Abstract
The spine is a critical component of the human body, supporting balance, flexibility, and natural movement. However, scoliosis, a condition where the curvature of the spine exceeds 10 degrees, can lead to health complications. In this research, we designed and three dimensional (3D) printed a customized orthosis using the Blender program, supported by ultrasound sensors controlled by an Arduino UNO circuit. Our innovative approach aims to accelerate healing and alleviate pain in patients with scoliosis. This study serves as a starting point for the development of research in the orthotic treatment of scoliosis of the spine by integrating two treatment techniques at the same time. Our ultrasound-reinforced orthosis represents a significant advancement in spinal care, offering a promising solution for scoliosis treatment.
Keywords
1. Introduction
Orthopedic appliances include precision and creativity in the design and manufacture of external orthoses (orthotics) as part of the patient's treatment process, and orthotic devices work to control weak or deformed areas of the body of a physically disabled person. Orthotic devices can be used on different areas of the body including the upper and lower limbs, the skull, or the spine[1].
Common orthotic interventions include scoliosis orthotic devices, HALO devices used in life-threatening neck injuries, and ankle-foot orthoses used in the rehabilitation of children with cerebral palsy[2]. Recently, orthoses have been designed to significantly realign the spinal bones in patients with postural scoliosis[3]. Scoliosis treatment methods have gradually developed with the advancement of scientific techniques, and a lot of research and scientific applications have been carried out in this field, until orthotic devices have become one of the important therapeutic devices used in the medical field.
There has been some research and experiments conducted in this field. Bidari et al.[4] compared braces made in the traditional way with those made through two computer-aided design and numerical analysis techniques: Computer-aided design and computer-aided manufacturing, and aomputer-aided-design and finite elements modeling. The ideal shape of scoliosis braces made using digital fabrication methods was reached in the anterior plane, and in the sagittal plane, where it was found using digital simulation that the printed braces were found through digital simulation to be more effective than traditional braces in the sagittal plane[4]. In the context of using ultrasound in the treatment process and relieving pain resulting from the orthotic process, recent studies investigated the use of ultrasound in relieving lower back pain[5]. It seems that ultrasound therapy is one of the safe and effective methods used in orthopedic and vertebral treatments in addition to traditional methods such as exercise[6], and electrical stimulation therapy[7]. It has been shown that ultrasound therapy can be applied in two modes, continuous or pulsed, and while the continuous mode delivers ultrasound waves non-stop throughout the treatment period, the discontinuous mode delivers pulses of waves and echo processing to deliver intermittently ultrasound for medical imaging that It transmits pulses of ultrasound and processes the echo that reflects the condition and elasticity of the tissue[8]. In general, ultrasound therapy expresses unidirectional energy delivery using the tip of the crystal probe towards the area of injury with a frequency between 1 and 3 MHz and intensity between 0.1 W/cm2 and 3 W/cm2[9]. A number of studies were undertaken including one on a sample of between 30 and 445 people, ranging in age from 31 to 56 years. The duration of treatment ranged from 3 weeks to six months, using several types of treatment. Six randomized clinical trials that evaluated the effectiveness of ultrasound therapy on lower back pain were included. It was shown that therapeutic ultrasound was more effective than other methods in reducing pain associated with the central nervous system[8-11].
The study of Lou et al.[12] indicated the effective role that the 3D ultrasound system can play as a radiation-free method for determining the optimum pressure level and location to obtain the best intra-brace stimulus correction during brace casting. The average number of radiographs per subject taken before final brace implementation with the intervention group was significantly lower than the control group. The safety of using ultrasound in the treatment process and not causing any harm to the patient was confirmed through studies and research, including calibration and electrical safety studies using therapeutic ultrasound for orthopedic, where the study of Daniel et al.[13] aimed to determine the extent to which the ultrasound equipment used by Chiropractors to calibrate conditions, electrical safety standards, and evaluate the frequency of ultrasound therapy use. A cross-sectional study tested 45 ultrasound machines to determine the extent to which the ultrasound equipment used by Chiropractors complied with conditions, electrical safety standards, and evaluated the frequency of ultrasound therapy use. It was found that a large proportion of ultrasound machines in chiropractic clinics presented a slightly increased wave intensity to the patient. The aim of the research is to speed up the healing process and relieve pain in patients with scoliosis, as this research serves as a starting point for the development of ultrasound-assisted orthotic treatment of scoliosis by integrating two treatment techniques simultaneously.
