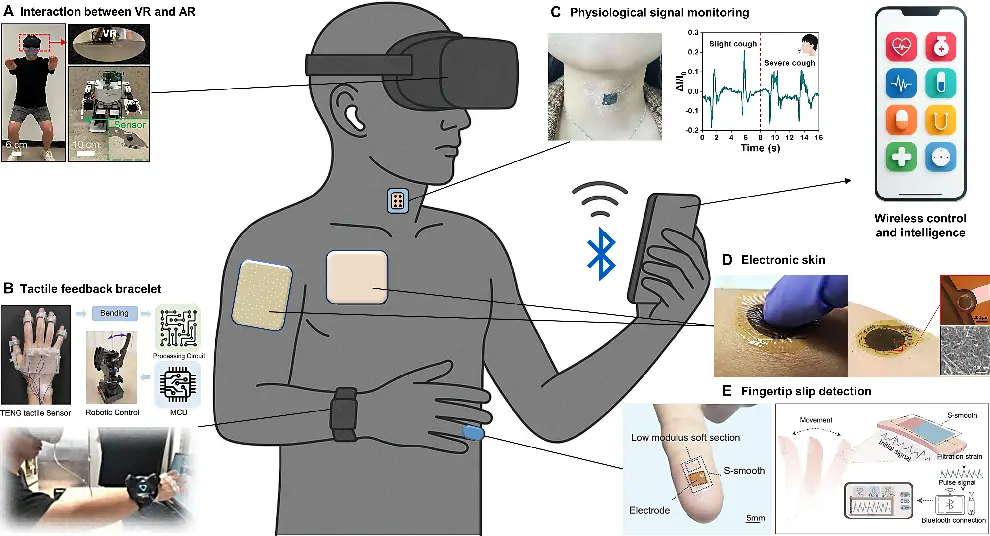
The operational superiority of triaxial tactile sensors is demonstrated through three primary performance metrics[3,28]. Their spatial resolution capability of 15 μm, exceeding that of the human fingertip, enables precise detection and differentiation of tactile stimuli, which is essential for high-precision industrial manipulation and sophisticated human-machine interaction[29] (Figure 2A). Mechanical robustness is demonstrated by consistent signal stability under prolonged cyclic loading exceeding 50,000 cycles, as well as across varying environmental conditions[30] (Figure 2B). Furthermore, detection fidelity is ensured by a remarkable sensitivity of 3.5 kPa-1 in the low-pressure range (0-50 Pa) and 0.134 N-1 for tangential force detection (0-0.5 N) (Figure 2C), allowing precise quantification of forces along multiple sensing axes[31].
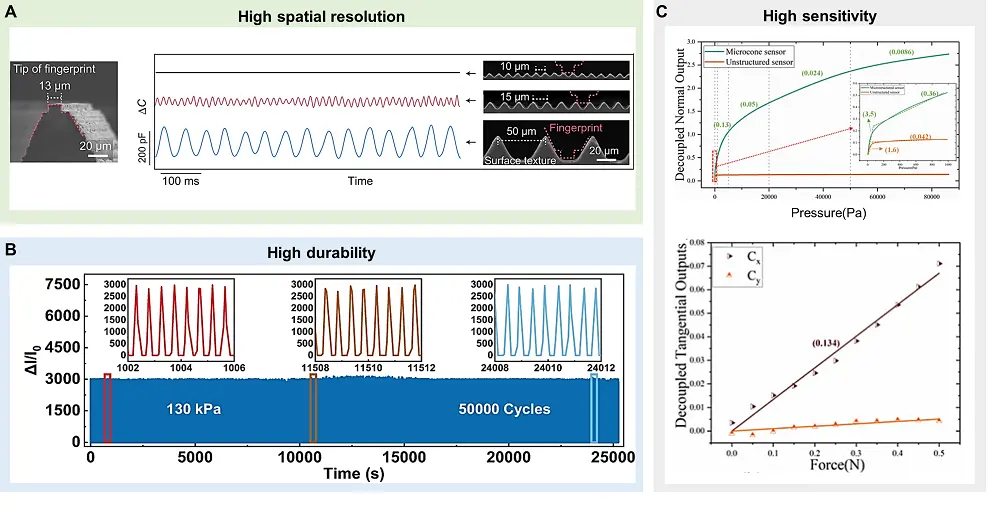
Despite these advancements, critical challenges remain in balancing the three key requirements of performance optimization, operational reliability, and integration feasibility. Achieving high performance demands advanced nanomaterial engineering strategies that enhance sensitivity and dynamic range while minimizing inter-axis crosstalk. Inter-axis crosstalk continues to be a persistent issue in multi-dimensional force measurement. Ensuring long-term durability requires sensor systems that maintain signal stability under prolonged mechanical stress and environmental fluctuations, operating without degradation or failure. Integration challenges focus on developing compact, cost-effective sensor architectures that maintain functional compatibility across diverse platforms, including robotic manipulators, VR haptic interfaces[32], and medical monitoring systems[33,34]. Addressing these multi-dimensional requirements calls for innovations in composite material design, sensor structure engineering, and adaptive signal processing algorithms. The ultimate industrial adoption of triaxial tactile sensing technology depends on resolving the inherent trade-offs among these interdependent parameters.
This review begins by systematically examining the diverse applications of triaxial tactile sensing across multiple domains, with particular emphasis on robotics and wearable systems. The analysis then shifts to foundational operational principles, focusing on the Force Decoupling Principle, the key mechanism that enables independent measurement of multi-dimensional forces. Current research predominantly employs seven force sensing modalities: piezoresistive, piezoelectric, capacitive, triboelectric, optical, magnetic, and pneumatic approaches. Force decoupling strategies discussed in this review are categorized into five groups: structural design, electrical signal decoupling, magnetic force decoupling, optical force decoupling, and machine learning-based decoupling. These methodologies enable separation of force signals in three dimensions, allowing independent measurement and analysis of forces along each axis.
To address existing research gaps, our work establishes a comprehensive analytical framework examining working principles, performance enhancement, and data processing methods, with particular emphasis on machine learning’s role in force decoupling and signal processing. Rather than focusing primarily on materials, applications, or individual sensing mechanisms, we introduce a co-optimization framework that tackles the challenge of balancing sensing performance, long-term durability, and integration feasibility, an area requiring further attention in current literature. This integrated approach provides researchers with a systematic technical roadmap to advance triaxial tactile sensing toward practical implementations in intelligent systems.
The following sections explore performance enhancement strategies for triaxial tactile sensors, focusing on improving sensitivity, spatial resolution, detection range, and operational durability. A subsequent analysis examines the expanding role of machine learning in tactile signal processing, discussing how neural network architectures, including convolutional neural network (CNN), deep neural network (DNN), long short-term memory (LSTM), and Visual Geometry Group (VGG) network, enable advanced functionalities such as surface texture characterization, material stiffness assessment, object morphology recognition, and physiological signal interpretation.
The final section evaluates the integration and emerging opportunities of triaxial tactile sensors across four application frontiers: human-machine interaction interfaces, biomimetic e-skin[35], tactile-based cryptographic systems, and adaptive pressure feedback. The concluding section assesses the strengths and current limitations of this technology while proposing future research directions and challenges. Through this comprehensive analysis, the review provides researchers and engineers with actionable insights to advance triaxial tactile sensing toward practical, large-scale implementations in next-generation intelligent systems.
2. The Working Principle of Tactile Sensors
Triaxial tactile sensing technology has evolved from rudimentary single-axis pressure detection to advanced systems capable of multi-dimensional force analysis. This chapter elucidates the core operational principles of triaxial tactile sensors, focusing on various force sensing mechanisms that enable precise force detection across multiple axes. The discussion covers piezoelectric[36-40], capacitive[41-44], piezoresistive[45-48], triboelectric[49-51], optical[52-55], and magnetic[56-59] sensing modalities, elaborating on their respective mechanisms for accurate multi-directional force detection. Furthermore, the chapter highlights the critical role of force decoupling in improving measurement accuracy and system stability.
2.1 The working principle of triaxial tactile sensor
The evolution of tactile sensing technology has transformed basic uniaxial pressure detection into comprehensive multidimensional force analysis. Traditional mechanical multi-axis force sensors measure triaxial forces, including normal and shear components, by combining precisely engineered mechanical structures with strain gauge or piezoelectric signal conversion. These systems fundamentally rely on two elements: the sensor body's structural design and the transduction mechanism that converts mechanical deformation into electrical signals. The piezoelectric six-dimensional force sensor[60] detects force and torque through a spoke structure composed of multiple piezoelectric sensing elements arranged symmetrically. When subjected to multidirectional forces or torques, these elements generate charges proportional to mechanical stress via the piezoelectric effect. Although such rigid six-axis sensors[61-63] demonstrate industrial-grade reliability, their limitations become evident in interaction scenarios. The inherently rigid structures hinder adaptation to deformable surfaces such as biomimetic robotic skin or smart textiles. Operational constraints also arise in dynamic environments due to complex calibration requirements and material degradation under extreme conditions.
Modern triaxial tactile systems overcome these limitations by employing diverse sensing principles, including resistive, capacitive, magnetic, optical, piezoelectric, triboelectric, and pneumatic mechanisms.
Pneumatic sensors detect the magnitude and variation of external forces through deformation of an elastic gas chamber under force loading, which causes changes in the volume or pressure of the internal gas. Figure 3A illustrates the BaroTac three-axis tactile sensing system[64], where multiple barometric sensors are arrange on a printed circuit board, with soft materials cast onto them in a dome shape. Externally applied forces deform the elastic dome, inducing pressure variations within individual chambers. Directional force discrimination is achieved by analyzing differential pressure responses across spatially distributed sensors, enabling independent forces measurement along the X, Y, and Z axes.
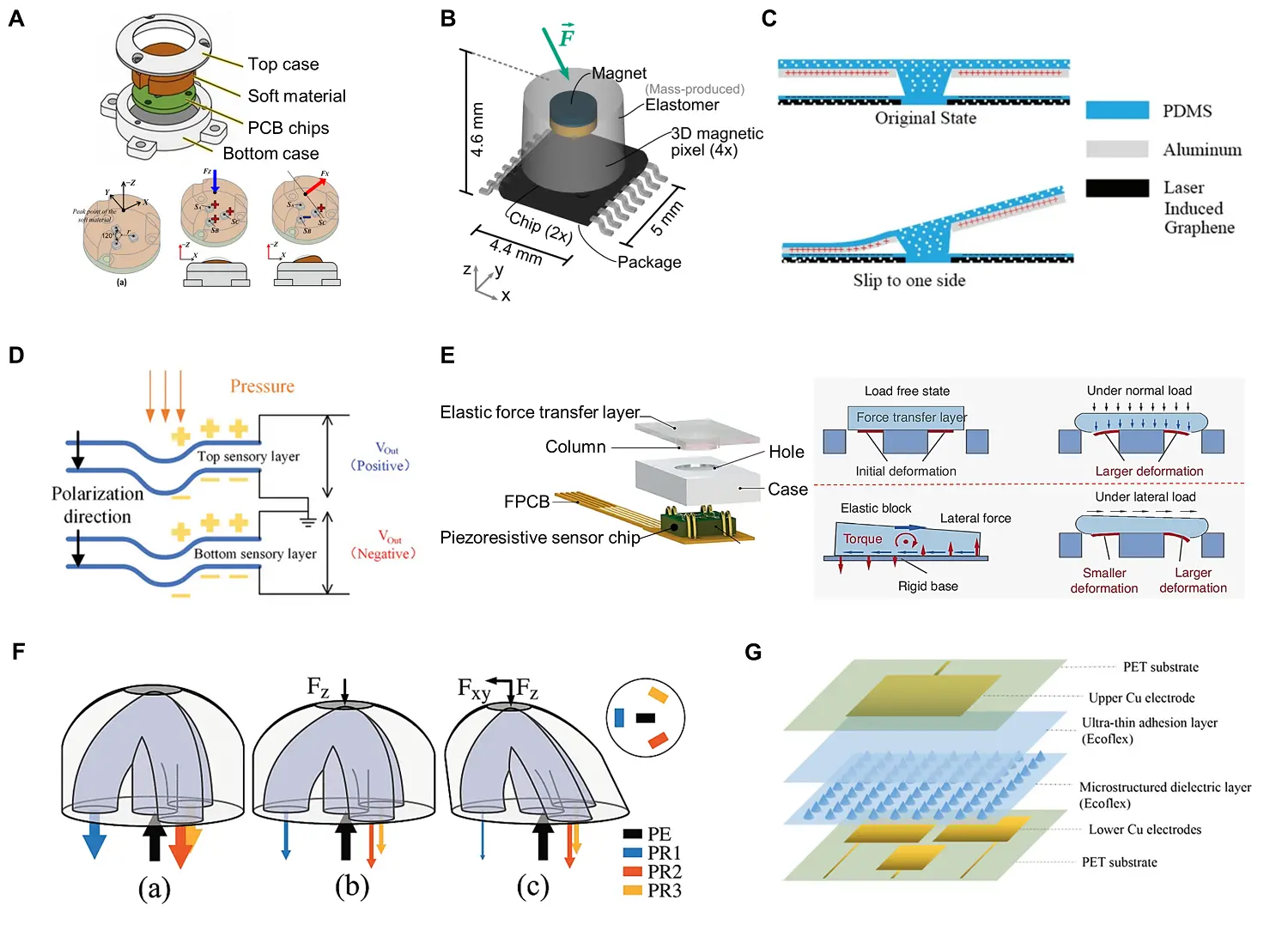
Figure 3. The principle of triaxial tactile sensors. (A) Barometric three-axis tactile sensor[64]; (B) Magnetic triaxial tactile sensor[58]; (C) Triboelectric triaxial tactile sensor[65]; (D) Piezoelectric triaxial tactile sensor[66]; (E) Piezoresistive triaxial tactile sensor[67]; (F) Optical triaxial tactile sensor[68]; (G) Capacitive triaxial tactile sensor[31]. PDMS: polydimethylsiloxane; PCB: printed circuit board; FPCB: flexible printed circuit board; PET: polyethylene terephthalate; PE: light emitter; PR: light detector .
Magnetic sensors track force-induced magnetic field changes using Hall effect elements, reflecting the magnitude and variation of the applied force. As illustrated in Figure 3B, the sensor consists of a neodymium magnet embedded within an elastomeric matrix positioned above a magnetometer chip[58]. External force applied to the sensor surface causes deformation of the elastomer, resulting in displacement of the magnetic element and alteration of the magnetic field distribution. An integrated array of four three-dimensional magnetic sensing pixels detects these variations in the field pattern with high precision. Through differential signal processing, the system effectively eliminates environmental magnetic interference, ensuring robust measurement capabilities even in electromagnetically complex environments.
Triboelectric sensors operate based on the electrostatic induction effect. When dissimilar materials come into contact under an external force, differences in electron affinity cause charge transfer, generating equal and opposite charges on their surfaces. Due to this charge imbalance, subsequent separation of the materials creates measurable potential differences. As the contact area or distance changes under external forces, the resulting variation in electric potential induces an instantaneous current signal in the external circuit, thereby converting mechanical energy into an electrical signal correlated with force magnitude. As shown in Figure 3C, the sensor’s operation relies on the contact charging phenomenon[65]. Contact electrification occurs at the metal-polymer interface, generating immobilized surface charges. When slip occurs, the seesaw structure induces asymmetric electrode contact, creating an electric field imbalance and consequent charge induction on the bottom electrode. This potential difference generates quantifiable voltage signals whose amplitude directly correlates with slip velocity.
