Abstract
With the development of 3D printing technologies, cellulose has been explored to realize its sophisticated geometry fabrication in this field for a variety of applications. This review focuses specifically on the latest research progress of 3D printing cellulose by discussing the characteristics of cellulose materials, different 3D printing technologies, and their optimal performance for applications in various fields like biomedicine, food packaging, and tissue engineering. The challenges of preparing 3D printing "ink" of cellulose using dissolved cellulose or nanocellulose are introduced. Finally, the corresponding applications of cellulose using 3D printing are classified and the strategies to optimize production performance are provided.
Keywords
1. Introduction
3D printing is an innovative technology fabricating production through additive manufacturing with desirable materials layer by layer[1]. In the past four decades, 3D printing has gradually developed into commercialized techniques to offer great benefits in industries, such as less raw material, fewer steps, cost savings, and customized geometry without additional technical assistance to maintain product shapes. Currently, the main challenges in 3D printing come from developing practically efficient materials and corresponding 3D printing optimization.
Different materials can be used in 3D printing, such as polymers, metals, ceramics, sand and wax. The common polymers applicable for 3D printing are polylactic acid (PLA), acrylonitrile butadiene styrene (ABS), and nylon, which are toxic to mankind after heating in high temperatures. Cellulose, the main element to build plant cell walls, is well known for its abundance, biocompatibility, and degradability[2]. As the most abundant natural polymer in the world, the raw materials of lignocellulose come from various plants, including wood, cotton, wheat straw, rice straw, reeds, hemp, mulberry bark, paper mulberry bark, sugarcane bagasse, etc.
Lignocellulose production on Earth is approximately 18 to 70 × 1010 billion tons annually[3]. It accounts for more than 50% of the carbon content in the plant kingdom and can be continuously regenerated through photosynthesis. However, only a small percentage of cellulose is effectively used[4].
Cellulose also has excellent mechanical properties and low toxicity, making it an ideal candidate for 3D printing biomaterial products[5]. Without causing significant immune or rejection reactions, cellulose is promising to be implanted in the body for a long time, which is particularly important for medical devices or tissue engineering materials[6]. Abundant functional groups (e.g., -OH groups) on cellulose fibril surfaces afford high bioactivity to bind strongly with important agents with special functions[7]. For instance, graphene nanosheets (GNS) or carbon nanotubes (CTN) can be bound to cellulose fibers via the hydroxyl groups to form a conductive interwoven network with macropores. The reported GNS/cellulose nanopaper shows high mechanical strength, excellent electrical conductivity, and strong electroactivity[8].
One favorable property of cellulose for 3D printing is its biodegradability. Cellulose can gradually degrade into small molecular substances, such as glucose, through the decomposition action of natural microorganisms. These substances can be absorbed by the organism, reducing long-term burdens on its body and degrading cellulose environmentally friendly[9]. Furthermore, cellulose degradation can be controlled through many chemical or physical methods and the degradation rate can be regulated to meet the needs of different 3D printing application scenarios[10].
Cellulose can thermally decompose before it becomes extrudable in fused deposition modeling (FDM) 3D printing. Inkjet 3D printing is a practical technique for cellulose 3D printing. However, the key scientific questions for 3D printing cellulose are the dissolution and processing of cellulose due to its insoluble nature in common organic and inorganic solutions. Enhancement of cellulose dissolution in a feasible solution constitutes the key challenge for realizing cellulose 3D printing. Owing to the formidable challenge in 3D printing of raw cellulose materials, nanocellulose (cellulose materials on a nanosize scale) opens up new avenues for practical 3D printing. Nanocellulose is mainly used as a filler to enhance the mechanical properties of products. The elastic modulus of nanocellulose can reach 150 GPa due to its lightweight, high stiffness, and superior mechanical strength. Nanocelluloses with cellulose I crystals have a super high tensile strength of approximately 17.8 GPa, seven times that of steel. With a high specific surface area of higher than 250 m2 g-1, more activated hydroxyl groups are exposed on the fiber surfaces and improve its strength and the ease of modification by oxidation, esterification, etherification, grafting copolymerization, and cross-linking reactions, etc.[11]. Cellulose nanocrystals (CNCs) also can function as additives, internal/external lubricants, are used with CNCs to improve surface properties of 3D printing products[12]. The excellent elasticity of cellulose/nanocellulose provides good ductility for 3D printing products, which can withstand external forces to a certain extent without breaking. This is very important for biomaterials in bone tissue engineering, which require excellent elasticity to prevent bone implant fracture under higher pressure.
Recently, the rapid development of 3D printing technology has provided new avenues for preparing complex structural materials, and the research on the applications of cellulose as a biomaterial in the field of 3D printing is of significant importance. The literature for 3D printing bulk cellulose and nanocellulose is increasing sharply each year[13-15].
2.3 D Printing Technology
3D printing technology is based on the principle of building three-dimensional solid objects by adding materials layer by layer. 3D printing technology differs from traditional manufacturing methods by using an additive manufacturing (AM) method[16]. AM includes a set of manufacturing techniques that build objects from the bottom up and layer-by-layer while traditional "subtractive" manufacturing produces objects by removing material from bulk materials, such as engraving, grinding, forging, etc. 3D printing technology offers a high degree of freedom, automation, and precision while eliminating the need for traditional molds, stamping dies, or flat engraving dies[17]. 3D printing technology enables people to design and finish the product rapidly without preparing modules and conducting pre-treatment, saving cost due to individual processing.
The first 3D printing process in the world was patented in 1986 by Charles W. Hull, named "Stereolithography"[18]. Since its inception, 3D printing has become increasingly popular.[17] In summary, it is valued for its potential to provide prototypes, customer-specific designs, high structural complexity, and rapid on-demand small batch, low-cost manufacturing. It is also considered to be the next revolution in manufacturing[19].
The core process mainly includes the following steps:
(1) 3D Model Design: Use CAD software to design a three-dimensional model of the target object. This model can be newly created or obtained by scanning a physical object to create a digital model.
(2) File Format Conversion: After completing the design, the three-dimensional model can be converted into a file format that the printer can recognize, such as an STL (Standard Tessellation Language) file. STL files represent the surface of the object as a triangular mesh, facilitating slicing by the printer.
(3) Slicing Process: Use specialized slicing software to decompose the STL file into a series of two-dimensional slices (layers), each representing a cross-section of the object at a certain height. These slice data will guide the printer to build the object layer by layer.