2. Orthosis Design
2.1 The studied case
A magnetic resonance images series was obtained using a device (SIEMENS MAGNETOM Symphony at 1.5 T, Al-Bassel Hospital, Tartus, Syria) of a 32 male patient with lumbar scoliosis and converted into 3D models using Blender software. Figure 1 shows the magnetic resonance image of the patient, and outlines the studied section in which the measurements have been performed.
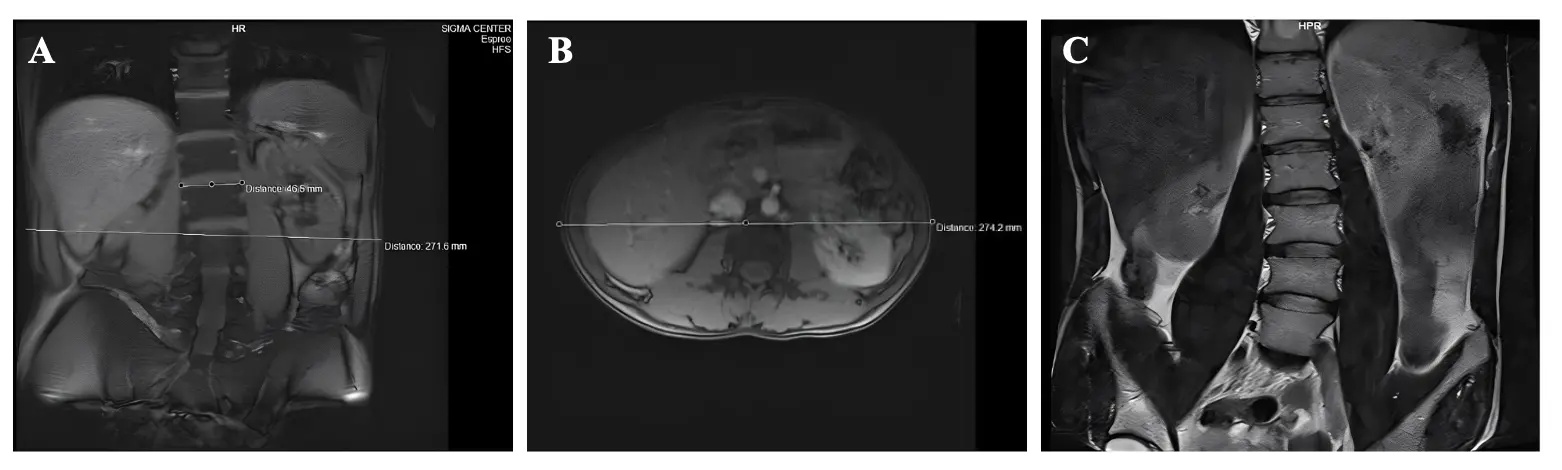
Figure 1. Magnetic resonance imaging of the studied case, highlighting the presence of scoliosis in both the sagittal and axial planes. (A) The sagittal plane showing the studied section; (B) The axial plane section studied; (C) The whole studied case showing the scoliosis in the sagittal plane.
2.2 The 3D design
The 3D model of the customized orthosis was created based on the patient's medical image obtained through magnetic resonance imaging (MRI). The MRI allowed us to study the case and determine the design considerations related to the geometry, size, and materials that would be necessary for creating a successful 3D model. Working in 3D design allowed us to have a close understanding of all the details of the model, ensuring that it was tailored to the patient's unique anatomy and provided effective support for their scoliosis condition.
At this stage, the 3D model was built by locating the decompression and scoliosis sites on the patient's medical image, as shown in Figure 1A,B. The 3D model provided a visualization of the affected area of the spine, enabling us to design an orthosis that provided targeted support and promoted bone remodeling and tissue regeneration.