Piezoelectric sensors utilize the direct piezoelectric effect, converting mechanical stress into electrical signals. When subjected to externally applied forces, the internal dipole moment in piezoelectric materials changes, generating a potential difference at the two ends of the material that reflects the magnitude and variation of the applied force. As illustrated in Figure 3D, the functional mechanism of the sensor[66] relies on the piezoelectric properties of polyvinylidene fluoride: mechanical deformation causes polarization displacement within the molecular structure, resulting in surface charge accumulation proportional to the deformation strain. Strategically positioned electrodes collect these charges, which the system converts into measurable voltage signals. This enables precise discrimination between diverse mechanical stimuli. This transduction pathway offers high sensitivity and excellent response linearity across a wide dynamic range of applied forces.
Piezoresistive sensors’ function based on the piezoresistive effect, where applied force causes strain-mediated rearrangement of conductive particles within the material, resulting in resistance changes for precise force detection. The sensor[67]shown in Figure 3E consists of four cantilever-mounted piezoresistive sensor chips that exhibit resistance changes under directional loading. Normal forces induce uniform beam deflection, whereas shear forces create asymmetric strain distributions and corresponding resistance changes. Wheatstone bridge circuits resolve these resistance variations into orthogonal force components.
Optical sensors capture changes in light signals such as intensity, wavelength, phase or image by utilizing principles of optical diffraction, interference, or reflection. These changes are used to sense contact force or deformation. An optical sensor[68] shown in Figure 3F employs a hemispherical architecture combining a central photon emitter with three radially arranged photodetectors. Normal forces uniformly increase light absorption in transparent channels, while shear forces generate directional absorption anisotropy. Three photodetectors spaced 120° apart quantify these intensity variations to determine force vectors.
Capacitive sensors accurately detect external loads by measuring force-induced changes in capacitance. These changes result from variations in the area of the capacitor plates, the distance between the plates, or the dielectric constant. A capacitive triaxial tactile sensor[31] (Figure 3G) based on micro-conical structures operates on parallel-plate capacitance principles, comprising a single top electrode and three bottom electrodes that form discrete capacitive units. When external forces are applied, normal components reduce the inter-electrode spacing, simultaneously increasing the capacitance values across all three units. Tangential components, in contrast, induce lateral displacement of the top electrode, altering the electrode-overlap geometry and generating characteristic differential capacitance patterns.
Table 1 provides a systematic comparison of seven force decoupling mechanisms, revealing distinct performance trade-offs that guide optimal sensor selection. Sensitivity characteristics vary significantly: capacitive mechanisms demonstrate the highest sensitivity (50-100 kPa-1) for precision applications, while other mechanisms, though exhibiting relatively lower sensitivity, offer unique advantages in cost-effectiveness, environmental tolerance, or specialized capabilities. Response characteristics differ markedly: fast-response mechanisms (< 10 ms), including piezoelectric, optical, and magnetic sensors, are suitable for dynamic applications; medium-response sensors (10-100 ms), encompassing resistive, capacitive, and triboelectric mechanisms, satisfy most tactile sensing requirements; pneumatic sensors exhibit slower response times (> 100 ms) but remain applicable for specific industrial scenarios. Cost-performance considerations show that resistive sensors enable the lowest-cost mass production, while optical and pneumatic systems require higher investment for specialized precision needs. Size and durability factors further influence selection: compact mechanisms (resistive, capacitive, triboelectric) suit space-constrained applications, multi-component mechanisms demand larger integration space, and high-durability solutions (magnetic, piezoelectric) excel in harsh environments. This systematic analysis demonstrates that optimal sensor selection requires application-specific trade-off optimization based on the relative importance of sensitivity, response time, cost, size, and durability.
Sensing mechanism | Sensitivity | Response time | Cost | Size | Durability | Main applicable scenarios |
Piezoresistive | < 100 kPa-1 | 10-50 ms | Low | Compact | Low | Static pressure measurement |
Capacitive | < 100 kPa-1 | 20-80 ms | Low | Compact | Medium | Static/micro-motion precision measurement |
Magnetic | < 5 kPa-1 | < 10ms | Average | Medium | High | Non-contact detection |
Optical | < 10 kPa-1 | < 5ms | High | Multi-component | Medium | Ultra-precision measurement |
Piezoelectric | < 10 kPa-1 | < 1ms | Average | Medium | High | Dynamic force/vibration/shock measurement |
Triboelectric | < 1 KPa-1 | 30-90 ms | Average | Compact | Low | Micromechanical energy collection and sensing |
Pneumatic | < 5 kPa-1 | 100ms | High | Multi-component | Medium | Rough measurement in harsh environment |
The main parameter range based on the parameter statistics of most of these sensors.
Collectively, these sensing modalities have significantly enhanced the performance of triaxial tactile sensors while expanding their potential applications across robotics, wearable systems, and human-machine interfaces.
2.2 Force decoupling mechanisms
A pivotal advancement in triaxial tactile sensing lies in the effective decoupling of multi-directional force components. Contemporary force decoupling strategies integrate three synergistic approaches: (1) specialized structural optimization for mechanical signal separation, (2) material engineering for directional response, and (3) computational intelligence via machine learning algorithms. Table 2 lists the force decoupling principles of several representative sensors. These approaches fundamentally enable independent quantification of normal (Z-axis) and shear (X/Y-axis) forces within a unified sensing system, critical for applications requiring high-fidelity tactile feedback in dynamic environments such as robotic manipulation, adaptive prosthetics, and interactive wearable systems. By eliminating inter-axis signal interference, these mechanisms collectively enhance measurement accuracy while improving system responsiveness.
Triaxial tactile sensor | Fabrication methods | Decoupling principle | Spatial resolution | Normal sensitivity | Shear sensitivity | Robustness | Minimum detection limit | Flexible integration capability | Typical application scenarios |
[19] | Microfabrication | Structural design | 6 μm | GF = 27.8 (At a strain of 0-40%) GF = 1,084 (At a strain of 40%-90%) GF = 9617 (At a strain of 90%-120%) | 2.21 N-1 (0-0.4N) | 2 Pa | Yes | Wearable electronics | |
[29] | Microfabrication | Structural design | 15 μm | 519 kPa-1 (0-20 kPa) | 10,000 cycles | Yes | Wearable electronics | ||
[30] | Microfabrication | Structural design | 24.6 kPa-1 (0-1,500 kPa) | 50,000 cycles | 1 Pa | Yes | Robotic manipulation | ||
[31] | Multi-layer stacking | Structural design | 3.5 kPa-1 (0-50 Pa) 0.36 kPa-1 (0.05-1 kPa) 0.13 kPa-1 (1-5 kPa) 0.05 kPa-1 (5-20 kPa) | 0.134 N-1 (0-100 Pa) | Repeated loading over 1h | 1 Pa | Yes | Robotic manipulation | |
[35] | Multi-layer stacking | Structural design | 0.117 mm | 5 × 10-5 kPa-1 (0-80 kPa) | 6 × 10-4 N-1 (0-80 kPa) | 3,000 cycles | 1 Pa | Yes | Wearable electronics |
[27] | Microfabrication | Structural design | 92.76 kPa-1 (0-6.77 kPa) 34.35 kPa-1 (6.77-16.38 kPa) 16.03 kPa-1 (16.38-31.23 kPa) 7.38 kPa-1 (16.38-50.93 kPa) | 50,000 cycles | 0.9 Pa | Yes | Human-computer interaction | ||
[52] | Microfabrication | Optical decoupling | 160 μm | 0.14 N-1 (0-0.4 N) | 0.21 N-1 (0-0.4 N) | 700 cycles | 120 μN | Yes | Human-computer interaction |
[73] | Multi-layer stacking | Electrical decoupling | 12.2 mm | 54.31 kPa-1 (0-500 Pa) 30.11 kPa-1 (0.5-10 kPa) 8.42 kPa-1 (10-40 kPa) 1.03 kPa-1 (40-115 kPa) | 5,400 cycles | 0.1 Pa | Yes | Human-computer interaction | |
[75] | Multi-layer stacking | Electrical decoupling | 100 μm | 71.37 kPa-1 (< 100 Pa) | 4 Pa | Yes | Healthcare and Biomedical Monitoring | ||
[84] | Modular assembly and integration | Machine learning | 5,000 cycles | 0.9 Pa | No | Robotic manipulation | |||
[28] | Microfabrication | Electrical decoupling | 2,093 kPa-1 (0-60 kPa) | 10,000 cycles | 0.43 mN | Yes | Wearable electronics |
GF: gauge factor (strain sensitivity).
Various mature strategies exist to achieve effective force decoupling, including structural engineering, optical methods, magnetic sensing, electrical signal processing, and machine learning algorithms. Structural approaches leverage specific geometries or multilayer architectures to direct forces to discrete sensing regions, minimizing crosstalk. As illustrated in Figure 4A, the force decoupling mechanism of the microcone-structured capacitive sensor[31] relies on the distinctive geometric deformation characteristics of the elastomeric microcones. The sensor employs specialized mathematical algorithms to process differential capacitance variations induced by normal and tangential forces, enabling precise discrimination of triaxial force components. This innovative structural design effectively mitigates signal crosstalk limitations and ensures isotropic response sensitivity to tangential forces in any direction within the XY plane. Furthermore, the electrode configuration minimizes interconnection complexity, facilitating high-density sensor arrays that provide robust tactile feedback for precision robotic manipulation tasks. Nevertheless, this approach is fundamentally constrained by stringent requirements for nanoscale manufacturing precision and the inherent susceptibility of elastomeric materials to long-term fatigue degradation, limiting its applicability primarily to controlled environments such as precision assembly operations and high-end tactile sensor arrays. Additionally, the absence of standardized evaluation criteria for balancing structural complexity against manufacturing costs continues to impede scalable deployment of this technology.
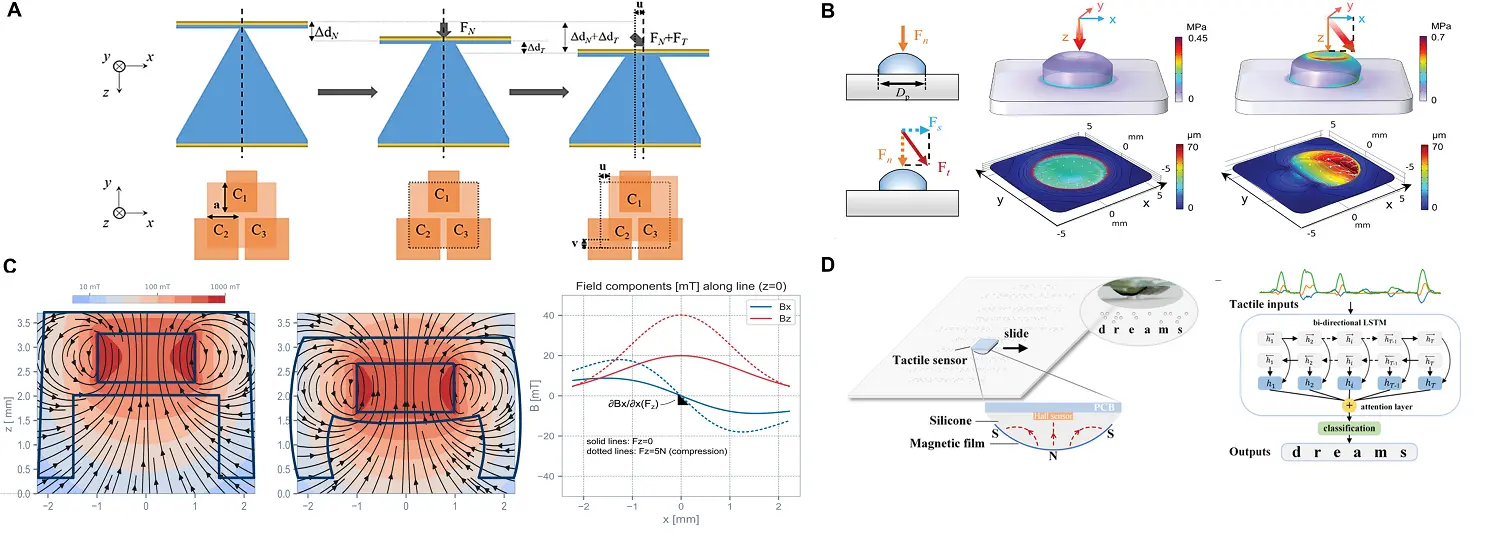
Optical techniques utilize components such as optical fibers or diffractive surfaces to convert force-induced mechanical deformations into quantifiable optical signal variations, enabling multidirectional force detection. The representative optical sensor[52] depicted in Figure 4B incorporates U-shaped optical micro-nano fibers (MNF) embedded within an elastic polydimethylsiloxane (PDMS) polymer film. Under vector force inputs, the MNF undergoes anisotropic bending deformations that cause changes in light transmission. Through time-resolved analysis of these optical signal variations, the system enables simultaneous detection of normal and shear force components, with the asymmetric fiber geometry providing inherent directional sensitivity to shear forces. Detection sensitivities for normal and shear forces reach 50.7 dB N-1 and 82.2 dB N-1, respectively. Experimental results demonstrate that this optical approach reduces inter-axis signal crosstalk while enhancing sensitivity and directionality of force detection, making it suitable for high-performance haptic visualization and human-machine interface applications. Despite these advantages, optical methods are inherently limited by susceptibility to environmental perturbations, including optical source instability and fiber fragility, restricting their use mainly to controlled laboratory environments and specialized high-precision applications rather than robust industrial deployments. Moreover, ongoing debates regarding optimal wavelength selection strategies and the fundamental trade-off between measurement sensitivity and mechanical durability remain unresolved, hindering the establishment of standardized design solutions for diverse application requirements.
Magnetic decoupling relies on magnetic sensors to monitor force-induced changes in magnetic fields, with sensor arrangements designed to isolate distinct force components. Figure 4C shows a triaxial magnetic sensor for robot grasping and slip detection[65]. The working principle of this sensor involves embedding a magnet into a deformable elastic body installed on the magnetometer chip. When force is applied, the elastic body deforms, causing the magnet to shift and modulate the magnetic field pattern. The system uses a differential operation mechanism to decouple triaxial force data. The multi-pixel design forms a square array with four three-dimensional magnetic pixels. This configuration achieves accurate sensing of X and Y shear forces while suppressing stray magnetic fields. However, magnetic approaches are inherently limited by triaxial field coupling phenomena and susceptibility to external electromagnetic interference. These characteristics make them particularly suitable for demanding industrial applications. Furthermore, optimizing the trade-off between magnetic field strength and power consumption remains an unresolved challenge, which is especially critical for portable and battery-operated sensing systems.