(4) Printing Process: The printer constructs the three-dimensional object layer by layer using specific printing techniques and materials, according to the slice data. Different printing technologies (such as FDM, stereolithography (SLA), selective laser sintering (SLS), etc.) differ in the way materials are deposited or cured.
(5) Post-Processing: After printing, a series of post-processing operations may be required, such as removing support structures, sanding, polishing, coloring, etc., to improve the surface quality and mechanical strength of the object.
Common 3D Printing Technologies can be classified as below:
(1) FDM:
Principle: Heated filaments of thermoplastic materials (such as PLA, ABS, etc.) are melted and extruded through a nozzle layer by layer onto the build platform, where they cool and solidify.
Characteristics: Lower cost, relatively simple operation, suitable for beginners and home use. A variety of printing materials are available, but the surface quality may not be as good as other high-precision printing technologies.
(2) SLA:
Principle: A laser or digital light projector is used to project light onto the surface of liquid photosensitive resin, causing it to solidify layer by layer.
Characteristics: High printing precision, smooth surface, capable of producing complex structures and high-precision models. However, the equipment and material costs are higher.
(3) SLS:
Principle: A laser is used to sinter powdered materials (such as nylon, metal powders, etc.) together layer by layer to form an object. The unsintered powder material acts as a support structure, eliminating the need for additional support.
Characteristics: A wide range of materials can be used, and parts with robust structures can be produced. Suitable for manufacturing objects with complex geometries, but post-processing may be relatively complex.
(4) Inkjet printing:
Inkjet 3D printing technology is based on the traditional inkjet printing principle, but it is applied to the construction of three-dimensional objects. The basic principle is to use "bio-ink" or special inks to form droplets at a certain frequency through heating or piezoelectric methods, and then precisely spray them onto the printing platform through the nozzle, building up layer by layer to form a three-dimensional entity[20].
3. Dissolution Challenges of Cellulosic Biomaterials
Cellulose has been well known to be insoluble in water and many organic solvents. The solubility of cellulose is related to its structure and intermolecular/intramolecular hydrogen bonding. Cellulose consists of repeating β-D-glucopyranose units covalently linked through acetal functions between the C1 carbon atom and the C4 carbon atom, with an equatorial-OH group (β-1,4-glycosidic bonds)[21]. Hydroxyl groups are uniformly distributed at different crystal planes being hydrophilic/hydrophobic interfaces. Limited solvents have been developed to dissolve cellulose by forming hydrogen bonds with cellulose chains. The reported solvents are listed below:
NMMO: NMMO is a non-derivative solvent system with dipolar nitrogen atoms that easily break the hydrogen bonds between cellulose molecules and form new coordination bonding with oxygen atoms in a limited temperature window around 110 °C, resulting in the dissolution of cellulose. The hydrogen bonding between NMMO and cellulose chains first forms in the amorphous region and subsequently in the crystalline region until complete cellulose dissolution. However, N-O bonding is thermally unstable and can break when the water in the solution is not within the limited dissolution range. NMMO is a promising solvent for realizing cellulose 3D printing[13,22].
Ionic Liquids: Ionic liquids (ILs) are organic salts containing strong hydrogen-bonded receptors, which cause dissolution through their interaction with hydroxyl groups on cellulose fibers[23]. Anion modules in ILs combine with the protons of hydroxyl groups and form electron donor-acceptors to destroy hydrogen bonding in cellulose. Cation modules also contribute to cellulose dissolution while saturated cations reduce such dissolution capability. The mechanism of the dissolution needs further investigation. ILs are non-volatile, easily recoverable, high polar, chemically stable, and environment-friendly. However, the cost of ILs is high, which limits their large-scale applications.
LiCl/N, n-dimethylacetamide (LiCl/DMAc): The LiCl/DMAc solvent system is also a classical and direct solvent system for cellulose dissolution. It has beenwidely used for cellulose analysis and chemical modification[24]. However, the dissolution rate is relatively low, even for pretreated cellulose. This is because DMAc must activate cellulose chains to a relaxed state. This is a long period. With the interaction between Li+ ions and cellulose, the protons in cellulose chains can form strong hydrogen bonding with Cl-. The repulsion between charges anchored on the cellulose system can take the cellulose fibrils apart and dissolve cellulose chains.
Deep eutectic solvents (DESs): DESs also can dissolve cellulose by competing for hydrogen bonding with cellulose and improving cellulose reactivity. However, their dissolution capability is not high enough. Other reagents like ZnCl2 /CaC, must be added after the pretreatment process using DESs for dissolution. As a new type of green solvent, deep eutectic solvents have shown strong development potential in the preparation and functional application of nanocellulose[25,26].
Alkali/urea and NaOH/thiourea: This system was invented by Cai et al. using NaOH and urea at a low temperature of -12 °C to freeze/thaw the immersed cellulose repeatedly[27]. Cellulose forms hydrogen bonding-induced complexes with alkali and urea in a shell, where the hydroxide breaks the hydrogen bonding among cellulose chains when the temperature is low. Meanwhile, Na+ ions form hydrates to prevent recrystallization of cellulose. This strategy is effective for dissolving cellulose with relatively low molecular weight. 3D printing of cellulose in NaOH/urea ink was studied by Jiang et al.[28], Baniasadi et al.[29], and Lan et al. for various applications[30].
Molten salt hydrates: This system uses cations in a series of Lewis acids to break the hydrogen bonding to realize cellulose dissolution. Meanwhile, metal cations combine with water to form coordination complexes, protecting anions and causing cellulose dissolution in the layer[31]. To the best of our knowledge, since the regenerated cellulose from the dissolution systems exhibited low mechanical properties, no reports using this solvent have been found in cellulose 3D printing.
Quaternary ammonium hydroxides (QAH): This system uses anions to react with the protons of the hydroxyl groups on cellulose while using methylene groups on the cations to interact with carbocation (C1) on cellulose. When QAH-cellulose intermediates form, the hydrogen bonding in cellulose is broken and cellulose dissolution is achieved[32]. QAH has emerged recently as cellulose solvents, including tetramethylammonium hydroxide (TMAH), tetrabutylammonium hydroxide (TBAH), tetrapropylammonium hydroxide (TPAH). QAH can dissolve cellulose by high concentration and at a mild temperature range of 16-40 °C, which is ideal for inkjet 3D printing of cellulose.