2.3 The slicing of the model
After taking the cross-sections and surrounding them using the Blender program, for each section of the patient's body as in Figure 2A, the sections were connected to each other, taking into account the real distance between the sections (2 mm), then a mechanical pressure point was created using the opposite pad of scoliosis, and two holes corresponding to the pressure pad were created to install the ultrasound generator to treat muscle contraction that causes scoliosis, as shown in Figure 2B.
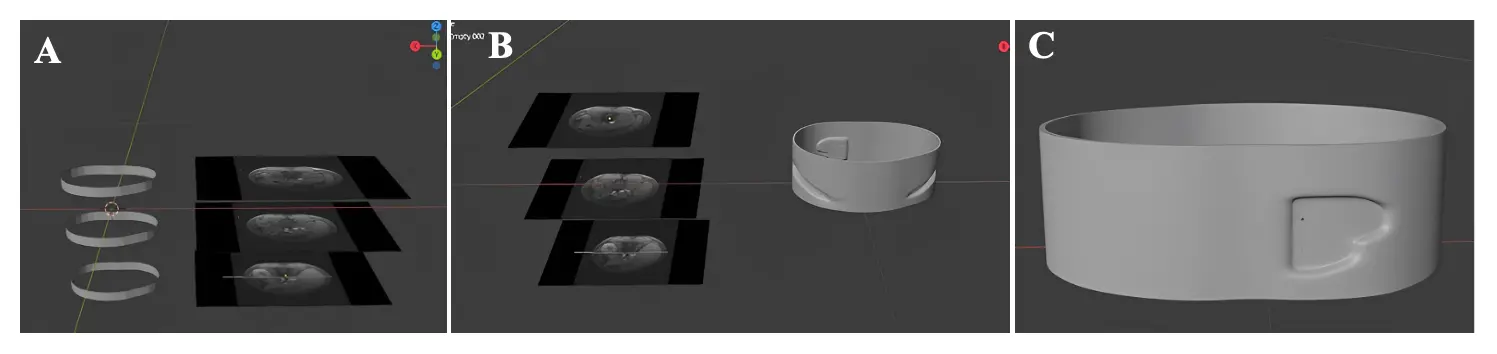
Figure 2. Design of scoliosis orthosis. (A) The contour outline on different slices used to produce the 3D model; (B) The assembly of different slices into a unified numerical and personalized model; (C) The overall resulting model after assembling the separated slices.
2.4 The 3D printing
The design of the customized orthosis was transferred to the 3D printer software in STL format. This allowed us to create a digital model of the orthosis that could be used to manufacture the device without any human intervention. The 3D printing process was automated, starting from the measurements obtained from the patient to the manufacture of the device.
The use of 3D printing technology enabled us to create a customized orthosis that closely matched the anatomical shape of the installation area. The error rate in the final product was very small, ensuring that the orthosis fit the patient's unique anatomy and provided effective support for their scoliosis condition.
Figure 2C shows the final shape of the orthosis after 3D printing. The orthosis was designed to provide targeted support to the affected area of the spine, promoting bone remodeling and tissue regeneration. The use of 3D printing technology allowed us to create a customized orthosis that was both effective and non-invasive, providing a promising treatment option for patients with scoliosis.
2.5 Ultrasonic (US) wave sensor adaptation circuit design
The ultrasonic sensors are controlled by the Arduino UNO circuit in order to speed up the healing process and relieve the patient's pain. In this research, we programmed the Arduino circuit connected with the ultrasonic sensors through a set of commands and instructions written in Arduino C that aims to give a command to the ultrasonic sensors. An audio signal starts transmitting waves for 10 minutes through the ON/OFF button, with a text message displayed on the liquid crystal display (LCD) screen stating that exposure to waves has started.
The exposure to the waves is switched off after the expiry of the exposure time (10 minutes) automatically through a timer with a warning beep to indicate the termination of the exposure process. The start time of exposure to the waves is determined by the doctor in coordination with the patient at his home to ensure his comfort and not to move him to medical centers. Figure 3 shows the diagram of the circuit. It consists of the following components.