Electrical methods employ capacitors, resistors, or piezoelectric elements to detect forces, combined with signal processing algorithms for effective triaxial component separation. The dual triboelectric nanogenerator force sensor[50] incorporates curved PDMS-Cu interface structures with silver nanowire (AgNW) electrode arrays. Under normal force loading, complete contact between the upper curved structure and the lower modified PDMS friction layers generates uniform charge transfer, while shear forces create asymmetric contact area distributions across the AgNW electrodes. Upon release of the multidimensional force, the contact position shifts, causing differentiated charge flow toward the ground. By real-time monitoring of electron flow within circuits, the system dynamically reconstructs force vectors. A key limitation lies in inter-channel signal crosstalk and susceptibility to electromagnetic noise. This makes these sensors particularly suitable for cost-sensitive large-scale deployments and low-power applications. Current debates focus on analog versus digital signal processing strategies, as well as optimal filtering approaches.
Machine learning techniques, particularly deep learning-enhanced decoupling strategies, address complex nonlinear signal interactions in unstructured environments. They can analyze high-dimensional sensor data to dynamically differentiate triaxial forces in real time. Figure 4D shows the arc-shaped tactile sensor system and its use of machine learning for triaxial force decoupling[69]. The tactile sensor consists of a flexible magnetic film, a silicone elastomer sheet, and a Hall sensor embedded on a printed circuit board. When external force is applied to the magnetic film, changes in magnetic flux density are detected by the Hall sensor. The system employs a bidirectional LSTM neural network with an attention mechanism. As the sensor slides over different textures, the 3D tactile signal sequence captures both normal and shear contact information. The attention layer helps the LSTM network focus on particular parts of the tactile signals that distinguish similar patterns. This approach achieved impressive recognition accuracies of 97% for Braille characters and 99% for 60 different fabric types. These methods face challenges including extensive training data requirements and limited cross-platform generalization. They excel in adaptive robotic systems and complex unstructured environments where traditional methods cannot capture nonlinear relationships. Current debates focus on network architecture selection and the fundamental trade-off between model interpretability and complexity.
These diverse force decoupling strategies have significantly advanced triaxial tactile sensing capabilities. Each approach presents distinct trade-offs among performance, complexity, and applicability. Structural and optical methods excel in precision applications, while magnetic and electrical approaches offer advantages in robust industrial environments. Machine learning techniques provide adaptability for complex scenarios but require substantial computational resources. Together, these complementary technologies are enabling next-generation applications across human-robot collaboration, prosthetic interfaces, and wearable health monitoring systems.
3. Tactile Sensor Performance Optimization
The performance of triaxial tactile sensors is critical to their success in applications such as robotics, wearable devices, and human-computer interaction. Optimizing essential performance parameters[10], such as sensitivity and spatial resolution, plays a pivotal role in enhancing the efficiency and reliability of these sensors. Table 2 compares the key performance metrics of several representative sensors, including sensitivity, minimum detection limit, spatial resolution, and robustness. However, these parameters exhibit intricate interdependencies, where optimizing one often compromises others. Achieving an optimal balance among these metrics remains central to developing high-performance tactile sensing systems.
One of the core challenges in tactile sensor development lies in enhancing performance to meet escalating requirements for triaxial measurement accuracy and real-time responsiveness. This chapter focuses on several key optimization strategies, including innovations in structural design[69-71] and material selection[72]. Through detailed analysis of these methods, we demonstrate how they effectively improve overall sensor performance and provide technical support for practical applications in related fields.
3.1 Sensitivity and range
The inverse relationship between force sensitivity and measurement range constitutes a fundamental design constraint in force sensor development. Sensitivity represents the minimum detectable force variation to a certain extent, enabling precise resolution of subtle tactile stimuli, particularly critical in low-pressure regimes (< 10 kPa). Conversely, measurement range denotes the maximum measurable force while maintaining linear response characteristics, which is essential for applications involving high-intensity mechanical interactions.
This theoretical constraint manifests practically through observable performance variations across different operational conditions. Tactile sensors universally exhibit segmented response characteristics, wherein sensitivity varies significantly across operating pressure ranges. Specifically, low-pressure regimes demonstrate high sensitivity with excellent linearity, whereas high-pressure regimes experience substantial sensitivity degradation due to sensing mechanism saturation, where microstructural compression nears physical limits, and material nonlinearity. For instance, an ionic gel capacitive sensor[73] displays characteristic performance of “54.31 kPa-1 for < 0.5 kPa; 1.03 kPa-1 for 40-115 kPa” (Table 2), representing a 50-fold sensitivity decrease that fundamentally constrains sensor performance optimization potential.
These parameters exhibit inherent interdependencies. Enhancing sensitivity typically reduces the maximum detectable force due to premature signal saturation or distortion. Conversely, extending the dynamic range often diminishes the sensor’s ability to detect small force variations, thereby lowering force resolution and sensitivity. The key optimization challenge lies in balancing these two parameters, improving sensitivity in low-pressure ranges while maintaining stability under higher pressures—an enduring difficulty in triaxial tactile sensor design.
Various strategies have been developed to optimize the sensitivity and range of triaxial tactile sensors. Material engineering provides foundational optimization pathways. Highly conductive materials such as metal micro/nanoparticles, graphene, and carbon nanotubes amplify charge transfer efficiency through quantum tunneling effects, significantly enhancing sensitivity. Complementary sensor structural designs, particularly microscale conical protrusions or hierarchical structures, achieve nonlinear contact area expansion under progressive mechanical loading, thereby extending dynamic measurement ranges through geometrically modulated resistance or capacitance variations. By integrating these multidimensional optimization strategies, tactile sensor performance can be significantly enhanced, enabling a balance between sensitivity and range to address the varying requirements of advanced application scenarios.
Figure 5A illustrates the fundamental mechanism underlying the “nonlinear synergy” strategy that enables simultaneous high sensitivity and wide linear range in the double-sided pyramidal carbon foam@stiffness regulator (DPyCF@SR) sensor[30]. The DPyCF sensing layer exhibits nonlinear piezoresistive behavior, yielding enhanced sensitivity at low strain values. Complementarily, the Ecoflex rubber SR demonstrates nonlinear elasticity, manifesting progressive stiffening under compressive loading. When these two nonlinear characteristic parameters (α and β) converge and meet the conditions, the sensor sensitivity becomes independent of strain, thereby achieving ideal linearity. Through precise engineering of the attenuation constant and stiffening constant, this sensor successfully transforms inherently contradictory material properties into synergistic advantages, resulting in a device with exceptional sensitivity (24.6 kPa -1) across an unprecedented linear range (1.4 MPa).
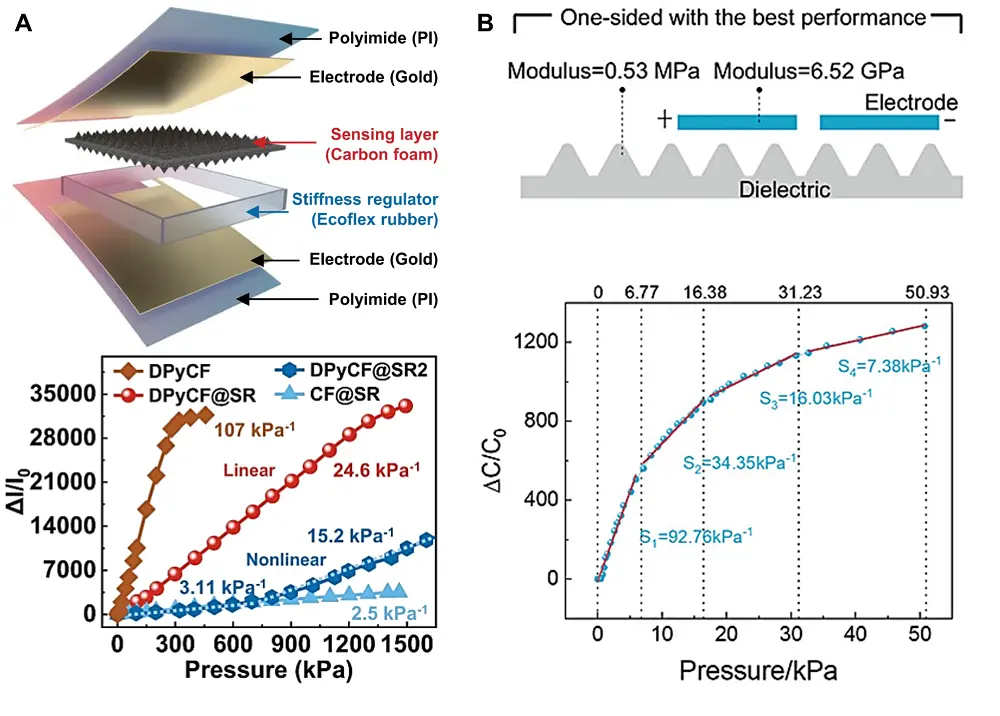
The S-smooth sensor[27] achieves exceptional sensitivity through a hierarchically optimized structural design (Figure 5B). By employing a coplanar electrode configuration rather than conventional sandwich structures, the sensor establishes an effective sensing interface that minimizes mechanical constraints during deformation. A critical innovation lies in the incorporation of a conductive lubricating layer that reduces the interfacial friction coefficient from 0.5 to approximately 0.1, thereby preserving microstructural integrity during operation. This structural optimization creates a synergistic effect among the modulus gradient, interfacial properties, and microarchitecture, ultimately yielding a remarkable sensitivity of 92.76 kPa-1 while maintaining excellent operational stability. The enhanced performance enables precise detection of subtle physiological signals, including characteristic features of arterial pulse waveforms such as percussion, tidal, and diastolic waves, which are essential for comprehensive cardiovascular monitoring.
A sensor structural design inspired by the Calathea zebrine leaf exemplifies this synergistic optimization approach. This bioinspired sensor design[73] employs soft lithographic replication techniques to transfer the natural conical microstructures of leaves onto microstructured ionic gel substrates. The hierarchical microstructure induces increasing contact area during mechanical compression, thereby generating nonlinear enhancements in electrochemical double-layer (EDL) capacitance. Under low-pressure conditions (< 0.5 kPa), the minimal initial contact area between conical protrusions and counter electrodes enables high sensitivity up to 54.31 kPa-1 through steep capacitance-pressure curve gradients. As applied pressures increase, the geometric deformation transitions from tip-contact to full-surface contact, maintaining > 1 kPa-1 sensitivity across a wide pressure range from 0.1 Pa to 115 kPa. The structural uniformity and manufacturing reproducibility of these microstructures ensure exceptional long-term stability, enabling accurate responses to both low and high pressures. Crucially, the structural optimization prevents saturation and distortion under higher pressures. This biomimetic approach effectively balances sensitivity and range, ensuring reliable performance in applications such as human-machine interaction and tactile sensing.
Structural decoupling strategies further optimize parameter balancing. An advanced magnetic decoupling approach employs two sinusoidally magnetized flexible magnetic films[74]. Specifically, two orthogonally magnetized films create a self-decoupling magnetic field distribution in triaxial space through superposition. The polarization pattern of the magnetic films changes before and after superposition. Simulation results demonstrate that the magnetic flux densities along the X, Y, and Z axes are effectively regulated after superposition. This self-decoupling mechanism simplifies the sensor’s mechanical structure and optimizes the balance between sensitivity and range. This innovative design permits customizable sensitivity-range profiles through parametric adjustments of elastic layer thickness, Young’s modulus, and magnetic domain periodicity, thereby meeting diverse application requirements.
Advanced composite systems demonstrate the synergistic potential of combined material and structural optimization strategies. The sea-urchin-shaped metal nanoparticle/polyurethane hybrid composite[75] leverages electric field enhancement effects to amplify quantum tunneling currents. These effects significantly increase sensitivity, particularly at low concentrations of conductive fillers, ensuring high responsiveness even under low-pressure conditions. Concurrently, microcones or microdome arrays across the composite surface induce progressive contact area expansion under increasing loads, further enhancing sensitivity. Through optimized combinations of materials and microstructural designs, tactile sensors can achieve both high sensitivity and wide measurement range, supporting diverse application requirements ranging from epidermal pressure mapping in health monitoring to precision force control in human-machine interaction systems.
Furthermore, capacitive sensors and microstructured sensors demonstrate superior detection limits compared to other sensor types, primarily due to efficient signal amplification mechanisms. Capacitive sensors achieve signal enhancement through the dual effects of dielectric constant variation and electrode spacing modulation. Ionic capacitive mechanisms, such as those in the S-smooth sensor (0.9 Pa detection limit)[27], enable the formation of EDL structures at the nanoscale, generating specific capacitances orders of magnitude higher than conventional geometric capacitors. This produces substantial responses to minute pressure variations. Microstructured designs, exemplified by the microcone sensor (1 Pa detection limit)[31], exploit geometric stress concentration principles, focusing macroscopic pressures into microscopic regions to achieve thousand-fold local stress amplification. When combined with ultra-soft material substrates, these designs enable detection systems to capture sufficient structural changes induced by minimal external forces. These mechanisms achieve effective physical or chemical amplification during signal transduction, thereby surpassing the intrinsic response limitations of materials found in conventional sensors (2-9.5 Pa detection limits).
Beyond detection limits, dynamic range (dimensionless, defined as the ratio of measurement range to detection limit) serves as another critical performance metric for sensor evaluation. The DPyCF@SR sensor exhibits the largest dynamic range (1,400,000)[30], primarily due to nanocomposite material design strategies and progressive failure mechanisms. Composite material sensors leverage the synergistic effects of multiphase materials to maintain sensitivity under low pressure while enhancing material load-bearing capacity up to 1.4 MPa. Fiber-reinforced phases provide mechanical strength support, porous matrix phases enable pressure response, and surface-functionalized layers optimize interfacial properties. Progressive failure design enables sensors to exhibit distinct response modes across different pressure regimes, preventing catastrophic performance loss and extending detection range to the MPa level. In contrast, sensors based on single materials or simple geometric structures, such as the microcone sensor (dynamic range of 85,000) and interlocking sensors (dynamic range of 12,500), are constrained by intrinsic mechanical properties, making it challenging to achieve ultra-wide measurement ranges while maintaining high sensitivity.
In summary, innovations in material optimization and structural design have not only enhanced sensor sensitivity but also expanded their measurement range through optimized design parameters. These improvements are fundamental for achieving high-performance tactile sensing, enabling precise detection across a wide variety of complex environments and applications.
3.2 Spatial resolution and mechanical durability
A notable trade-off exists between spatial resolution and mechanical durability in tactile sensor design. Spatial resolution, defined as the minimum distinguishable distance between adjacent tactile stimuli, directly governs a sensor’s ability to detect fine surface textures and localized force gradients. This parameter is typically enhanced through two primary strategies: increasing the sensor array density or reducing the spacing between individual sensing units. High spatial resolution is indispensable for applications requiring high tactile fidelity, including robotic material discrimination, prosthetic tactile feedback systems, and medical diagnostic interfaces. However, pursuing higher resolution often compromises mechanical durability, as miniaturized sensing components and intricate microstructural geometries become more vulnerable to mechanical wear, structural deformation, and fatigue failure under repeated loading conditions.
The fundamental conflict between these parameters arises from divergent design requirements. High-resolution implementations necessitate delicate microstructures with reduced feature sizes and complex geometries, while durable designs prioritize robust structures with simplified sensing units. Material innovation and structural optimization strategies play pivotal roles in addressing this challenge, making it possible to enhance spatial resolution without sacrificing the sensor’s mechanical robustness.