The appropriate green solvents for cellulose are urgently needed for extended cellulose application in 3D printing as biomaterials in the modern era.
4. Preparation of Cellulosic Nanomaterials
Many researches have been conducted to achieve 3D printing by nanocellulose. It is imperative to introduce the preparation of this nanomaterial and how to achieve its 3D printing (Table 1). Nanocellulose has emerged as a biomaterial with application growth at an avalanche rate. Nanocellulose can be prepared through mechanical grinding, high-pressure homogenization, enzymatic treatment, 2,2,6,6-tetramethylpi- peridin-1-yloxy (TEMPO) catalyzed oxidation and ultrasonication strategies[33]. New techniques to prepare nanocellulose are desirable to reduce costs for large-scale production.
Preparation Method | Specific Effect | Properties | Differences and Limitations |
Mechanical Disintegration | Produces a range of particle sizes | High aspect ratio, good dispersion, high mechanical strength | Energy-intensive, may require multiple passes for uniform particle size |
Chemical Treatment | Removes amorphous regions, leaving crystalline structures | Enhanced crystallinity, high thermal stability, tailored surface chemistry | Acid hydrolysis: simpler but lower yields and smaller particles; TEMPO-oxidation: better control but complex and costly |
Enzymatic Treatment | Enzymes selectively degrade certain regions of cellulose | Mild process conditions, environmentally friendly, high yields potential | Enzyme specificity limits particle size control, slower process |
Biological Methods | Fungi degrade cellulose naturally | Sustainable, eco-friendly, potential for large-scale production | Difficult to control particle size and morphology, slower process |
TEMPO: 2,2,6,6-tetramethylpi- peridin-1-yloxy.
Mechanical Method: Using mechanical actions like friction, collision, and shear to modify the crystalline structure of cellulose.
(1) High-pressure Homogenization Method: Cellulose suspension is passed through a high-pressure homogenization device, where it is dissociated into nanoscale particles under the action of high-speed shearing and collision. This method effectively breaks and disperses cellulose bundles, resulting in uniformly dispersed nanocellulose particles.
(2) High-energy Ball Milling Method: This method uses a high-speed rotating ball mill jar and balls to grind the cellulose. During the ball milling process, the high-speed rotation and collision of the balls generate strong shearing and impact forces, gradually breaking down cellulose into nanoscale particles.
Chemical Method: Using the action of chemical reagents to change the morphology and structure of cellulose.
(1) Acid Hydrolysis Method: Cellulosic materials are hydrolyzed under acidic conditions, typically using strong acids such as concentrated sulfuric acid or hydrochloric acid to break down the polymer chains of cellulose, resulting in nanocellulose at the nanoscale. Nanocellulose prepared by the acid hydrolysis method has high purity and crystallinity[34].
(2) Enzymatic Hydrolysis Method: Cellulose is hydrolyzed using cellulase enzymes. Cellulase enzymes can hydrolyze the β-1,4-glycosidic bonds of cellulose, breaking it down into nanocellulose. Nanocellulose prepared by the enzymatic hydrolysis method is relatively gentle and environmentally friendly, and can retain the crystalline properties of cellulose[35].
(3) Oxidation Method: Cellulose is treated with chemical oxidants (such as chromic acid or hydrogen peroxide). The oxidants can oxidize the hydroxyl and methyl groups of cellulose, breaking it down into nanocellulose. The chemical oxidation method can modulate the functional groups and surface properties of cellulose.
Biological Method: Using biotechnologies such as enzymatic hydrolysis to prepare cellulose with specific structures.
(1) Microbial Fermentation Method: Utilizes specific microorganisms (such as acetic acid bacteria) to produce nanocellulose through a biosynthetic process. The process of microbial synthesis of nanocellulose includes microbial cultivation, expression of cellulose biosynthetic enzymes, and the synthesis of cellulose. This method can control the structure and properties of cellulose by regulating microbial cultivation conditions and genetic engineering technology[36].
(2) Plant Tissue Culture Method: Utilizes plant tissue culture technology to prepare nanocellulose by culturing and growing plant cells. This method can regulate the morphology and structure of cellulose by controlling the composition of the culture medium and growth conditions[37].
5. Application of 3D Printing Cellulose
Cellulose materials from wood, cotton, bamboo, etc. have been used in engineering to fabricate paper, textiles, and medicine for centuries. The applications of 3D-printed cellulose products in Engineering and scientific fields are developing rapidly. Owing to the advantages of excellent mechanical properties, non-toxicity, biocompatibility, sustainability, biodegradability, hydrophilicity, and ease of chemical modification, such products can be used for composite materials with high quality, biomedical engineering, food industry, electronics, tissue engineering, functional materials, biological devices, energy storage and conversion devices, and textiles preparation. Some applications are discussed here.
5.1 Biomedical applications
Currently, individual drug therapy is distinguished from group drug therapy to meet the needs of precision medicine. 3D printing technology plays a major role in pharmaceutical innovation and in producing personalized and customized pharmaceutical preparations in a variety of fields, such as tissue engineering, drug delivery, regenerative medicine, and wound healing, which are applications that cellulose can typically address. Through 3D printing technology, different categories of drugs can be designed, including multi-release drug preparation, zonal compound preparation, profiled preparation and high-loading preparation, etc. Pressure extrusion technology is used mainly in 3D printing cellulose to maintain its superior properties due to mild parameters like low temperature[38]. However, insufficient liquidity at a low temperature will lead to extrusion difficulties or rapid solidification that blocks the nozzle and affects printing accuracy. Yang et al. 3D printed nine different shapes of ibuprofen for controlled drug release using gelatin, glycerin, and microcrystalline cellulose (Figure 1)[39]. Owing to its biocompatibility, cellulose does not lead to excessive immune response or rejection, satisfying the base of choice in the drug-controlled release system. This ensures cellulose a carrier that can safely and effectively release drugs in the organism while reducing the adverse effects on the body[40]. Additionally, drugs can be effectively mixed with cellulose and form a stable complex to maintain their activity and stability in the controlled release process[41].The biocompatibility of cellulose also allows for adjustment of its ratio to other materials and/or additives, thereby accurately controlling the release rate and time of drugs[42]. This is particularly important for treatment regimens that require prolonged stable release of drugs, such as chronic disease treatment or situations where continuous drug therapy is necessary[43].