2.5.1 Ultrasound source (US sensor)
In our study, the ultrasound sensor (Figure 4A) was a critical component of the treatment system. The sensor was placed on the contracture muscles that were causing scoliosis, next to the mechanical pressure point with a corrective effect for scoliosis through the orthosis. By placing the ultrasound sensor at the site of scoliosis, we were able to deliver ultrasound waves directly to the affected area at a frequency of 3 MHz, promoting bone remodeling and tissue regeneration. The ultrasound waves had a corrective effect on scoliosis by enhancing the mechanical pressure provided by the orthosis and accelerating the healing process. The ultrasound sensor itself was a small, lightweight device that could be easily positioned on the patient's body. The sensor was designed to transmit and receive ultrasound waves, enabling it to both deliver the treatment and monitor its effectiveness. The use of the ultrasound sensor provided a non-invasive and painless treatment option for patients with scoliosis, eliminating the need for more invasive procedures and reducing the risk of complications.
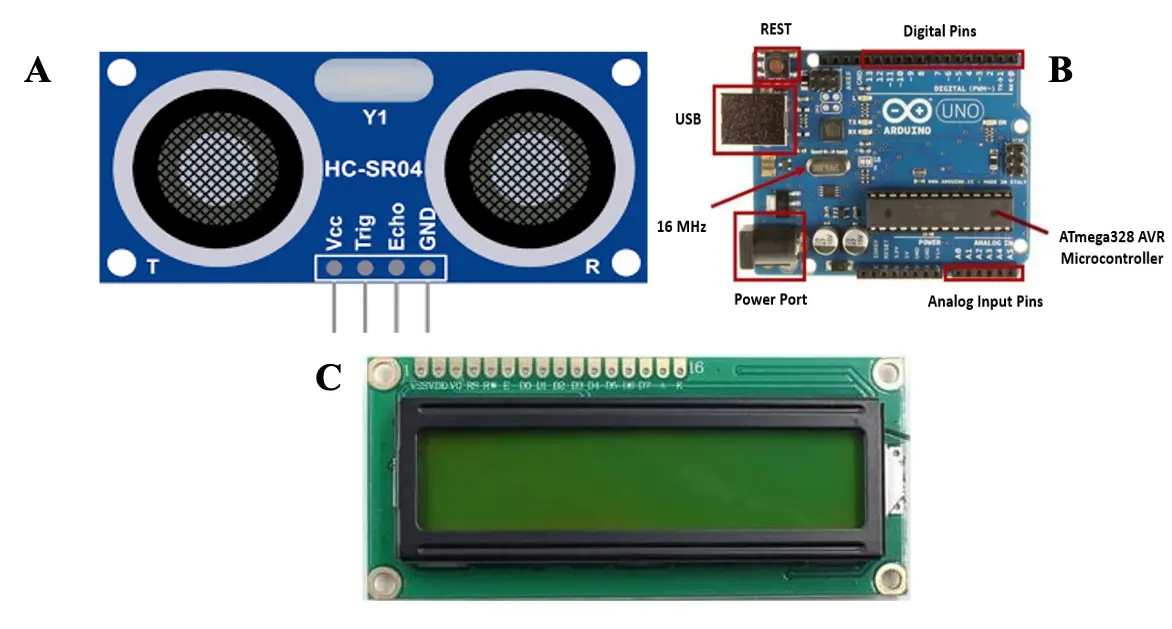
Figure 4. Arduino components used to form the acquisition and treatment system. (A) Ultrasonic part used to send the waves used in bone remodeling; (B) Arduino Mega system used to control all inputs and peripherals of the system; (C) LCD system used to input the parameters and display the progress of the treatment. LCD: liquid crystal display.
2.5.2 Control unit
In our study, we used the Arduino circuit as shown in Figure 4B to control the ultrasound signal transmission and monitor the treatment process. The Arduino circuit is a development board that is equipped with a software environment for the AVR controller from Atmel. The circuit is open-source, meaning that anyone has the right to use and modify its programs and give different operating commands to all circuits connected with it. This made it easy for us to customize the operation of the circuit to suit our specific requirements. The appropriate electrical supply to the controller was secured by using a battery to provide the supply voltage (Vs 5+). The use of a battery as a power source ensured that the circuit could be used in a portable and flexible manner, making it suitable for use in a clinical setting. The battery also provided a stable supply voltage, ensuring that the circuit operated reliably and accurately.