The micro-pyramid array exemplifies an effective approach to balancing sensitivity and durability through controlled spatial arrangement[76]. By optimizing the ratio of pyramid base length to their spacing, particularly at a 1:1 ratio, the sensor achieves high sensitivity across both low-pressure (< 10 kPa) and medium-pressure (10-100 kPa) regimes. The periodic pyramidal architecture facilitates mechanical stress distribution, mitigating localized strain concentrations that typically initiate material degradation. The integration of PDMS/CNT conductive elastomers further enhances the sensor’s resistance to stress and wear, thereby maintaining consistent performance under prolonged operational cycles.
To achieve high spatial resolution, Figure 6 presents a strategy employing biomimetic microstructure design[29]. Ridge-shaped artificial fingerprint patterns replicate the tactile sensing capabilities of human fingertips, enabling precise detection of surface textures through interactions with fine surface features. By adjusting the ridge tip (Figure 6A) and the spacing between microstructures, the sensor’s ability to detect fine textures is enhanced, enabling the discrimination of closely spaced fibers in textiles. Furthermore, the sensor’s mechanical durability is improved by using a micro-structured ionic gel layer (Figure 6B), which reduces response relaxation time and enhances overall elasticity. This design ensures high sensitivity while allowing rapid responses to both static and dynamic stimuli, including high-frequency vibrations, without compromising the detection of subtle surface variations. By integrating advanced materials with refined microstructures, this approach achieves both high spatial resolution and mechanical durability, making it suitable for real-time applications in robotic interaction and prosthetic sensory systems.
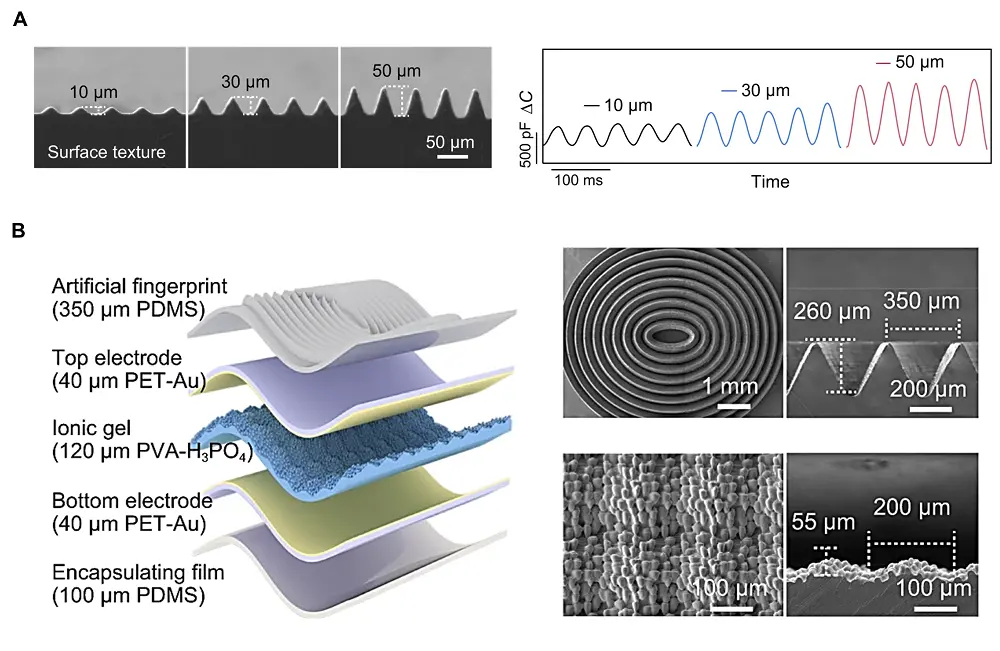
Figure 6. Optimization of space resolution[29]. (A) SEM image of textured structures that have ridges with three different heights (10, 30, and 50 μm) and signals generated by the interaction of the slip-sensor; (B) Schematic diagram of the structure of the slip-sensor. SEM: scanning electron microscopy; PDMS: polydimethylsiloxane; PET: polyethylene terephthalate; PVA: polyvinyl alcohol.
3.3 Contradictions and trade-offs between major performance categories
Achieving optimal triaxial tactile sensor performance requires balancing three critical yet competing requirements: sensing performance, long-term durability, and integration feasibility. Force sensitivity-enhancing strategies, such as ultra-soft materials and microstructural amplification, typically compromise measurement range due to material deformation limits and long-term durability despite their superior detection capabilities. These materials are susceptible to environmental disturbances and microstructural changes that cause material aging and signal instability. For example, spike-nickel particle-based piezoresistive composites undergo conductive network reorganization under sustained loading, resulting in baseline resistance drift and decreased measurement accuracy. Conversely, extending dynamic range through high-strength composite materials often reduces sensitivity at low pressures.
Durability-optimized sensors employ stable conductive networks, such as piezoresistive materials with high aspect ratio fillers or conservative large-contact-area designs that minimize stress concentration. While ensuring operational stability, these approaches inherently reduce sensitivity and force resolution, thereby limiting their suitability for precision applications.
Structural designs that improve force concentration may sacrifice spatial resolution and integration efficiency, as complex 3D microstructures require larger footprints and sophisticated fabrication processes. High-sensitivity composites typically employ mesoscopic or macroscopic features such as surface protrusions, which increase packaging complexity compared to conventional multilayer devices. These features create stress concentration points prone to fatigue failure during extended operation, further compromising durability. Additionally, their sensitivity to wiring errors and assembly stresses during integration undermines the consistency required for large-scale deployment. Anti-interference designs, while enhancing stability in dynamic environments, generally limit maximum measurement capabilities.
These trade-offs underscore the need for application-specific sensor design and co-optimization frameworks that balance competing requirements according to scenario demands, rather than pursuing universal performance optimization.
In summary, achieving an optimal balance between spatial resolution and mechanical durability requires coordinated optimization of material properties, geometric design, and sensor structures. Through micro-pyramid arrays, biomimetic microstructures, and advanced composite materials, modern tactile sensors overcome traditional performance limitations, enabling reliable operation in applications such as robotic precision assembly, wearable health monitoring, and interactive haptic interfaces. By addressing the interdependence of resolution and durability, these innovations expand the functional capabilities of triaxial tactile sensing technologies.
4. Data Acquisition and Processing
This chapter systematically presents the data acquisition processes specific to triaxial tactile sensors alongside advanced machine learning-based data processing methods, emphasizing how the integration of these technologies enhances overall sensor performance.
Data acquisition forms the initial stage of tactile information processing, involving the accurate transduction of tactile stimuli into quantifiable electrical signals. This stage is crucial as it determines the fidelity and richness of information available for subsequent analysis. Typically, data acquisition systems for three-dimensional tactile sensing are designed to capture signals such as normal and shear force vectors, pressure distributions, and high-frequency vibrations, depending on the sensor’s capabilities. These analog signals are converted into digital formats via analog-to-digital converters and signal conditioning circuits, ensuring high accuracy, fidelity, and compatibility with downstream computational models. Effective data acquisition for machine learning applications requires meticulous calibration to minimize signal distortion and environmental interference. The resulting high-fidelity datasets are essential for training robust models. Moreover, the diversity and comprehensiveness of the acquired data significantly influence model performance, particularly in interpreting complex haptic interactions and enabling reliable real-time tactile feedback.
In recent years, machine learning has made significant progress in processing and analyzing triaxial tactile signals, particularly in addressing challenges such as multimodal data fusion and environmental noise suppression. CNN[77] and recurrent neural network (RNN) have become foundational techniques for extracting complex spatial features from tactile data, enabling accurate predictions of material properties and object contact states. Generative Adversarial Network[78] enhance signal fidelity under low signal-to-noise conditions by generating synthetic tactile data, where the generator network produces physically plausible tactile signatures to augment limited experimental datasets. Moreover, reinforcement learning[79] optimizes closed-loop haptic feedback and robotic manipulation strategies through reward signals derived from tactile performance metrics. Contrastive learning and self-supervised learning approaches mitigate reliance on labeled datasets by leveraging unlabeled tactile data to learn invariant features, significantly advancing unsupervised learning applications in tactile perception research[80]. Collectively, these advances have enhanced the accuracy, efficiency, and scalability of tactile sensing systems across robotics, healthcare, and intelligent monitoring domains.
4.1 Machine learning for data processing.
Machine learning has revolutionized tactile sensing technologies. As illustrated in Figure 7A, the IrisTact tactile sensor[81] utilizes a flexible grating structure to capture color variations induced by mechanical deformation, generating datasets for tactile information decoupling and processing via deep neural networks. The flexible grating produces wavelength-dependent structural color changes under mechanical stress, visually encoding tactile data. Contact-induced surface distortions modify light diffraction patterns, resulting in distinct chromatic signatures captured by an integrated real-time camera system. These visual inputs serve as the basis for deep learning models to interpret and analyze tactile signals effectively.
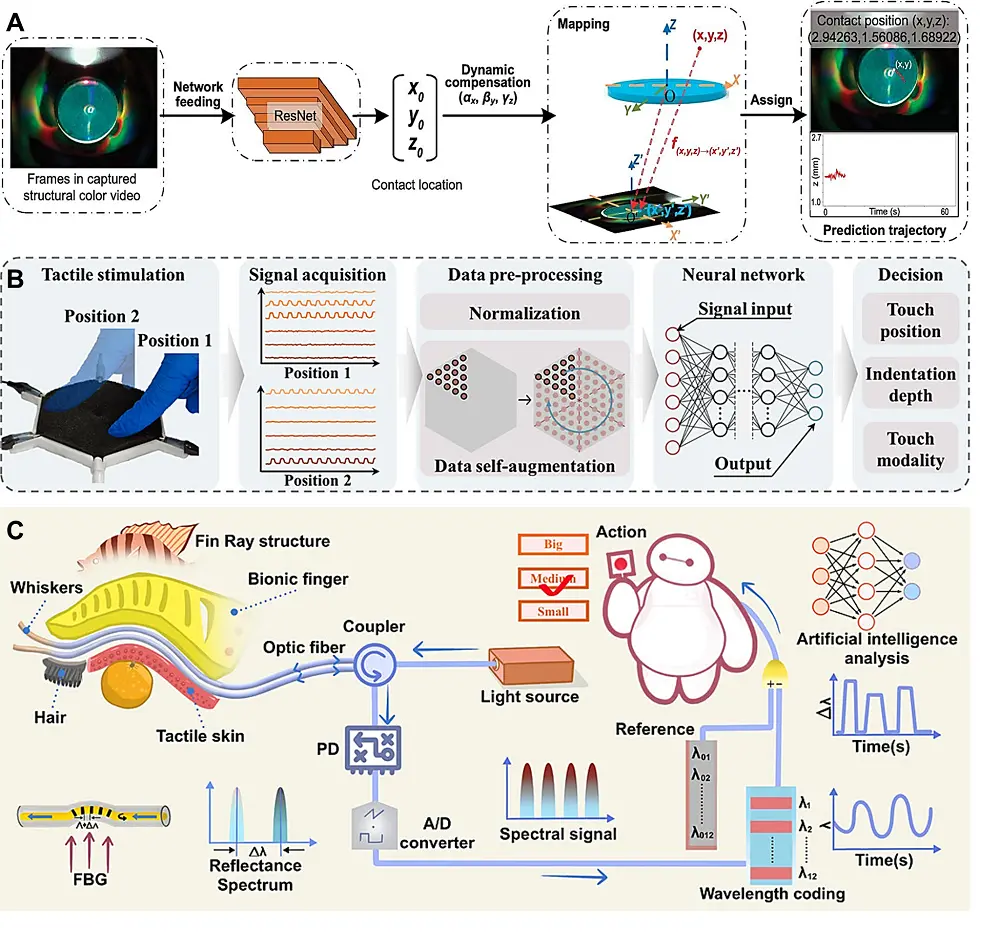
Figure 7. Machine learning for data processing. (A) The prediction of contact location for each frame of the recorded structural color video[81]; (B) Schematic process flow of the algorithm-sensor system based on CB-coated PU sponge[82]; (C) Mechanisms and processes of multimodal tactile perception in biomimetic fingers using optical fiber sensors[77]. PD: photodetector.
To accurately decode tactile information from these optical patterns, the system employs a ResNet deep CNN. Following preprocessing steps that reduce noise and enhance key features, the structural color images are fed into the CNN, which is trained to predict essential tactile parameters such as planar contact coordinates (X, Y), indentation depth (Z), and the magnitude of applied normal force. By adopting this data-driven approach, the system avoids the need for complex physical calibration of mechanical deformation models. Instead, it learns the intrinsic mapping between color variations and physical interaction parameters directly from large datasets. This method effectively leverages neural networks to decode complex tactile information, significantly improving tactile estimation accuracy while achieving high spatial resolution and force sensitivity.
During dynamic contact scenarios, the IrisTact sensor continuously monitors changes in structural color resulting from positional shifts, deformation depths, and varying force magnitudes. To reduce the impact of elastic rebound effects, a dynamic difference preprocessing technique is applied to the captured images before they are input into the ResNet model. Additionally, dynamic compensation strategies are implemented to correct prediction deviations during high-speed motion, ensuring the system maintains high accuracy and stability even under rapid and complex interactions such as robotic assembly and interactive surface exploration.
Figure 7B presents another tactile sensing platform integrating DNN for advanced data processing[82]. This sensor aims to replicate the tactile perception capabilities of human skin, enhancing human-computer interaction. It is based on a carbon black-coated PU sponge, leveraging the material’s flexible piezoresistive properties to achieve continuous, large-area tactile sensing. Mechanical contact induces spatially varying resistance changes, generating six-channel electrical signals proportional to the contact location and intensity. A custom DNN model processes the preprocessed signals through multiple hidden layers, learning nonlinear mappings between electrical responses and tactile parameters. The trained model accurately estimates contact position within a regular hexagonal sensing area while simultaneously predicting indentation depth and applied force magnitude. To overcome limited training data and enhance model robustness, a data self-enhancement approach is employed, generating synthetic datasets based on the sensor’s regular hexagonal structure. This augmentation technique improves the model’s generalization ability and reduces reliance on extensive experimental data. Ultimately, the model achieves accurate localization and force estimation across the continuous sensing area, significantly enhancing the performance of human-computer interaction systems.
CNNs were employed to process multimodal tactile data acquired from a Fiber Bragg Grating sensor[77] (Figure 7C). The dataset was divided into training (60%), validation (20%), and testing (20%) subsets. The CNN architecture consisted of Conv2D layers with 32 convolutional kernels of size 1 × 1 using ReLU activation functions, MaxPooling2D layers with 1 × 1 pooling windows, a Flatten layer for dimensionality reduction, and Dense layers containing 64 neurons with ReLU activation. The output layer utilized Softmax activation to enable multi-class classification. This computational framework demonstrated outstanding performance across various tactile perception tasks, achieving classification accuracies of 99% for surface roughness discrimination, 98.79% for material hardness identification, 97.79% for finger pad position recognition, and 96% for fruit size categorization. These results highlight the exceptional capability of CNNs to process and interpret complex tactile information obtained from fiber optic sensing systems.