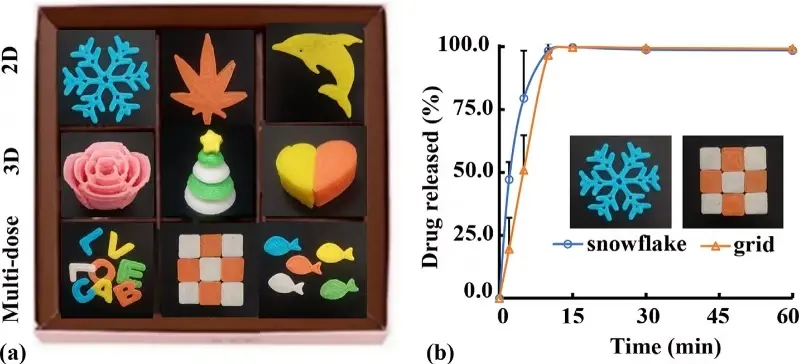
Figure 1. Appearance (a) and in vitro ibuprofen dissolution characteristics (b) of immediate-release preparations. Republished with permission from[39].
Acid solution is a good choice when preparing a nanocellulose-based drug-controlled-release system, which can maintain the high crystallinity of nanocellulose and its high purity. This is important to satisfy the high standards of a drug-controlled-release system. Meanwhile, by controlling reaction conditions and hydrolysis time, the properties of the nanocellulose can be adjusted to meet the specific drug release requirements[43].
To meet the controlled release requirements for drugs, purified nanocellulose particles are mixed with an appropriate amount of solvent, such as water or organic solvent, to form an "ink" suitable for 3D printing. Different cellulosic ethers, such as EC, HPC, and CMC, are commonly used as viscosity modulators in the 3D printing process to achieve high viscosity, and slow flocculation kinetics of the "ink" to facilitate the fabrication of unsupported spanning structures[43-46]. Currently, the optimized content of each component is determined through empirical experiments and then feedback to study the corresponding 3D printing effect and drug-controlled release performance. Simple 3D devices like desktop 3D printers can realize drug-control-release systems and 3D print paper-based microfluidic analytical devices like cellulose-based μ-PADs[47]. Such μ-PADs are driven by the capillary force of cellulose powder so that it can transport liquid-like fluid delivery in the paper. Depending on the ease of the printed microchannels at different depths, programmable capillary flow rates were achieved within the cellulose powder. Flow velocity depends linearly on the channel depth. Figure 2 shows the photographs of the Li4Ti5O12 (LTO) and LiFePO4 (LFP) inks and their apparent ink viscosity as a function of shear rate. Figure 2d and Figure 2e show 3D printing LFP ink (60 wt.% solids) through a 30 μm nozzle to yield a multilayer structure and the corresponding scanning electron microscopy (SEM) images.
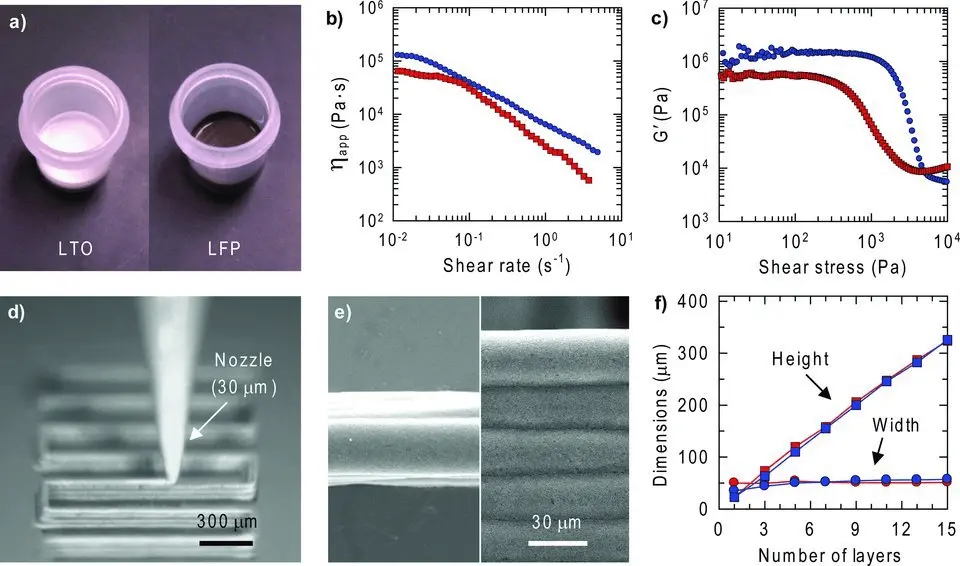
Figure 2. (a) Optical images of LTO and LFP inks; (b) apparent ink viscosity as a function of shear rate; (c) storage modulus as a function of shear stress for each ink; (d) optical image of LFP ink (60 wt.% solids) deposition through a 30 μm nozzle to yield multilayer structure; (e) SEM images, top (left) and side (right) views, of the printed and dried multilayer LFP structure; (f) height and width of printed features as a function of the number of printed layers (30 μm nozzle diameter). Note: Red and blue symbols correspond to data obtained on LTO and LFP inks, respectively. Republished with permission from[46]. LTO: Li4Ti5O12; LEP: LiFePO4; SEM: scanning electron microscopy.
Drugs can be loaded into the cellulose-based drug carriers during or after the 3D printing process. 3D printed porous structure and high adsorbability of cellulose facilitate slow release and prolonged duration of drugs[48]. The controlled release of drugs can be further realized by designing different shapes and structures and regulating the composition and properties of the material. Necessary post-treatments, such as drying and curing can improve the stability and durability of the 3D printed drug carrier[49]. The controlled release performance, biocompatibility, and therapeutic efficacy of the 3D-printed drug carrier also evaluated by in vitro and in vivo experiments.
Drug-control-release functions can be integrated into tissue engineering (TE) scaffolds. TE scaffold preparation is among the predominant applications of 3D printing technology, which enables the possibility to create TE scaffolds with customizable shapes and precise pore sizes, according to specific requirements of the target tissue[50]. The porous structure allows for the efficient infiltration of cells and growth factors, essential for promoting tissue regeneration. Meanwhile, the pores can provide the necessary space for cell proliferation and migration, enabling new tissue formation that integrates well with the surrounding native tissue[51]. Furthermore, the porous structure facilitates the exchange of nutrients and waste products. With a large surface area, cellulose-based scaffolds exhibit merits for cell attachment and growth[52]. These properties are crucial for maintaining cell viability and promote tissue repair and regeneration[53]. Being biodegradable and biocompatible polysaccharide, cellulose TE scaffolds can offer many advantages for regenerative medicine, supporting it as an ideal biomaterial for biomedical applications[52].