2.5.3 Display screen
In our study, we used an LCD screen (Figure 4C) to display the status of exposure to ultrasonic waves. The use of the LCD screen provided real-time feedback to the user, enabling them to monitor the progress of the treatment and ensure that it was functioning correctly. The LCD screen was connected to the Arduino circuit and was powered using appropriate electrical feeding to display the relevant information. The information displayed on the LCD screen included the start and end time of the treatment, the current status of the treatment, and any error messages that may have occurred during the treatment process. The use of an LCD screen provided a user-friendly interface for patients and healthcare professionals, and helped to ensure that the treatment was delivered accurately and effectively.
2.5.4 Clinical application software
The treatment protocol in our study was installed programmatically within the Arduino circuit, which was connected to the ultrasound sensor. The circuit was programmed to operate via a start button, which initiated a 10-minute exposure period. During this time, the ultrasound signals were transmitted through the orthosis and into the affected area of the spine. The exposure period was automatically ended through a timer and an alarm that worked automatically to indicate the termination of the ultrasound exposure. This ensured that the treatment duration was consistent and standardized across all patients. Once the exposure period was completed, the circuit automatically turned off the ultrasound signal, ensuring patient safety and preventing overexposure to the ultrasound waves. The use of an automated treatment protocol enabled us to ensure accurate and consistent treatment delivery, which is critical for effective treatment outcomes.
3. Results
The integration of advanced imaging and 3D printing technologies facilitated the creation of a customized orthosis for a 32-year-old male patient with lumbar scoliosis. The MRI series, obtained using the SIEMENS MAGNETOM Symphony at 1.5 T (Al-Bassel Hospital, Tartus, Syria), provided detailed images essential for accurate 3D modeling using Blender software. This 3D design process enabled precise visualization of the affected spinal region, allowing the orthosis to be tailored to the patient’s specific anatomy, ensuring targeted support and promoting bone remodeling and tissue regeneration.
After completing the design phase, the next step involved slicing the 3D model and assembling the sections for 3D printing. The orthosis was successfully printed with high accuracy, minimizing errors in the final product. This precise fit was crucial for providing effective support and contributing to the non-invasive treatment of scoliosis.
To further enhance the therapeutic effect of the orthosis, we implemented an ultrasonic wave treatment system controlled by an Arduino Uno R3. Ultrasonic sensors were strategically placed on the contracture muscles, delivering waves at 3 MHz to promote bone remodeling and tissue regeneration. The Arduino circuit, powered by a stable battery supply, ensured precise control of the ultrasound signal, with real-time monitoring provided by an LCD screen.
In addition to the ultrasound system, the incorporation of the HALO Smart Sensor allowed for accurate and non-invasive monitoring throughout the treatment process. This integrated approach demonstrated the potential for customized, minimally invasive scoliosis management.
Finally, with the design and settings completed, a miniature orthosis model assisted by ultrasound technology was ready for application. This model was specifically designed to accelerate the healing process and reduce the pain associated with mechanical correction using the orthotic device. The ultrasound-assisted miniature orthosis was compact and non-invasive, providing a painless and effective treatment option for scoliosis patients, as illustrated in Figure 5.
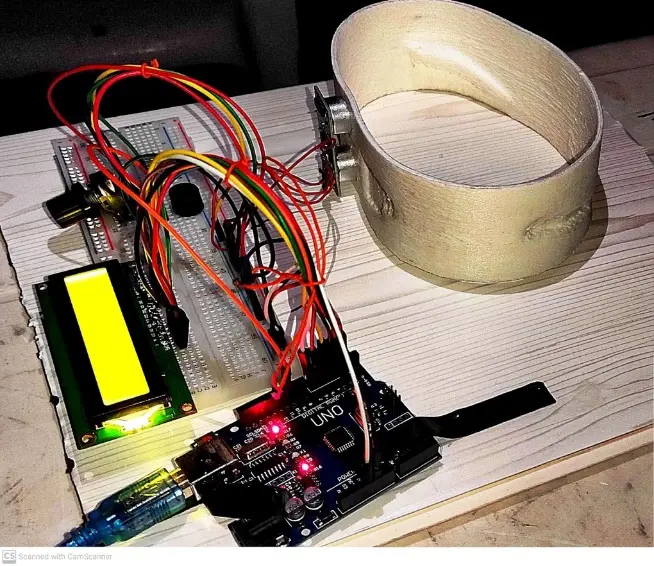
Figure 5. The overall scoliotic spinal orthosis. The components work together to form an integrated system capable of transmitting and processing ultrasound signals, controlling the treatment process, and displaying critical information to the user.