The TactileNet architecture, built on a deep CNN, enhances tactile data processing by employing multiple TactileNetBase sub-networks based on the MobileNetV2 backbone[38]. Each sub-network independently processes individual frames, capturing both spatial deformation patterns and temporal dynamics. By sharing extracted parameters across frames, the model significantly reduces the total number of parameters, minimizing the risk of overfitting and ensuring efficient learning for each frame. Feature maps from multiple frames are concatenated and fused through 3D max pooling and global average pooling layers, culminating in a classification vector generated by a fully connected layer. This design enables simultaneous and efficient multi-frame tactile signal processing, substantially improving the model’s efficiency and accuracy via effective parameter sharing.
Tactile data processing based on the VGG network[83], known for its effectiveness in handling colorful images, offers an alternative approach for object classification using tactile input. After acquiring tactile signals from a multi-channel optical fiber sensor, the data are transformed into two-dimensional images via a recursive graph algorithm. These images are then processed by the VGG network, which extracts deep tactile features through hierarchical convolutional layers and performs classification using fully connected layers. This method enables real-time object recognition with high accuracy based on the encoded tactile information.
While machine learning techniques hold great promise for triaxial tactile sensing, their application in real-world robotic and wearable systems faces significant engineering challenges. These models demand extensive, high-quality labeled datasets, but acquiring such data is difficult. Large-scale data collection requires exceptional long-term sensor stability, as training often spans months of continuous acquisition. During this time, sensor drift, calibration shifts, and performance degradation can introduce systematic errors that corrupt datasets and undermine model reliability. Another major challenge is inter-device variability; manufacturing inconsistencies cause differences in sensor response across units, leading models to learn device-specific artifacts instead of genuine tactile patterns. Additionally, maintaining high signal quality is essential, since effective training depends on high signal-to-noise ratios to detect subtle force variations. Overcoming these obstacles calls for improved sensor designs emphasizing manufacturing uniformity, standardized calibration procedures, and automated data acquisition systems. Furthermore, data augmentation and transfer learning strategies can help mitigate the demand for large datasets.
Deploying sophisticated machine learning models on resource-constrained wearable devices poses significant computational challenges. Traditional deep learning methods demand substantial processing power, memory, and energy, which conflict with the size, weight, and power limitations inherent to portable systems. The need for real-time processing further intensifies these demands, as tactile sensing applications often require immediate responses with minimal latency. Such computational overhead can rapidly deplete battery life and generate excessive heat, making sustained operation impractical. To address these challenges, physics-informed network designs are employed, leveraging the mechanical, optical, or electromagnetic force decoupling principles intrinsic to the sensors. This allows pre-configuration of network parameters and more efficient training, effectively reducing computational load. Additionally, simplifying network architectures by decreasing layer depth and node counts enhances efficiency while preserving performance.
Achieving robust model performance across diverse tasks and environments remains a significant challenge. Although expanding training datasets to include a wider range of scenarios can improve generalization, it substantially increases dataset size, labeling costs, and development time. The heterogeneity of tactile sensing tasks, from delicate manipulation to demanding industrial monitoring, often necessitates fundamentally different sensing characteristics. In many practical applications, developing task-specific models optimized for well-defined environments proves more efficient and effective than striving for universal solutions.
The black-box nature of many machine learning models poses challenges for understanding and trusting tactile perception decisions, especially in safety-critical applications. Complex neural networks often operate through opaque processes that offer little insight into how force information is processed. Enhancing interpretability requires integrating physics-based principles into both sensor design and algorithmic approaches. Designing force decoupling methods grounded in fundamental mechanical, optical, and electromagnetic principles enables physically interpretable information processing. Incorporating physical model constraints through techniques such as Physics-Informed Neural Networks can improve model interpretability while maintaining performance. These implementation challenges highlight the importance of co-designing hardware and software components with careful consideration of the specific constraints and requirements of target applications.
4.2 Complex haptic information processing and recognition based on machine learning
4.2.1 Surface Texture Recognition.
Tactile sensors enable texture discrimination by detecting surface microstructural characteristics such as hardness, roughness, and frictional properties. Machine learning algorithms like CNN and RNN facilitate automated feature extraction and classification of textural patterns, allowing robotic systems to achieve precise surface texture identification. Sliding-based recognition methods further enhance measurement accuracy by analyzing dynamic variations in normal and frictional forces during surface traversal. This integrated approach significantly advances robotic capabilities in object recognition and dexterous manipulation.
Figure 8A illustrates a deep learning-based tactile perception method that integrates an arc-shaped tactile sensor with a LSTM network for surface texture analysis[69]. The sensor quantifies three-dimensional magnetic flux components to capture material properties such as softness, friction coefficient, and surface roughness across diverse fabric types. The LSTM model incorporates attention-enhanced mechanisms to automatically process temporal tactile signals, eliminating the need for manual feature extraction. This methodology achieves 99% classification accuracy across 60 fabric categories, demonstrating promising applications in Braille interpretation and textile quality inspection through surface characteristic-based tactile analysis.
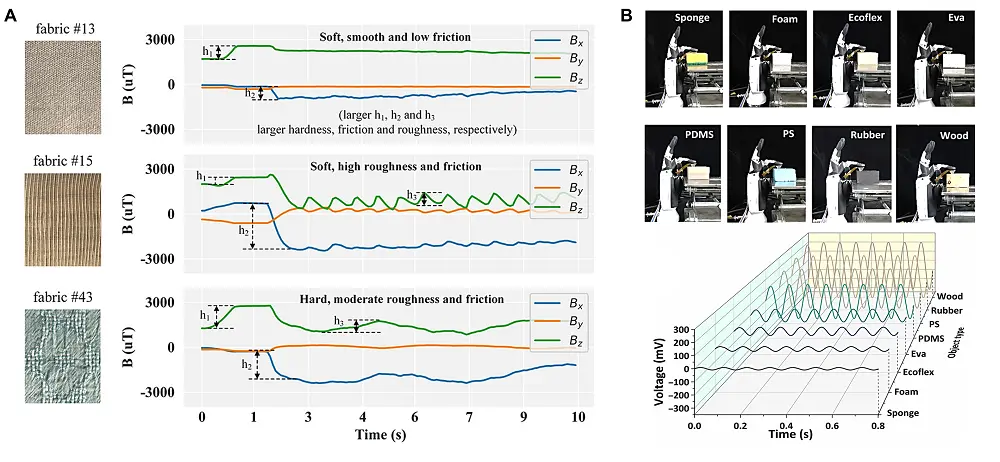
Figure 8. Texture recognition and stiffness recognition. (A) Sensor responses when sliding over three fabric samples with different hardness, friction, and roughness[69]; (B)The real-time piezoelectric output and the corresponding voltage peak obtained by the sensor when in contact with eight objects of different softness[77].
The texture recognition performance of the CNN-integrated TIRgel sensor system[84] is demonstrated through experiments where RGB (Red, Green, Blue) images of fabric textures are captured, printed, and then brought into contact with the TIRgel sensor for tactile measurements. The acquired tactile images reveal distinct luminosity patterns: smooth surfaces, such as printed photographs, show localized bright contact points, whereas fabric textures display characteristic layered geometric patterns. These results confirm the sensor’s ability to capture subtle tactile details, validating the TIRgel system’s effectiveness for fine texture detection based on CNN processing.
4.2.2 Slip Detection
Tactile sensors enable slip monitoring by analyzing real-time three-dimensional tactile images and the evolving pressure matrix derived from the captured triaxial distribution of contact forces. Machine learning algorithms extract discriminative features from raw tactile data to identify slip initiation events. The integration of temporal convolutional networks (TCNs) improves slip detection by capturing temporal patterns, providing critical feedback for robotic slip compensation during practical operations. For example, a pneumatic tactile sensor system employing TCN for slip detection[85] monitors dynamic pressure variations during object interaction. The TCN model learns to distinguish static contact from slipping states through temporal feature extraction. Trained on labeled pressure data, the system achieves accurate, efficient, and robust slip classification across varying slip velocities, directions, and surface curvatures, demonstrating high accuracy and operational reliability for robotic slip compensation.
4.2.3 Stiffness identification
Tactile sensors characterize stiffness by mapping three-dimensional contact forces and generating tactile images, such as pressure matrices. Machine learning algorithms process the collected raw moment data to classify objects according to their elastic properties. The integration of triaxial tactile sensing with machine learning techniques enables efficient and accurate stiffness recognition, providing a crucial capability for robotic manipulation in unstructured environments.
Figure 8B illustrates a biomimetic dual-modal tactile sensor[77] that quantifies material stiffness by synergistically integrating piezoelectric and piezoresistive modules, analogous to the fast-adaptive and slow-adaptive mechanoreceptors in human skin. The system employs a hierarchical recognition strategy: the piezoelectric layer initially classifies object stiffness through active vibration, with amplitude modulations in the piezoelectric signal corresponding to distinct stiffness categories. After this preliminary classification, the robotic manipulator applies a calibrated contact force, generating characteristic feedback from the piezoresistive layer. A CNN processes these multidimensional tactile signals to quantitatively determine elastic coefficients across variable contact angles. This methodology overcomes limitations of conventional measurement techniques, effectively eliminating the risk of sample damage inherent to static methods, while enhancing measurement accuracy compared to dynamic approaches. In practical applications, this machine learning-augmented recognition system achieved 98.44% accuracy in clinical feature identification. Furthermore, it enables precise stiffness characterization in intelligent harvesting, facilitating optimal grip force modulation to prevent both material damage and object slippage during manipulation.
A field-programmable gate array-based tactile sensing system[86] utilizes tactile torque as a descriptor for stiffness recognition. The sensor detects changes in triaxial magnetic flux density during object contact, capturing parameters related to stiffness, elastic deformation, and surface friction characteristics. Two classification algorithms, unsupervised K-means and supervised K-nearest neighbor, process the tactile torque data to categorize material stiffness. The system achieves 86.7% classification accuracy, demonstrating its practical utility for real-time stiffness identification applications.
4.2.4 Touch status recognition
Figure 9 presents experimental results for touch pattern recognition[82]. Figure 9A identifies five distinct contact modes with corresponding six-channel sensor responses, while Figure 9B visualizes the dimensionality-reduced feature space. Deep learning models trained on this dataset show significant performance improvement through data augmentation strategies. As shown in Figure 9C, augmented training increases classification accuracy from 76.26% to 94.62%, and confusion matrix analysis confirms enhanced pattern discriminability due to expanded training data diversity.
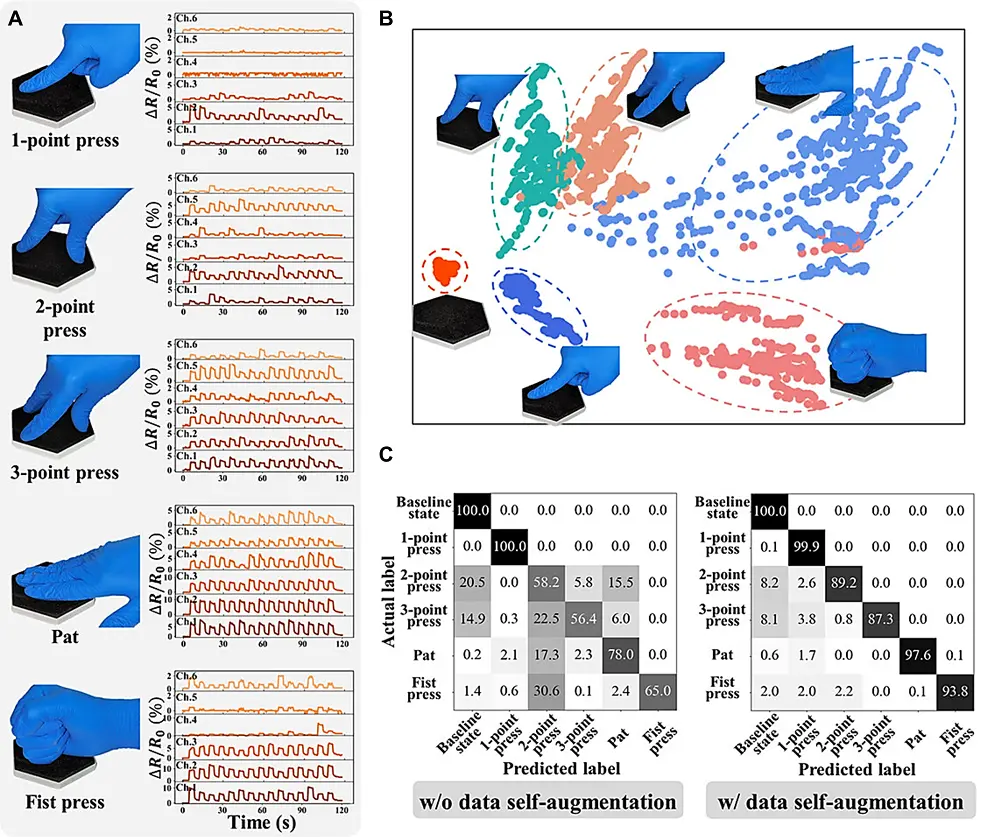
Figure 9. Touch modality recognition task[82]. (A) Five different touch states and the responses of the corresponding six channels; (B) Visualization of the collected training data of five touch modalities after dimensionality reduction; (C) Confusion matrix results on the testing set when not adopting and adopting data self-augmentation strategy.
4.2.5 Dialect recognition
Figure 10 illustrates a wearable dialect speech recognition system based on Ti3C2Tx composite aerogel pressure sensors[25]. This sensor detects subtle laryngeal muscle vibrations (Figure 10A) and offers improved resistance to external noise interference compared to conventional speech recognition technologies.
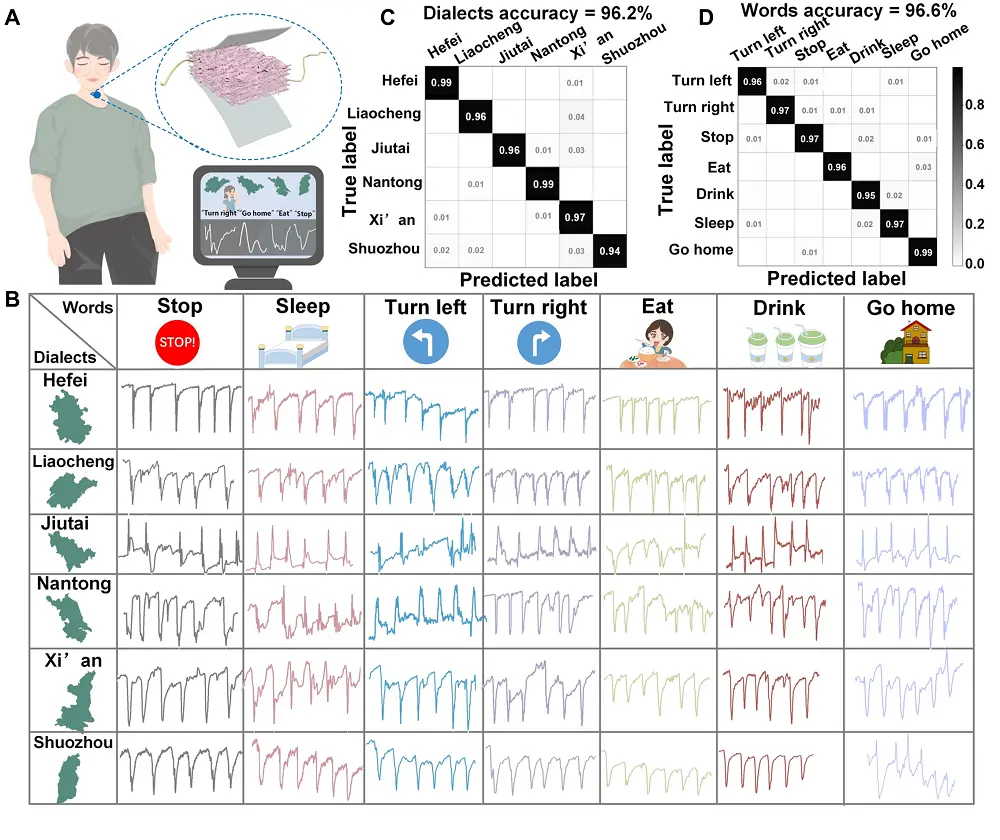
Figure 10. Dialect speech recognition[25]. (A) A speech recognition sensor installed in the throat; (B) Continuous current signal images generated by common words in different Chinese dialects; (C) Confusion matrix of the CNN for six different Chinese dialects; (D) Confusion matrix of the CNN for seven words in different Chinese dialects. CNN: convolutional neural network.