Furthermore, 3D printed cellulose-based TE scaffolds can mimic the natural extracellular matrix (ECM) of tissues due to their low cytotoxicity, good biocompatibility, and the similar structure of the ECM in natural tissues. This also enhances their ability to provide a more physiologically relevant environment for cells to grow and function and improve tissue repair and regeneration outcomes, thereby potentially revolutionizing the regenerative medical industry. Figure 3 shows the procedure for apple-derived cellulose scaffolds for 3D mammalian cell culture.
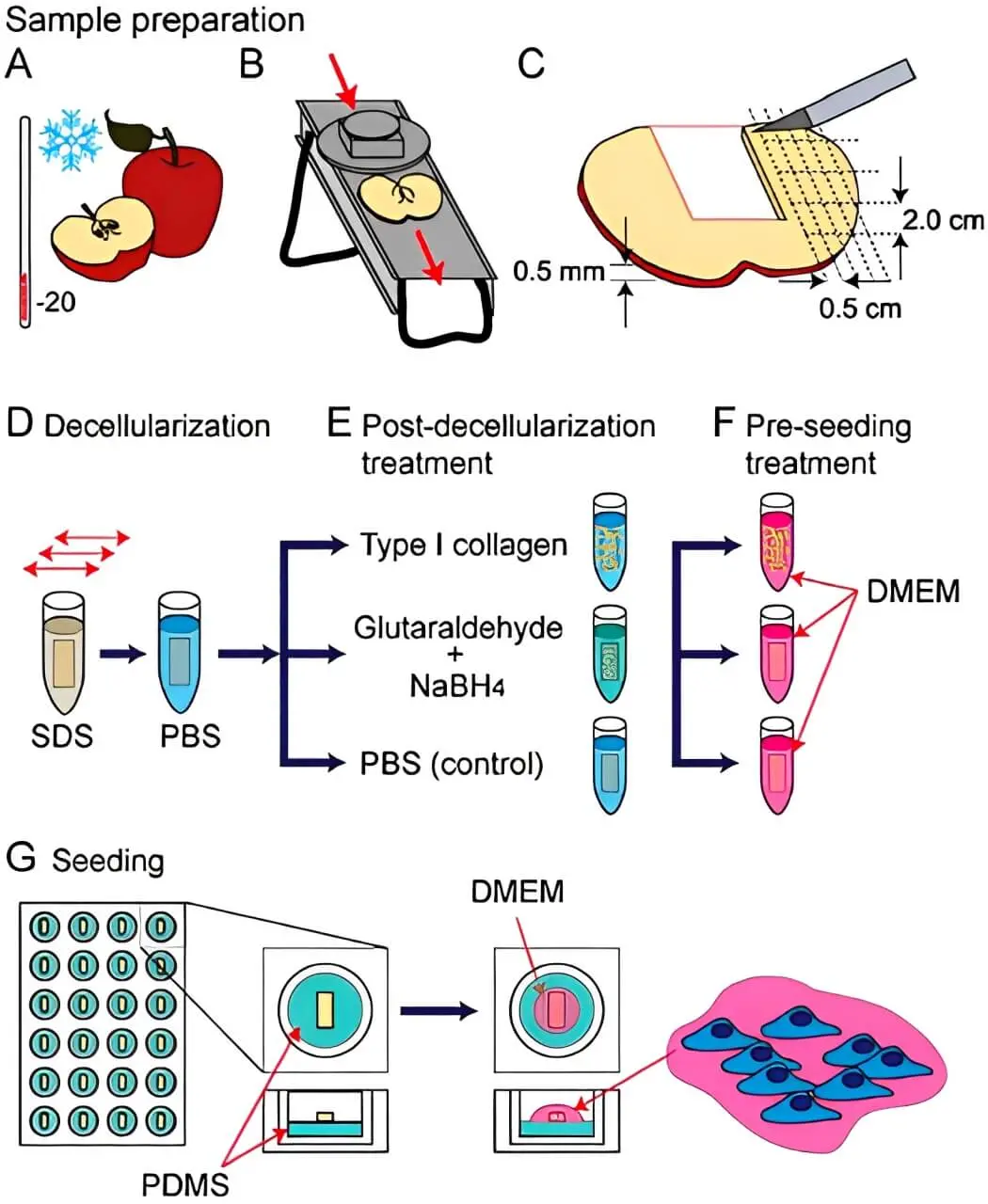
Figure 3. Procedure for apple derived cellulose scaffolds for 3D mammalian cell culture. (A) McIntosh red apples dried out at 220 °C for a maximum of 5 min to harden the outside hypanthium tissue; (B) apples are thinly and evenly sliced with a mandolin slicer, then cores removed; (C) uniform 2.0 by 0.5 cm segments are cut out of the apple slices and placed in separate microcentrifuge tubes; (D) decellularization of apple segments; (E) segments are prepared with varying surface chemistries including coating with Type 1 collagen, chemical cross-linking with glutaraldehyde, or incubation in PBS; (F) scaffolds are placed in mammalian cell culture medium (DMEM) for 12 h in a standard tissue culture incubator at 37 °C and 5% CO2; (G) cell seeding was carried out in PDMS-coated 24 well plates. A 40 mL cell suspension in each well was incubated for 6h, then filled with DMEM for cell culture for up to 12 weeks. Republished with permission from[49]. SDS: sodium dodecyl sulfate; PBS: phosphate-buffered saline; PDMS: poly(dimethyl-siloxane).