4. Discussion
This study demonstrates the effective integration of advanced imaging, 3D printing, and ultrasonic technology in the development of a customized orthosis for the treatment of lumbar scoliosis. The process began with the acquisition of a high-quality MRI series using the SIEMENS MAGNETOM Symphony at 1.5 T, which provided the detailed anatomical data necessary for creating an accurate 3D model of the patient's spine. Utilizing Blender software for 3D modeling allowed for precise visualization of the affected spinal region, enabling the design of an orthosis that was specifically tailored to the patient's unique anatomical structure.
The accuracy of the 3D printing process played a crucial role in ensuring that the orthosis fit the patient perfectly, minimizing errors and enhancing the overall effectiveness of the treatment. By closely matching the orthosis to the patient's anatomy, we were able to provide targeted support that could promote bone remodeling and tissue regeneration, critical factors in the non-invasive treatment of scoliosis.
The incorporation of an ultrasonic wave treatment system, controlled by an Arduino Uno R3, introduced an innovative element to the orthosis, enhancing its therapeutic potential. The ultrasonic sensors, strategically placed on the contracture muscles, delivered targeted waves at a frequency of 3 MHz, further promoting bone remodeling and aiding in the correction of scoliosis. The Arduino circuit provided precise control over the ultrasound signals, with real-time monitoring facilitated by an LCD screen. This level of control and feedback ensured that the treatment was both effective and safe.
The addition of the HALO Smart Sensor to the treatment system enabled continuous, non-invasive monitoring of the patient's condition throughout the treatment process. This sensor provided valuable data that could be used to adjust the treatment as needed, ensuring that the orthosis delivered optimal results.
The final product, a miniature orthosis model assisted by ultrasound technology, was designed to accelerate the healing process and reduce the discomfort associated with scoliosis treatment. The compact and non-invasive nature of the device made it suitable for extended wear, providing a promising alternative to more invasive treatment options.
The integration of these advanced technologies offers a new, patient-specific approach to scoliosis management. The successful application of this method highlights the potential for using personalized, technology-driven solutions in the treatment of complex musculoskeletal conditions. This approach not only improves treatment outcomes but also enhances patient comfort and compliance, marking a significant step forward in the field of orthopedic rehabilitation. Further studies with larger patient samples and longer follow-up periods are needed to validate these findings and explore the full potential of this innovative treatment approach.
5. Conclusion
In this prototype, we integrated two treatment techniques to address the complexities of scoliosis management. Building on prior studies and theoretical principles, we developed a customized orthosis specifically for lumbar scoliosis, enhanced with ultrasound technology to accelerate healing and alleviate pain associated with mechanical pressure. The successful implementation of this combined system marks a significant advancement in orthotic and support devices, offering substantial support for recovery from scoliosis.
Our innovative approach represents a substantial step forward in the development of orthoses and support devices, leveraging cutting-edge technology to enhance patient outcomes. Nonetheless, further research is essential to fully assess the effectiveness of this treatment approach across different pathological conditions and to evaluate the precision and impact of the sensor parameters. We are confident that ongoing research in this field will lead to even more effective and personalized orthotic solutions, ultimately improving patient outcomes and overall quality of life.
Acknowledgements
The authors would like to thank the University of Miskolc (Institute of Machine and Product Design) in Hungary and the University of Magdeburg (Institute of Mechanics) in Germany for their unlimited support.
Authors contribution
Darwich MA: Conceptualization, methodology, data curation, software, supervision, project administration, validation.
Szávai S: Investigation, visualization, formal analysis, supervision, project administration, validation, writing-original draft.
Nazha HM: Conceptualization, methodology, data curation, software, resources, writing-review and editing.
All authors have read and agreed to the final version of the manuscript.