For dialect analysis, the study employs CNN to process pressure signals acquired by the sensor to distinguish regional dialects and words. Figure 10B displays continuous current waveforms for seven common words across six Chinese dialects, revealing distinct vibrational signatures during articulation. The CNN architecture effectively captures subtle pronunciation variations and processes continuous changes in current signals. Trained on 6,888 dialect samples and 4,158 word samples, the model achieves 96.2% dialect recognition accuracy and 96.6% word recognition accuracy (Figure 10C and Figure 10D), confirming its linguistic analysis capabilities.
These cases collectively demonstrate machine learning’s transformative role in bridging complex raw data and intuitive tactile information. Through systematic integration of sensor hardware and computational models, modern tactile systems achieve unprecedented capabilities in robotic manipulation and wearable systems.
5. Practical Application
This chapter explores the diverse and rapidly evolving applications of triaxial tactile sensing technology, highlighting its multifunctionality and transformative potential across various fields. We systematically examine the integration of triaxial tactile sensors in areas such as human-computer interaction, e-skin[86], tactile signal encryption, and pressure feedback systems. Special attention is given to recent technological advancements and their broad implications. In particular, we investigate how these sensors have significantly improved the intuitiveness, precision, and responsiveness of human-machine interactions. By thoroughly analyzing these applications, we emphasize the pivotal role of triaxial tactile sensing technology in shaping the future of robotics, healthcare, wearable devices, and immersive human-computer interfaces.
5.1 Robotics application
5.1.1 Haptic integration in robot and human-computer interaction
In robotic manipulation tasks, triaxial tactile sensors (Figure 11A) play a critical role in enhancing robotic dexterity and adaptability[87]. High-resolution tactile sensing technologies enable real-time detection of contact posture and distributed force vectors. This detailed feedback is essential for executing complex multi-axis object rotations, especially when handling unstable grasps or irregularly shaped objects[88]. By continuously monitoring rich haptic information, robotic systems can detect potential grasp instabilities and dynamically adjust manipulation strategies, significantly improving task success rates and operational robustness. Furthermore, the system not only provides contact position and force data but also integrates sim-to-real haptic transfer technology, enabling the simulation and fine-tuning of object rotation operations without requiring direct physical contact. This capability is vital for precise and adaptive robotic operations in highly dynamic and unpredictable environments.
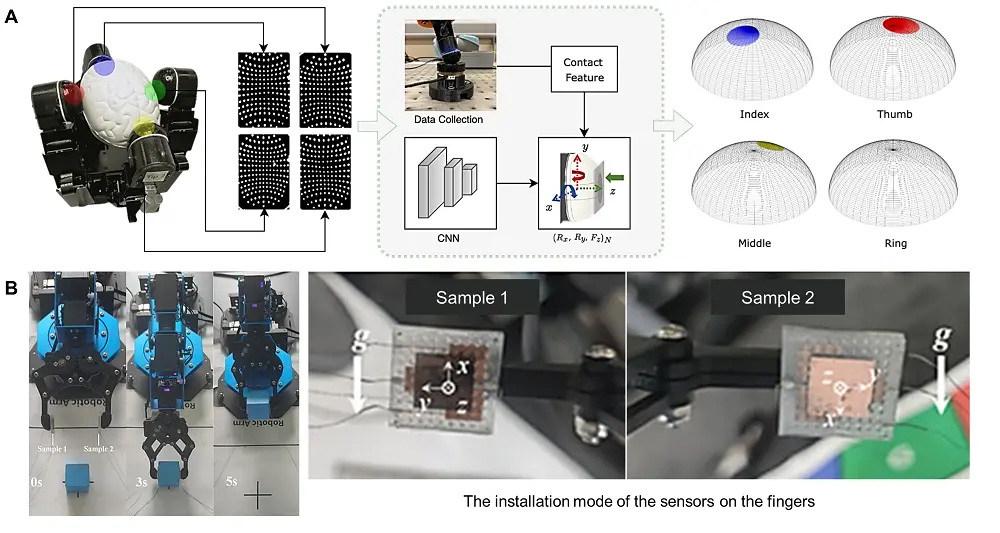
Figure 11. Haptic integration in robot and human-computer interaction. (A) Application of triaxial tactile sensors in precise robotic manipulation and object rotation; (B) Haptic integration in robot arms[31]. CNN: convolutional neural network.
The capacitive triaxial tactile sensor based on elastic microcones, shown in Figure 11B, is designed to provide precise tactile feedback for robotic grasping and object handling tasks[31]. By effectively discriminating shear forces, it enhances fine grasping capabilities, especially for fragile objects. The sensor offers real-time feedback on grip force and gravitational loading, ensuring safe and efficient manipulation of delicate items. When integrated into robotic arms, it captures subtle force variations, enabling continuous adjustment of grasp strategies to improve stability and accuracy. This technology is particularly valuable in applications requiring fine motion control, such as robotic surgery, human-robot collaboration, and exploration in hazardous or complex environments where precision and reliability are critical.
A wireless haptic interface has been developed to deliver programmable feedback over a large skin surface area, enabling fine-grained control of touch sensations[32]. This innovative interface is lightweight, flexible, and fully wireless, integrating scalable control electronics with efficient wireless power transmission. The system provides real-time tactile feedback and has been demonstrated in diverse applications such as navigation instruction delivery, music translation into tactile patterns, and sensory substitution for robotic prosthetic limb control. Operated through a customizable user interface, it manages multiple actuators and delivers high-precision, location-specific haptic feedback across different body regions. By modulating vibration intensity and frequency, the interface conveys spatial, auditory, and kinesthetic information, enabling natural, intuitive, and immersive interactions with the skin.
5.2 Wearable devices
5.2.1 Wearable tactile skin
Wearable e-skin technologies are increasingly used as wireless human-machine interfaces in robotics and VR systems. As shown in Figure 12A, skin-integrated patches embedded with bending sensors and haptic actuators enable users to remotely control robotic arms with high precision and responsiveness[23] These patches are placed on various body locations to capture user movements via highly sensitive bending sensors and provide tactile feedback through actuators, forming a closed-loop system that significantly enhances real-time user-robot interaction. Wireless communication ensures minimal latency, making the system highly effective for applications such as robotic surgery, patient care, and complex teleoperation tasks. The simultaneous integration of visual and tactile feedback within the VR environment allows users to observe robotic actions while experiencing corresponding tactile responses, creating an immersive and intuitive control experience that closely mimics direct physical interaction.
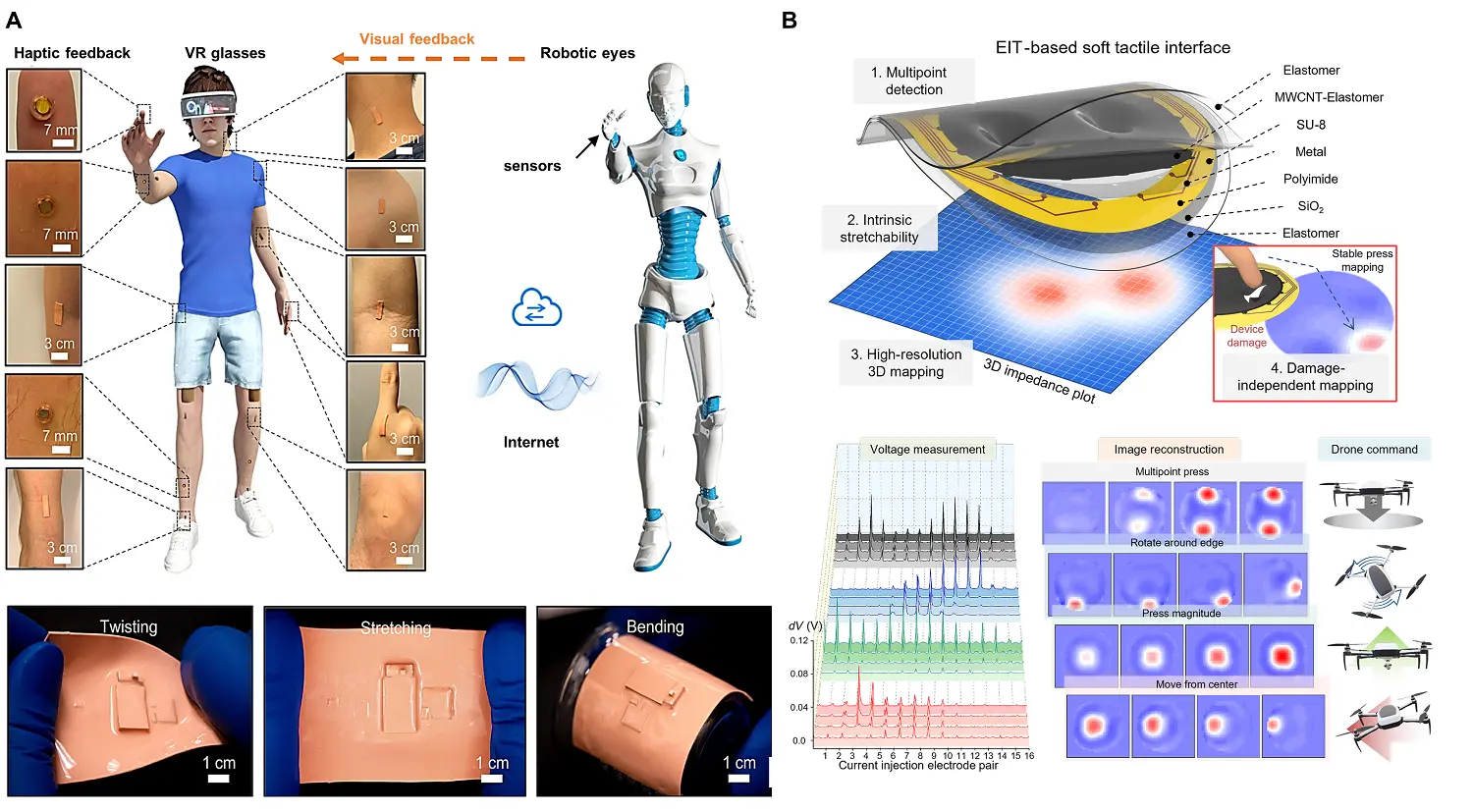
Figure 12. Wearable e-skin. (A) e-skin in robotic VR applications[23]; (B) Real-time drone control via the e-skin[26]. VR: virtual reality; EIT: electrical impedance tomography; SU: SU-8 2, a negative photoresist used for passivation, was obtained from Microchemicals. MWCNT: multiwall carbon nanotube.
As depicted in Figure 12B, an ultrathin, soft electronic skin based on electrical impedance tomography (EIT) incorporates an organic/inorganic hybrid structure[26]. The device is fabricated through a simple, cost-effective manufacturing process that features micropatterned multi-walled carbon nanotubes embedded in elastomer composites, achieving both skin-like mechanical compliance and exceptional operational stability. Unlike conventional array architectures that require numerous interconnects, this EIT-based tactile interface delivers superior spatiotemporal resolution with significantly fewer connection points. The pixel-to-interconnect ratio exceeds 57. The system demonstrates remarkable sensing precision, distinguishing external pressures at sub-millimeter resolution and detecting vertical deformations as small as several hundred micrometers. Moreover, the interface maintains functional integrity under external damage and environmental perturbations, confirming its suitability for sustained wearable applications. Its practical utility is demonstrated in real-time human-machine interfaces, specifically in handwriting recognition and drone control, highlighting considerable potential for advanced human-computer interaction systems.
An alternative e-skin design utilizes interlocked piezoresistive microsphere arrays to achieve enhanced sensitivity[19]. The interlocking geometry concentrates mechanical stress at the microsphere contact points, producing distinct deformation patterns depending on the type and direction of the applied force. This structure enables differentiation between normal and shear forces and facilitates detailed mapping of tactile events. The system accurately detects subtle variations in tactile stimuli, such as finger pressure or fluid flow, and generates high-resolution tactile maps. These capabilities make it highly suitable for diverse applications, including intelligent prosthetics, robotics, and wearable health monitoring systems where precise tactile feedback is essential for effective environmental interaction.
The triaxial artificial e-skin (3DAE-Skin)[23] successfully replicates human mechanical sensation by emulating the spatial distribution of mechanoreceptors such as Merkel cells and Ruffini endings. Designed with a bioinspired approach, the 3DAE-Skin features multilayered force and strain sensing arrays arranged to mimic the distribution of these mechanoreceptors in human skin. This design also ensures exceptional flexibility and mechanical durability. By integrating force and strain sensing components, the 3DAE-Skin can detect object modulus and surface curvature in real time during contact events. Leveraging deep learning algorithms, the system achieves highly accurate detection of object stiffness and shape with fine spatial resolution, thereby broadening its potential applications.
5.2.2 Tactile feedback
The development of advanced tactile feedback systems is crucial for fully realizing the potential of three-dimensional haptic sensing. As depicted in Figure 13A, the system[24] delivers vibrational feedback that simulates realistic tactile sensations, allowing users to experience the feeling of grasping and manipulating virtual objects (Figure 13B). This capability has transformative implications for virtual social interaction, education, and gaming, significantly enhancing both realism and engagement. For example, users can perform complex tasks such as playing a virtual piano (Figure 13C), receiving synchronized vibration feedback corresponding to each keystroke, thereby deepening immersion and improving motion control.