3D printing cellulose also shows a wide potential in the trauma dressing field. With excellent biocompatibility, cellulose can coexist with a biological system without causing adverse effects. Triple-D cellulose-based biomaterials (a type of trauma dressings) can be designed to exhibit specific properties that enhance wound healing capability. For example, higher absorbability can remove excess fluid from the wound site, thereby reducing the risk of infection and preventing tetanus and other diseases. They are also designed to permeate oxygen and gas despite nanocellulose having an excellent oxygen barrier property, allowing proper wound ventilation and promoting healing. Therapeutic agents with special functions such as antibiotics or growth factors can be added to 3D-printed cellulosic-based dressings to enhance their wound-healing efficiency. These reagents can be incorporated directly into the dressing material or coated on the surfaces. The excellent mechanical properties of cellulose-based biomaterials, such as tensile strength and flexibility, make them durable and easy to handle during the dressing process. They can also be disinfected to ensure safety in the clinical setting. Cellulose-based biomaterials in biomedical fields, especially in trauma dressings that combine biocompatibility, absorptivity, permeability, and mechanical properties will revolutionize wound care and improve patient outcomes. More 3D-printed cellulose-based biomaterials are expected for biomedical applications in this field[52].
5.2 Food packaging field
Cellulose and its derivatives like cellulose acetate, cellulose sulphate, nanocellulose, carboxymethyl cellulose, and methylcellulose, are explored as promising alternatives for conventional plastic in the food packaging field. The environmental issues have been widely discussed in the food packaging field[54]. The excellent sustainable and degradable performance of cellulose ensures safety by reducing plastic pollution and environmental impact. 3D printing technology can be integrated into the production, and modification processes, thereby improving corresponding properties and highlighting potentials for their application in food packaging. Cellulose packaging can be developed to have various packaging properties, including barrier, mechanical, thermal, preservation aspects, antimicrobial, and antioxidant properties. For example, adding antibacterial agents and antioxidants can provide cellulose with the capability to inhibit the growth and oxidation reaction of microorganisms and extend food shelf life[55]. On the other hand, designing a packaging structure with air permeability and moisture retention can maintain food freshness. Technologies like special fluorescent dyes, magnetic particles, or QR codes can add anti-counterfeiting labels on cellulosic packaging materials for the authenticity and safety of food since consumers can verify it through specific devices (such as ultraviolet lights, mobile Apps, etc.)[56].
Numerous chemical or physical methods can modify cellulose to improve its 3D printing performance, mechanical properties, and degradability for better packaging[57]. The high freedom of 3D printing technology can also satisfy different brand requirements. Zhou et al. 3D printed a composite comprising carboxymethyl nanocellulose, glycerin, and acrylamide derivatives as the shell and chitosan/AgNPs (CNGA/C-AgNPs) as the core through coaxial 3D-printing technology. The 3D printed cushioning-antibacterial dual-function packaging aerogel CNGA/C-AgNPs exhibited superior cushioning and resilience performance with an average compression resilience rate of more than 90%. 3D printing technology opens a new avenue for developing cellulose applications in food intelligent packaging[58].
5.3 Applications in other fields
Cellulosic materials are also emerging in the burgeoning 3D printing technology in extended fields, including oil sorption[59], stretchable batteries[60], electronics[61], building construction[62], sensors[63], paper manufacturing[64], automotive[65], aerospace[66], separators[67], and other promising fields. Discussions in detail for these applications can be found in other literature[68]. This review aims at biomedicine and food packaging applications. Therefore, 3D printing cellulose hydrogen and its applications in sensors are introduced here.
3D-printed hydrogels normally have superior mechanical properties, water absorbability in humid environments, and biofunctionalization potential. Therefore, the functions of sensors can be 3D printed using cellulose-based materials. For example, Zhu et al developed a moisture sensor using 3D-printed nanocellulose and carbon nanotube materials[69]. Such NFC/CNT humidity sensors exhibited a high response value of 69.9% at 95% relative humidity. They also display good bending resistance and long-term stability when monitoring human breath. Figure 4 shows the photographs and schematic illustration of 3D printing nanocellulose and carbon nanotube-based moisture sensor structure.
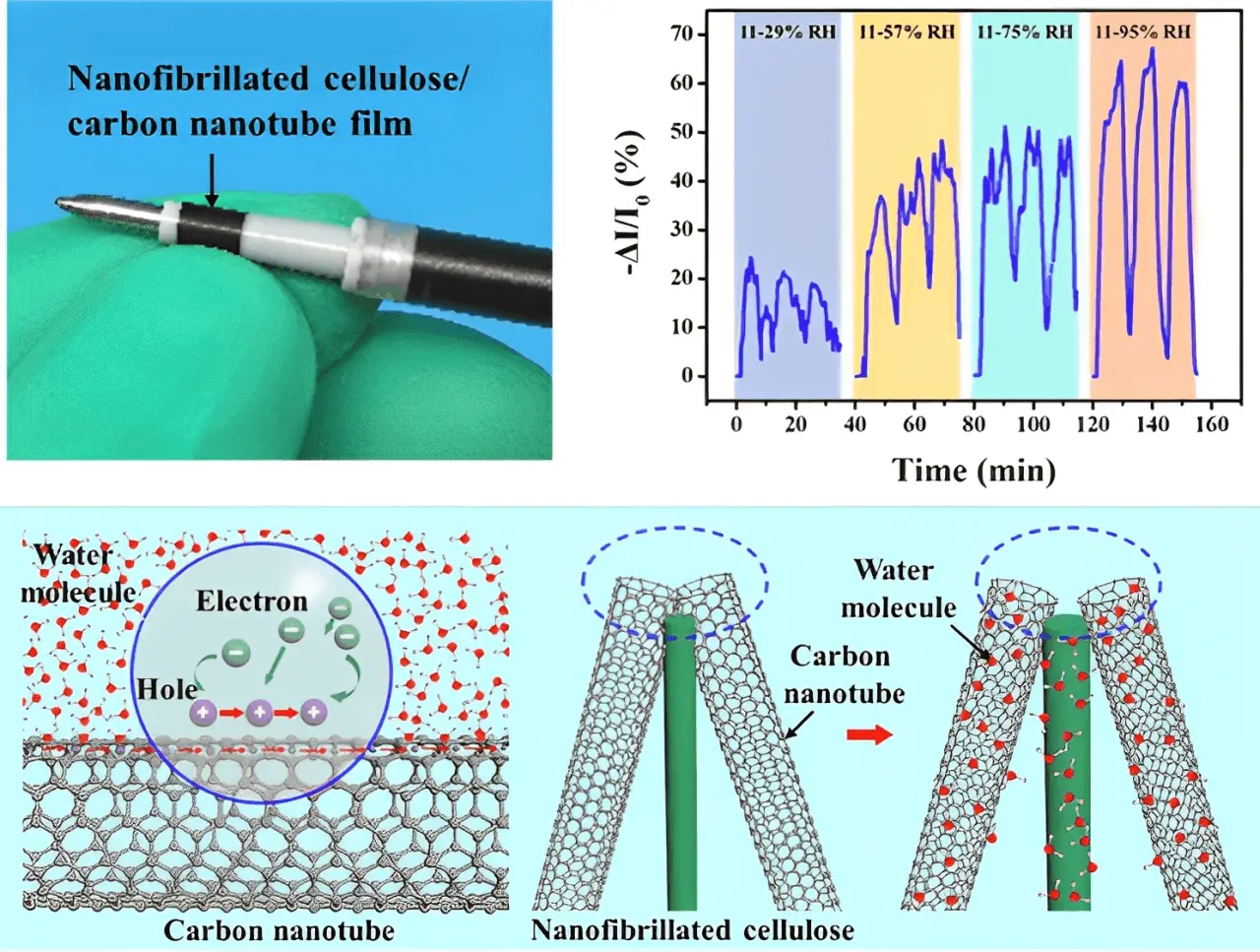
Figure 4. 3D printing nanocellulose and carbon nanotube-based moisture sensor. Republished with permission from[69].