Conflicts of interest
All authors declare that they are bound by confidentiality agreements preventing disclosure of conflicts of interest in this work.
Ethical approval
Not applicable.
Consent to participate
Not applicable.
Consent for publication
Not applicable.
Availability of Supporting Data
Data are available on request from the corresponding author.
Funding
None.
Copyright
© The Author(s) 2023.
References
-
1. Shahar FS, Sultan MTH, Md Shah AU, Safri SNA. Natural fibre for prosthetic and orthotic applications-a review. In: Jawaid M, Hamdan A, Hameed Sultan MT, editors. Structural Health Monitoring System for Synthetic, Hybrid and Natural Fiber Composites. Composites Science and Technology. Singapore: Springer; 2021. p. 51-70[DOI]
-
2. Darwich A, Nazha H, Sliman A, Abbas W. Ankle-foot orthosis design between the tradition and the computerized perspectives. Int J Artif Organs. 2020;43(5):354-361.[DOI]
-
3. Karimi MT, Rabczuk T. Scoliosis conservative treatment: a review of literature. J Craniovertebr Junction Spine. 2018;9(1):3-8.[DOI]
-
4. Bidari S, Kamyab M, Ghandhari H, Komeili A. Efficacy of computer-aided design and manufacturing versus computer-aided design and finite element modeling technologies in brace management of idiopathic scoliosis: a narrative review. Asian Spine J. 2021;15(2):271-282.[DOI]
-
5. Haile G, Hailemariam TT, Haile TG. Effectiveness of ultrasound therapy on the management of chronic non-specific low back pain: a systematic review. J Pain Res. 2021;14:1251-1257.[DOI]
-
6. Kotwicki T, Chowanska J, Kinel E, Czaprowski D, Tomaszewski M, Janusz P. Optimal management of idiopathic scoliosis in adolescence. Adolesc Health Med Ther. 2013;4:59-73.[DOI]
-
7. Facci LM, Nowotny JP, Tormem F, Trevisani VFM. Effects of transcutaneous electrical nerve stimulation (TENS) and interferential currents (IFC) in patients with nonspecific chronic low back pain: randomized clinical trial. Sao Paulo Med J. 2011;129:206-216.[DOI]
-
8. Allen RJ. Physical agents used in the management of chronic pain by physical therapists. Phys Med Rehabil Clin N Am. 2006;17(2):315-345.[DOI]
-
9. Cornwall MW. Electrotherapy Explained: Principles and Practice, ed 4. Phys Ther. 2007;87(8):1088.[DOI]
-
10. Gallo JA, Draper DO, Brody LT, Fellingham GW. A comparison of human muscle temperature increases during 3-MHz continuous and pulsed ultrasound with equivalent temporal average intensities. J Orthop Sports Phys Ther. 2004;34(7):395-401.[DOI]
-
11. Durmus D, Durmaz Y, Canturk F. Effects of therapeutic ultrasound and electrical stimulation program on pain, trunk muscle strength, disability, walking performance, quality of life, and depression in patients with low back pain: a randomized-controlled trial. Rheumatol Int. 2010;30(7):901-110.[DOI]
-
12. Lou EH, Chan AC, Donauer A, Tilburn M, Hill DL. Ultrasound-assisted brace casting for adolescent idiopathic scoliosis, IRSSD Best research paper 2014. Scoliosis. 2015;10(1):1-6.[DOI]
-
13. Daniel DM, Rupert RL. Calibration and electrical safety status of therapeutic ultrasound used by chiropractic physicians. J Manipulative Physiol Ther. 2003;26(3):171-175.[DOI]
Copyright
© The Author(s) 2023. This is an Open Access article licensed under a Creative Commons Attribution 4.0 International License (https://creativecommons.org/licenses/by/4.0/), which permits unrestricted use, sharing, adaptation, distribution and reproduction in any medium or format, for any purpose, even commercially, as long as you give appropriate credit to the original author(s) and the source, provide a link to the Creative Commons license, and indicate if changes were made.
Publisher’s Note
Share And Cite
Science Exploration Style
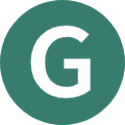
Science Exploration Style