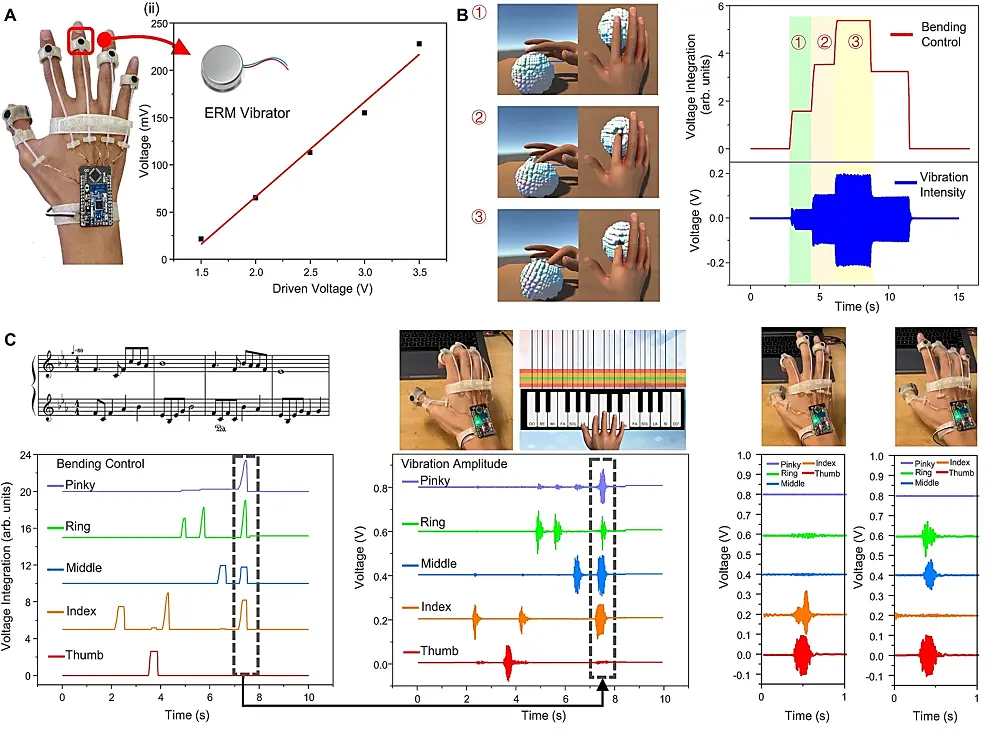
Figure 13. Augmented multimodal haptic feedback system[32]. (A) Illustration of the ATH-Ring based HMI; (B) The relationship between the vibration intensity collected by a PZT vibration sensor and the driven voltage of the vibrator; (C) Playing a virtual piano with multiple fingers, with corresponding control and real-time vibration signals. HMI: human-machine interface; ATH: augmented tactile-perception and haptic-feedback; PZT: Lead Zirconate Titanate; ERM: eccentric rotating mass.
An additional type of haptic feedback system[89] integrates force sensing with electro-haptic actuation through optimized electrode surface designs (Figure 14). By modifying surface microstructures, the contact resistance between the electrode and the skin dynamically changes in response to applied forces. This mechanism enables real-time modulation of tactile sensations without relying on complex mechanical actuators, providing a lightweight, efficient, and highly realistic haptic interface for next-generation wearable VR and AR applications.
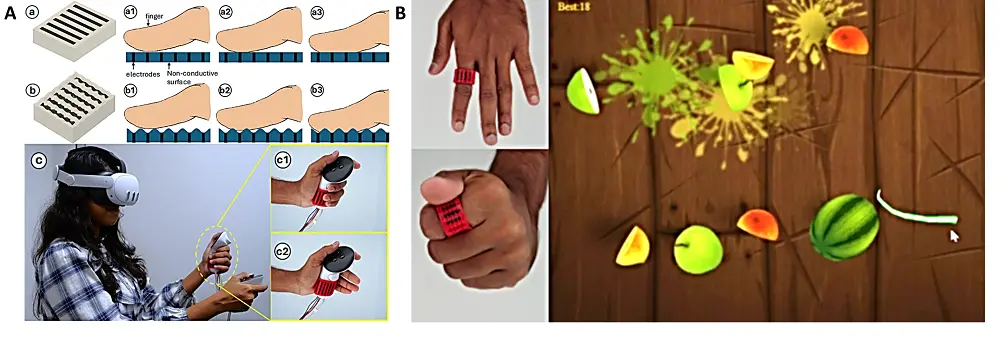
Figure 14. A tactile interface integrating force sensing and electrical tactile stimulation[89]. (A) Manipulating the geometry of the tactile surface to enable the high variance of the contact between the skin and the electrodes with pressure; (B) Demonstration of tactile sensors in games.
5.3 Information security
5.3.1 Tactile signal encryption
In the emerging field of tactile signal encryption, bilayer gradient hydrogel systems demonstrate exceptional potential by combining high-sensitivity pressure sensing with dynamic information encryption capabilities. This flexible e-skin system[90] differentiates between light (causing minimal capacitance change) and heavy (causing significant capacitance variation) pressure inputs, encoding binary states “0” and “1” based on these capacitance changes. By varying the sequence of light and heavy touch events along the same trajectory, a range of encrypted binary outputs and information encoding strategies can be realized. This mechanism enables real-time dynamic trajectory recognition as well as static text input and conversion of encrypted messages, offering a promising approach toward integrating triaxial tactile sensing with secure information processing in flexible electronics platforms.
By integrating positional and pressure-based information, these systems significantly enhance password complexity and security, as tactile pressure characteristics are difficult to detect visually. Unlike traditional password systems that rely solely on positional input, location-and-pressure intelligent-based systems[91] require precise matching of both spatial coordinates and pressure profiles, making unauthorized replication exceedingly difficult. This approach effectively safeguards sensitive information and provides a more secure password protection mechanism.
In summary, the advancement of intelligent triaxial tactile sensors will focus on five critical research directions that collectively drive rapid expansion in practical applications. First, low-power design will support long-term tactile monitoring in battery-powered wearable devices and bionic robotic systems. Second, multi-modal integration will synergistically process diverse tactile parameters, including normal pressure, shear forces, temperature, and vibration, to achieve comprehensive perception of complex contact states. Third, enhanced environmental robustness will ensure stable tactile detection performance under harsh conditions such as mechanical shock, temperature and humidity fluctuations, and electromagnetic interference. Fourth, machine learning-integrated chips will embed signal processing and feature extraction capabilities directly within sensor architectures, enabling real-time edge intelligence for tactile data analysis. Finally, multi-modal recognition technology will achieve deep fusion of tactile information with visual and auditory signals, enabling accurate identification of object material properties, geometry, surface texture, and dynamic characteristics. Together, these technological innovations will provide high-precision tactile sensing solutions for precision manufacturing, medical diagnostics, and intelligent human-machine interaction applications, establishing a strong foundation for the next generation of intelligent robotics and wearable systems.
6. Conclusion
The field of triaxial tactile sensing technology is advancing at a remarkable pace, achieving significant progress in higher resolution, low power consumption, self-energy generation, and multi-modal integration. These innovations are set to play a pivotal role in shaping the future of next-generation robotics, wearable systems, and human-computer interaction. However, bridging the gap between cutting-edge laboratory innovations and the stringent requirements of practical industrial applications remains a central and ongoing challenge.
Looking ahead, several key technological advancements will shape the future development of triaxial tactile sensors. First, achieving improved resolution and precision will be crucial for replicating or even surpassing human-like tactile perception, thereby enabling finer and more accurate force detection across multiple axes. Second, reducing power consumption and integrating self-energy harvesting capabilities will be vital to ensure sensor autonomy and prolonged operational lifespan, especially in wearable and mobile robotic applications constrained by battery life and energy efficiency. Third, the incorporation of multi-modal sensing, capturing not only force but also parameters such as temperature, humidity, and vibration, combined with the integration of advanced artificial intelligence algorithms, will facilitate real-time data processing, dynamic adaptation, and sophisticated tactile perception.
Despite these promising advancements, significant challenges remain. Balancing the competing demands of high sensitivity, mechanical stability, and scalable manufacturability is essential to enable the transition of triaxial tactile sensors from research prototypes to commercially viable products. Additionally, ensuring reliable performance under extreme environmental conditions, such as elevated temperatures and high humidity, is critical for expanding their application across diverse and harsh scenarios. As robotic systems become increasingly autonomous and interact more seamlessly with complex environments, the growing demand for efficient and intelligent tactile sensing and feedback mechanisms will shape future research priorities.
In summary, the integration of advanced triaxial tactile sensing technologies is expected to drive transformative innovations in robotics, human-computer interaction, and wearable devices. By addressing remaining technical challenges, particularly in materials engineering, sensor architecture design, and intelligent signal processing, triaxial tactile sensors can fully realize their potential to enable more responsive, adaptive, and autonomous systems. Continued interdisciplinary research efforts will be essential to further enhance the integration and scalability of triaxial tactile sensing systems, ultimately advancing the frontier of intelligent systems across multiple domains.
Authors contribution
Yun G: Conceptualization, data curation, investigation, methodology, project administration, resources, supervision, validation, visualization, writing-review & editing.
Hu Z: Data curation, investigation, methodology, resources, validation, visualization, writing-original draft, writing-review & editing.
All authors have given approval to the final version of the manuscript.
Conflicts of interest
The authors have no conflicts of interest to declare.
Ethical approval
Not applicable
Consent to participate
Not applicable
Consent for publication
Not applicable
Availability of data and materials
Not applicable.
Funding
None.
Copyright
© The Author(s) 2025.
References
-
1. Vouloutsi V, Cominelli L, Dogar M, Lepora N, Zito C, Martinez-Hernandez U. Towards Living Machines: current and future trends of tactile sensing, grasping, and social robotics. Bioinspir Biomim. 2023;18:025002.
[DOI] -
2. Mousavi A, Rahimnejad M, Azimzadeh M, Akbari M, Savoji H. Recent advances in smart wearable sensors as electronic skin. J Mater Chem B. 2023;11:10332-10354.
[DOI] -
3. Han ST, Peng H, Sun Q, Venkatesh S, Chung KS, Lau SC, et al. An overview of the development of flexible sensors. Adv Mater. 2017;29:1700375.
[DOI] -
4. Templeman JO, Sheil BB, Sun T. Multi-axis force sensors: A state-of-the-art review. Sens Actuators A Phys. 2020;304:111772.
[DOI] -
5. Leemans J, Respekta D, Bai J, Braeuer S, Vanhaecke F, Hens Z. Formation of colloidal In (As, P) quantum dots active in the short-wave infrared, promoting growth through temperature ramps. ACS Nano. 2023;17:20002-20012.
[DOI] -
6. Ilami M, Bagheri H, Ahmed R, Skowronek EO, Marvi H. Materials, actuators, and sensors for soft bioinspired robots. Adv Mater. 2021;33:2003139.
[DOI] -
7. Ray TR, Choi J, Bandodkar AJ, Krishnan S, Gutruf P, Tian L. Bio-integrated wearable systems: a comprehensive review. Chem Rev. 2019;119:5461-5533.
[DOI] -
8. Wu Y, Ma Y, Zheng H, Ramakrishna S. Piezoelectric materials for flexible and wearable electronics: A review. Mater Des. 2021;211:110164.
[DOI] -
9. Pyo S, Lee J, Bae K, Sim S, Kim J. Recent progress in flexible tactile sensors for human-interactive systems: from sensors to advanced applications. Adv Mater. 2021;33(47):2005902.
[DOI] -
10. Xu J, Pan J, Cui T, Zhang S, Yang Y, Ren TL. Recent progress of tactile and force sensors for human-machine interaction. Sensors. 2023;23(4):1868.
[DOI] -
11. Yin R, Wang D, Zhao S, Lou Z, Shen G. Wearable sensors-enabled human-machine interaction systems: From design to application. Adv Funct Mater. 2021;31(11):2008936.
[DOI] -
12. Liu Y, He K, Chen G, Leow WR, Chen X. Nature-inspired structural materials for flexible electronic devices. Chem Rev. 2017;117(20):12893-12941.
[DOI] -
13. Xu C, Solomon SA, Gao W. Artificial intelligence-powered electronic skin. Nat Mach Intell. 2023;5:1344-1355.
[DOI] -
14. Phadkule SS, Sarma S. Progress in nanocomposite based flexible temperature sensors: A review. Meas Sensors. 2023;27:100692.
[DOI] -
15. Tian S, Wang Y, Deng H, Wang Y, Zhang X. Flexible pressure and temperature sensors towards e-skin: Material, mechanism, structure and fabrication. Soft Sci. 2023;3:30.
[DOI] -
16. Wang Z, Hu J, Han L, Wang Z, Wang H, Zhao Q, et al. A MOF-based single-ion Zn2+ solid electrolyte leading to dendrite-free rechargeable Zn batteries. Nano Energy. 2019;56:92-99.
[DOI] -
17. Wang K, Yap LW, Gong S, Wang R, Wang SJ, Cheng W. Nanowire-based soft wearable human-machine interfaces for future virtual and augmented reality applications. Adv Funct Mater. 2021;31(39):2008347.
[DOI] -
18. Zhang C, Li Z, Li H, Yang Q, Wang H, Shan C, et al. Femtosecond laser-induced supermetalphobicity for design and fabrication of flexible tactile electronic skin sensor. ACS Appl Mater Interfaces. 2022;14(33):38328-38338.
[DOI] -
19. Park J, Lee Y, Hong J, Lee Y, Ha M, Jung Y, et al. Tactile-direction-sensitive and stretchable electronic skins based on human-skin-inspired interlocked microstructures. ACS Nano. 2014;8(12):12020-12029.
[DOI] -
20. Liu Z, Wang G, Ye C, Sun H, Pei W, Wei C, et al. An ultrasensitive contact lens sensor based on self-assembly graphene for continuous intraocular pressure monitoring. Adv Funct Mater. 2021;31(29):2010991.
[DOI] -
21. Wang X, Gu Y, Xiong Z, Cui Z, Zhang T. Silk-molded flexible, ultrasensitive, and highly stable electronic skin for monitoring human physiological signals. Adv Mater. 2013;26(9):1336-1342.
[DOI] -
22. Kim MS, Almuslem AS, Babatain W, Bahabry RR, Das UK, El-Atab N, et al. Beyond flexible: Unveiling the next era of flexible electronic systems. Adv Mater. 2024;36(51):2406424.
[DOI] -
23. Duan S, Yang H, Hong J, Li Y, Lin Y, Zhu D, et al. A skin-beyond tactile sensor as interfaces between the prosthetics and biological systems. Nano Energy. 2022;102:107665.
[DOI] -
24. Bai N, Xue Y, Chen S, Shi L, Zhang Y, Hou X, et al. A robotic sensory system with high spatiotemporal resolution for texture recognition. Nat Commun. 2023;14:7121.
[DOI] -
25. Chen R, Luo T, Wang J, Wang R, Zhang C, Xie Y, et al. Nonlinearity synergy: An elegant strategy for realizing high-sensitivity and wide-linear-range pressure sensing. Nat Commun. 2023;14:6641.
[DOI] -
26. Gu Y, Zhang T, Li J, Zheng C, Yang M, Li S. A new force-decoupling triaxial tactile sensor based on elastic microcones for accurately grasping feedback. Adv Intell Syst. 2023;5(3):2200321.
[DOI] -
27. Jung YH, Yoo JY, Vázquez-Guardado A, Kim JH, Luan H, Park M, et al. A wireless haptic interface for programmable patterns of touch across large areas of the skin. Nat Electron. 2022;5:374-385.
[DOI] -
28. Libanori A, Chen G, Zhao X, Zhou Y, Chen J. Smart textiles for personalized healthcare. Nat Electron. 2022;5:142-156.
[DOI] -
29. Passlack U, Simon N, Buche V, Harendt C, Stieglitz T, Burghartz JN. Investigation of long-term stability of hybrid systems-in-foil (HySiF) for biomedical applications. In: 2020 IEEE 8th Electronics System-Integration Technology Conference (ESTC); 2020 Sep 15-18; Tønsberg, Norway. Piscataway: IEEE; 2020. p. 1-6.