Cellulose separators were 3D printed by Koh et al. as highly efficient filtration meshes for oil/water separation applications. Such 3D-printed separators comprise cellulose acetate/ethyl acetate in a complex structure and realize a high separation efficiency (> 99%) even at a high water flux of 160,000 L m-2 h-1 (Figure 5). These separators can separate various oil substances with different viscosities while maintaining anti-oil-fouling properties. This demonstrates the high capability of a 3D-printed cellulose separator[73].
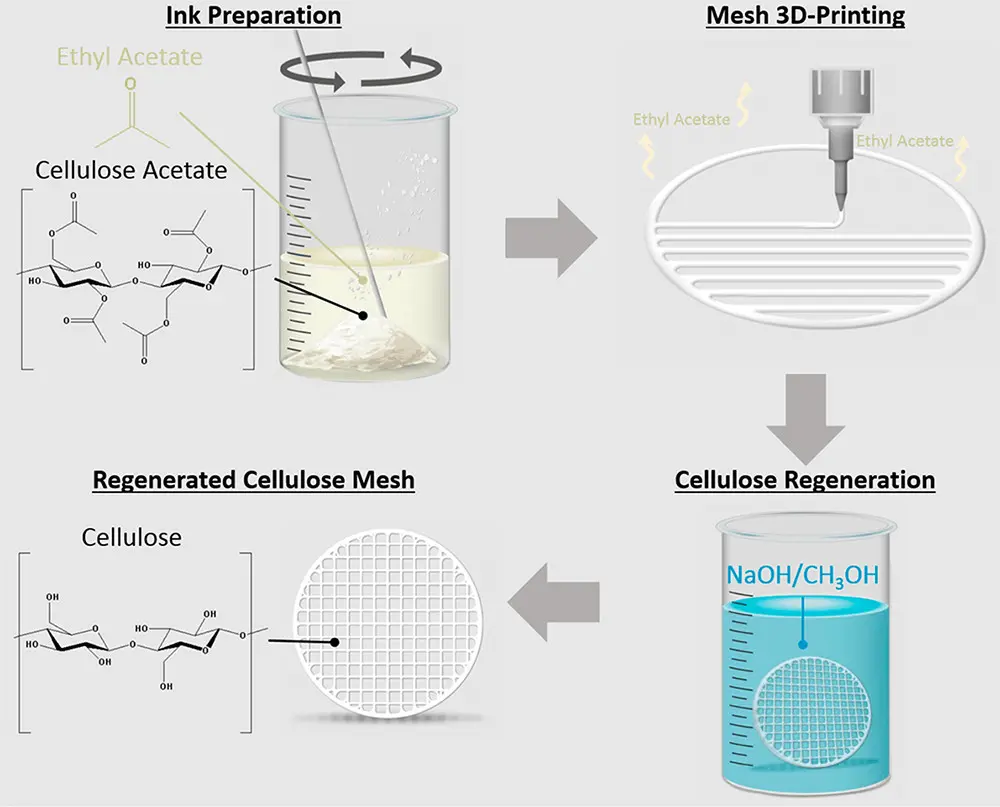
Figure 5. Schematic of 3D printed cellulose mesh antifouling for separating water and oil. Republished with permission from[73].
6. Optimization and Improvement of 3D Printing Cellulose
3D printing cellulose technology is still in its infant stage nowadays. Too many factors can affect the quality of printed products, such as rheology of printing "ink" and the addition of fillers to obtain functional composites and topological structures. These factors must be considered and investigated to improve this technology.
6.1 Rheological property improvement
The rheological properties of printing "ink" affect 3D printing accuracy and molding quality, which can be optimized to improve by adjusting parameters of concentration, viscosity, temperature, etc.
Concentration as an important parameter directly affects the rheological properties of the cellulose printing "ink", including viscosity and yield stress[74]. High concentration may lead to poor mobility and difficulty in squeezing through the nozzle. Low concentration can result in a loose printing structure with insufficient strength. Experiments are required to determine the optimal cellulose suspension concentration range for different 3D printing equipment and material characteristics. The concentration range needs to guarantee the strength and stability of the 3D printed structure and "ink" mobility[75].
Other parameters also can affect the viscosity of cellulose printing "ink", including the extrusion speed, linewidth, and interlayer binding force during the printing process[76]. The appropriate viscosity of printing "ink" can stabilize the printing process and realize precision 3D printing.
The viscosity of the cellulose "ink" can also be adjusted using a thickener or a diluent. A thickener like a hydroxyethyl cellulose (HEC) can increase the viscosity of the cellulose "ink", making it easier to stir, mix, and coat cellulose during 3D printing process. The amount of thickener should be accurately controlled according to specific requirements to avoid excessive thickening. Geng et al. reported that TEMPO-CNFs could form an entangled network in the suspension and that a higher TEMPO-CNF concentration can enhance the viscosity and modulus of cellulose printing "ink"[77]. At a low concentration between 0.2 and 2.0 wt%, the shear rate dependence of viscosity of TEMPO-CNF suspension can be fitted well using the Cross model. Newtonian flow characteristic is found in the dilute region and typical shear-thinning behavior is observed in the viscoelastic and gel regimes for a TEMPO-CNF suspensions with steady flow. Although the TEMPO-CNF suspension is a heterogeneous system, the repelling forces between anion groups on the surface of TEMPO-CNFs can stabilize the nanofibers in the suspensions[78]. When the concentration raises to 2.4 wt%, the curve of shear rate vs viscosity fits a power law that viscosity changes significantly with shear rate increase[79]. Furthermore, the viscosity of the TEMPO-CNFs decreases because of a decline in surface charge density and smaller, more uniform fibrils[80].