[DOI] -
30. Liu Z, Hu X, Bo R, Yang Y, Cheng X, Pang W, et al. A three-dimensionally architected electronic skin mimicking human mechanosensation. Science. 2024;384(6699):987-994.
[DOI] -
31. Liu Y, Yiu C, Song Z, Huang Y, Yao K, Wong T, et al. Electronic skin as wireless human-machine interfaces for robotic VR. Sci Adv. 2022;8(2):eabl6700.
[DOI] -
32. Sun Z, Zhu M, Shan X, Lee C. Augmented tactile-perception and haptic-feedback rings as human-machine interfaces aiming for immersive interactions. Nat Commun. 2022;13:5224.
[DOI] -
33. Xiao Y, Li H, Gu T, Jia X, Sun S, Liu Y, et al. Ti3C2Tx composite aerogels enable pressure sensors for dialect speech recognition assisted by deep learning. Nano-Micro Lett. 2024;17:101.
[DOI] -
34. Kim K, Hong JH, Bae K, Lee K, Jee DJ, Park J, et al. Extremely durable electrical impedance tomography-based soft and ultrathin wearable e-skin for three-dimensional tactile interfaces. Sci Adv. 2024;10(38):eadr1099.
[DOI] -
35. You J, Lu M, Dazhen L, Gao M, Zhang R, Li W, et al. Anti-motion artifacts iontronic sensor for lon-term accurate fingertip pulse monitoring. Adv Sci. 2025;12(15):2414425.
[DOI] -
36. Park J, Kim M, Lee H, Ko H. Fingertip skin-inspired microstructured ferroelectric skins discriminate static/dynamic pressure and temperature stimuli. Sci Adv. 2015;1(9):e1500661.
[DOI] -
37. Liu W, Yu P, Gu C, Cheng X, Fu X. Fingertip piezoelectric tactile sensor array for roughness encoding under varying scanning velocity. IEEE Sens J. 2017;17(21):6867-6879.
[DOI] -
38. Babadian RP, Faez K, Amiri M, Falotico E. Fusion of tactile and visual information in deep learning models for object recognition. Inf Fusion. 2023;92:313-325.
[DOI] -
39. Chun S, Kin JS, Yoo Y, Choi Y, Jung SJ, Jang D, et al. An artificial neural tactile sensing system. Nat Electron. 2021;4:429-438.
[DOI] -
40. Cheng X, Gong Y, Liu Y, Wu Z, Hu X. Flexible tactile sensors for dynamic triaxial force measurement based on piezoelectric elastomer. Smart Mater Struct. 2020;29(7):075007.
[DOI] -
41. Fu X, Dong J, Li L, Zhang L, Zhang J, Yu L, et al. Fingerprint-inspired dual-mode pressure sensor for robotic static and dynamic perception. Nano Energy. 2022;103(Part A):107788.
[DOI] -
42. Lee S, Byun SH, Kim CY, Cho S, Park S, Sim JY, et al. Beyond human touch perception: an adaptive robotic skin based on gallium microgranules for pressure sensory augmentation. Adv Mater. 2022;34(44):2204805.
[DOI] -
43. Cheng A, Li X, Li D, Chen Z, Cui T, Tao LQ, et al. An intelligent hybrid-fabric wristband system enabled by thermal encapsulation for ergonomic human-machine interaction. Nat Commun. 2025;16:591.
[DOI] -
44. Boutry CM, Negre M, Jorda M, Vardoulis A, Khatib O, Bao Z. A hierarchically patterned, bioinspired e-skin able to detect the direction of applied pressure for robotics. Sci Robotics. 2018;3(24):eaau6914.
[DOI] -
45. Ha M, Lim S, Park J, Um DS, Lee Y, Ko H. Bioinspired interlocked and hierarchical design of ZnO nanowire arrays for static and dynamic pressure-sensitive electronic skins. Adv Funct Mater. 2015;25(19):2841-2849.
[DOI] -
46. Pan L, Chortos A, Yu G, Wang Y, Isaacson S, Allen R, et al. An ultra-sensitive resistive pressure sensor based on hollow-sphere microstructure induced elasticity in conducting polymer film. Nat Commun. 2014;5:3002.
[DOI] -
47. Zhong W, Liu Q, Wu Y, Wang Y, Qing X, Li M, et al. A nanofiber based artificial electronic skin with high pressure sensitivity and 3D conformability. Nanoscale. 2016;8(24):12105-12112.
[DOI] -
48. Zhu B, Niu Z, Wang H, Leow WR, Wang H, Li Y, et al. Microstructured graphene arrays for highly sensitive flexible tactile sensors. Small. 2014;10(18):3625-3631.
[DOI] -
49. Zhang X, Li Z, Du W, Zhao Y, Wang W, Pang L, et al. Self-powered triboelectric-mechanoluminescent electronic skin for detecting and differentiating multiple mechanical stimuli. Nano Energy. 2022;96:107115.
[DOI] -
50. Wang Z, Bu T, Li Y, Wei D, Tao B, Yin Z, et al. Multidimensional force sensors based on triboelectric nanogenerators for electronic skin. ACS Appl Mater Interfaces. 2021;13(47):56320-56328.
[DOI] -
51. Hong J, Rao Z, Duan S, Xiang S, Wei X, Xiao Y, et al. A paradigm shift toward active resistive sensing driven by triboelectric nanogenerator. Nano Energy. 2024;131(Part B):110327.
[DOI] -
52. Xie Y, Pan J, Yu L, Fang H, Yu S, Zhou N, et al. Optical micro/nanofiber enabled multiaxial force sensor for tactile visualization and human-machine interface. Adv Sci. 2024;11(45):2404343.
[DOI] -
53. Lepora NF. The future lies in a pair of tactile hands. Sci Robotics. 2024;9(91):eadq1501.
[DOI] -
54. Wang H, Wang W, Kin JJ, Wang C, Wang Y, Wang B, et al. An optical-based multipoint 3-axis pressure sensor with a flexible thin-film form. Sci Adv. 2023;9(36):eadi2445.
[DOI] -
55. Dvorak , N , Chung , K , Mueller K, Ku PC. Ultrathin tactile sensors with directional sensitivity and a high spatial resolution. Nano Letters. 2021;21(19):8304-8310.
[DOI] -
56. Flavin MT, Ha K, Guo Z, Li S, Kim JT, Saxena T, et al. Bioelastic state recovery for haptic sensory substitution. Nature. 2024;635(8038):345-352.
[DOI] -
57. Yan Y, Hu Z, Yang Z, Yuan W, Song C, Pan J, et al. Soft magnetic skin for super-resolution tactile sensing with force self-decoupling. Sci Robotics. 2021;6(51):eabc8801.
[DOI] -
58. Le Signor T, Dupré N, Didden J, Lomakin E, Close G. Mass-manufacturable 3D magnetic force sensor for robotic grasping and slip detection. Sensors. 2023;23(6):3031.
[DOI] -
59. Dai H, Zhang C, Pan C, Hu H, Ji K, Sun H, et al. Split-type magnetic moft tactile sensor with 3D force decoupling. Adv Mater. 2024;36(11):2310145.
[DOI] -
60. Li Y, Wang G, Zhang S, Zhou Y, Li H, Qi Z. Design and calibration of spoke piezoelectric six-dimensional force/torque sensor for space manipulator. Chin J Aeronaut. 2024;37(1):218-235.
[DOI] -
61. Yoshikawa T, Miyazaki T. A six-axis force sensor with three-dimensional cross-shape structure. In: Proceedings, 1989 International Conference on Robotics and Automation; 1989 May 14-19; Scottsdale. Piscataway: IEEE; 1989. p. 249-255.
[DOI] -
62. Kang MK, Lee S, Kim JH. Shape optimization of a mechanically decoupled six-axis force/torque sensor. Sens Actuators A Phys. 2014;209:41-51.
[DOI] -
63. Palli G, Moriello L, Scarcia U, Melchiorri C. Development of an optoelectronic 6-axis force/torque sensor for robotic applications. Sens Actuators A Phys. 2014;220:333-346.
[DOI] -
64. Kim G, Hwang D. BaroTac: Barometric three-axis tactile sensor with slip detection capability. Sensors. 2022;23(1):428.
[DOI] -
65. Wang X, Liang J, Xiao Y, Wu Y, Deng Y, Wang X, et al. A flexible slip sensor using triboelectric nanogenerator approach. J Phys: Conf Ser. 2018;986:012009.
[DOI] -
66. Lin W, Wang B, Peng G, Shan Y, Hu H, Yang Z, et al. Skin-inspired piezoelectric tactile sensor array with crosstalk-free row+column electrodes for spatiotemporally distinguishing diverse stimuli. Adv Sci. 2021;8(3):2002817.
[DOI] -
67. Hou C, Gao H, Yang X, Xue G, Zuo X, Li Y, et al. A piezoresistive-based 3-axial MEMS tactile sensor and integrated surgical forceps for gastrointestinal endoscopic minimally invasive surgery. Microsyst Nanoeng. 2024;10:141.
[DOI] -
68. Preti ML, Bernabei F, Nardin AB, Beccai L. Triaxial 3D-channeled soft optical sensor for tactile robots. IEEE Sens J. 2024;24:27956-27965.
[DOI] -
69. Yan Y, Hu Z, Shen Y, Pan J. Surface texture recognition by deep learning-enhanced tactile sensing. Adv Intell Syst. 2022;4(1):2100076.
[DOI] -
70. Cheng Y, Ma Y, Li L, Zhu M, Yue Y, Liu W, et al. Bioinspired microspines for a high-performance spray Ti3C2Tx MXene-based piezoresistive sensor. ACS Nano. 2020;14(2):2145-2155.
[DOI] -
71. Wei Y, Chen S, Lin Y, Yang Z, Liu L. Cu-Ag core-shell nanowires for electronic skin with a petal molded microstructure. J Mater Chem C. 2015;3:9594-9602.
[DOI] -
72. Delipinar T, Shafique A, Gohar MS, Yapici MK. Fabrication and materials integration of flexible humidity sensors for emerging applications. ACS Omega. 2021;6(13):8744-8753.
[DOI] -
73. Qiu Z, Wan Y, Zhou W, Yang J, Yang J, Huang J, et al. Ionic skin with biomimetic dielectric layer templated from Calathea zebrine leaf. Adv Funct Mater. 2018;28(37):1802343.
[DOI] -
74. Yan Y, Zermane A, Pan J, Kheddar A. A soft skin with self-decoupled three-axis force-sensing taxels. Nat Mach Intell. 2024;6:1284-1295.
[DOI] -
75. Lee D, Kim J, Kim H, Heo H, Park K, Lee Y. High-performance transparent pressure sensors based on sea-urchin shaped metal nanoparticles and polyurethane microdome arrays for real-time monitoring. Nanoscale. 2018;10:18812-18820.
[DOI] -
76. Ma C, Xu D, Huang YC, Wang P, Huang J, Zhou J, et al. Robust flexible pressure sensors made from conductive micropyramids for manipulation tasks. ACS Nano. 2020;14(10):12866-12876.
[DOI] -
77. Mao B, Zhou K, Xiang Y, Zhang Y, Yuan Q, Hao H, et al. A bioinspired robotic finger for multimodal tactile sensing powered by fiber optic sensors. Adv Intell Syst. 2024;6(8):2400175.
[DOI] -
78. Abderrahmane Z, Ganesh G, Crosnier A, Cherubini A. A deep learning framework for tactile recognition of known as well as novel objects. IEEE Trans Ind Inform. 2019;16(1):423-432.
[DOI] -
79. Khandate G, Shang S, Chang ET, Saidi TL, Liu Y, Dennis SM, et al. Sampling-based exploration for reinforcement learning of dexterous manipulation. arXiv:2303.03486 [Preprint]. 2023. Available from: https://arxiv.org/abs/2303.03486
-
80. Metzger A, Toscani M. Unsupervised learning of haptic material properties. eLife. 2022;11:e64876.
-
81. Qiu Y, Yan C, Zhang Y, Yang S, Yao X, Ai F, et al. A tactile perception method with flexible grating structural color. Nat Sci Rev. 2025;12(1):nwae413.
[DOI] -
82. Kong D, Yang G, Pang G, Ye Z, Lv H, Yu Z, et al. Bioinspired co-design of tactile sensor and deep learning algorithm for human-robot interaction. Adv Intell Syst. 2022;4(6):2200050.
[DOI] -
83. Lyu C, Xiao Y, Deng Y, Chang X, Yang B, Tian J, et al. Tactile recognition technology based on multi-channel fiber optical sensing system. Measurement. 2023;216:112906.
[DOI] -
84. Zhang S, Sun Y, Shan J, Chen Z, Sun F, Yang Y. Tirgel: A visuo-tactile sensor with total internal reflection mechanism for external observation and contact detection. IEEE Robotics Autom Lett. 2023;8(10):6307-6314.
[DOI] -
85. Grover A, Grebe C, Nadeau P, Kelly J. Under pressure: Learning to detect slip with barometric tactile sensors. arXiv:2103.13460 [Preprint]. 2021. Available from: https://arxiv.org/abs/2103.13460
-
86. Lora-Rivera R, Luna-Cortés JA, de Guzmán-Manzano A, Ruiz-Barroso P, Castellanos-Ramos J, Oballe-Peinado Ó. Object stiffness recognition with descriptors given by an FPGA-based tactile sensor. In: 2020 IEEE 29th International Symposium on Industrial Electronics (ISIE); 2020 Jun 17-19; Delft, Netherlands. 2020. Piscataway: IEEE; 2020. p. 561-566.
[DOI] -
87. Chortos A, Liu J, Bao Z. Pursuing prosthetic electronic skin. Nat Mater. 2016;15(9):937-950.
[DOI] -
88. Yang M, Lu C, Church A, Lin Y, Ford C, Li H, et al. Anyrotate: Gravity-invariant in-hand object rotation with sim-to-real touch. arXiv:2405.07391 [Preprint]. 2024. Available from: https://arxiv.org/abs/2405.07391
-
89. Perera PB, Marasingh H, Takami T, Kajimoto H, Withana A. Integrating force sensing with electro-tactile feedback in 3D printed haptic interfaces. In: Proceedings of the 2024 ACM International Symposium on Wearable Computers; 2024 Oct 5-9; New York, United States. New York: ACM; 2024. p. 48-54.
-
90. Zhou S, Han TH, Ding L, Ru E, Zhang C, Zhang YJ, et al. Bilayer gradient hydrogel with topological crosslinking for high-sensitivity tactile perception and information encryption. Adv Funct Mater. 2024;34(27):2313012.
[DOI] -
91. Huang Z, Yu S, Xu Y, Cao Z, Zhang J, Guo Z, et al. In-sensor tactile fusion and logic for accurate intention recognition. Adv Mater. 2024;36(35):2407329.
[DOI]
Copyright
© The Author(s) 2025. This is an Open Access article licensed under a Creative Commons Attribution 4.0 International License (https://creativecommons.org/licenses/by/4.0/), which permits unrestricted use, sharing, adaptation, distribution and reproduction in any medium or format, for any purpose, even commercially, as long as you give appropriate credit to the original author(s) and the source, provide a link to the Creative Commons license, and indicate if changes were made.
Publisher’s Note
Share And Cite