6.2 Composite material development
Biological or functional composites can be obtained by combining cellulose with other materials to improve the comprehensive performance of 3D printed materials. For example, TEMPO-oxidized cellulose nanofibril (TOCNF) films have exceptional mechanical properties, including high Young's modulus of up to 14 GPa, high tensile strength of up to 300 MPa, and high strain to failure of up to 10%[81]. As such, TOCNF-reinforced polymer composites were 2.3 times stiffer and 1.9 times stronger than the unadulterated polymeric material. Long-range and good matrix–fiber interactions were identified as reasons for the exceptional performance. Accordingly, utilizing TOCNFs as the reinforcing fiber for a 3D printing composite can result in great performance enhancement of the composite[82].
6.3 3D printing parameter optimization
Optimizing 3D printing parameters is desirable to obtain a better printing effect, including printing speed, layer rotation angle, layer thickness, etc. For example, an eco-friendly wood-plastic biocomposite can be 3D printed using modified poplar fibers and polylactic acid (PLA)[82]. The rheological properties to affect 3D printing are greatly affected by the concentration of poplar fibers and the shear rate of the printing ink. The printing parameters, including printing temperature, speed, and layer thickness also affect the product properties, and the rule of optimization must be obtained. By adjusting the printing orientations with the optimized printing parameters, favorable printability and mechanical properties of the poplar/PLA composite were obtained at the optimal printing temperature of 220 °C, speed of 40 mm/s, and layer thickness of 0.2 mm with the optimized orientation in a longitudinal stripe. It is worth noting that different printing parameters should be chosen according to the practical applications. Different physical and mechanical requirements need specially optimized parameters to realize the desirable efficient and economical utilization of the composites.
6.4 Post-processing optimization
Post-processing steps are also important for the optimization of 3D-printed products. Thermopress treatments of the printed parts can improve their density and eliminate the internal gap, enhancing the interlayer adhesion force and improving the overall strength. Optimization of the thermopress parameters such as temperature, pressure, and duration can avoid damaging the print or affecting its performance.
Surface modification of the 3D printed products by polish, sandblasting, or chemical treatment can improve their surface quality and adhesion. Coating the 3D printed products with a functional material also can enhance their corrosion resistance and aesthetics.
Curing treatment of 3D printed products can improve their strength and stability, and reduce the risk of deformation and cracking. Other post-processing options like ultrasonic and steam processing can also improve the performance and quality of the printed products. 3D printing technology of fiber-reinforced composite and traditional manufacturing can be combined to improve production efficiency and product quality. Recently, intelligent and automated technologies have been introduced to optimize the 3D printing and post-processing processes to improve production efficiency and product quality. Artificial intelligence and machine learning can intelligently optimize and predict 3D printing parameters and post-processing performance to achieve more efficient production with higher quality.
6.5 Structure design optimization
3D-printed cellulose products can be designed and manufactured with topological optimization, which enhances their mechanical behavior. A series of tests (e.g., mechanical tests) corresponding to physical models and numerical simulations will provide data for topological optimization, thereby serving 3D printing better products in design and rapid manufacturing. For example, CAD models of cellulose bone TE scaffolds can be constructed according to computed tomography images. Different layer-to-layer angles (e.g., 0, 45, 60, and 90 degrees) in the 3D-printed cellulose TE scaffolds can be employed for these models, which can be improved through topological optimization methods. Meanwhile, finite element analysis can validate the data obtained from the physical model tests. As a result, the mechanical properties of 3D printed cellulose products, including the ultimate load, yield load, failure deflection, yield deflection, stress, strain distribution, and porosity of scaffold structures, can be compared to determine the best mechanical properties after topological optimization. Topological optimization also helps design lightweight structures, which is essential for applications necessitating weight reduction, such as aircraft and automobile[83].
7. Challenges and Prospects
Despite extended research that has been conducted in 3D printing technology, 3D printing cellulose-based materials is just beginning. 3D printed cellulose has shown potential in many industry fields to substitute synthetic polymers in 3D printing technology. The cellulose-based sustainable printing "ink" is promising to lead to new innovative materials. Although promising in the future, the challenge is still huge due to the high cost, insufficient quality, dissolution problems, and performance stability of 3D printing cellulose currently. The cost of pre-and post-processing, technology limitations, quality of cellulose parts after printing, and difficulty to scale currently are the main challenges in 3D printing cellulose. Lignocellulose is made from wood. The content of other components may affect its applications in biomedicine or tissue engineering. Bacterial cellulose has high purity, which is another choice for 3D printing. However, the cost of bacterial cellulose is relatively higher. Bulk cellulose is difficult to dissolve to 3D print through the printer nozzle. Nanocellulose has a much higher cost in production. As such, the use of nanocellulose to 3D print significantly increased the cost. Meanwhile, the quality of 3D-printed nanocellulose products is better than that of bulk cellulose due to the unique properties of nanocellulose.
With the progress of technology and science, cellulose as a biomaterial in the field of 3D printing is expected to achieve innovative applications in the future. The application of cellulose as a biomaterial in the field of 3D printing has made remarkable progress, and it has shown great potential for application in biomedicine, food packaging, tissue engineering, and other fields. Further exploration of cellulose preparation methods, performance optimization, and printing process innovation are needed to promote its wide promotion and commercialization in practical applications.
Furthermore, the essential characteristics of cellulose like hydrophilicity limit the applications of 3D printing cellulose. As such, it is suitable for wound dressings or tissue engineering scaffolds. However, cellulose is not a good choice to produce food packaging without any modification. Water can evaporate through permeation. On the other hand, the difficult degradation of cellulose/nanocellulose is the problem when it is 3D printed to bone TE scaffold. The rigorous degradation rate required in the human body for bone regeneration is difficult to realize for cellulose.
In summary, the applications of 3D printing cellulose are still under exploration. Further studies are required to open new avenues for cellulose to satisfy more fields/industries. Cellulose-based 3D printing is expected to be an innovative, efficient, and sustainable technology when the cost is greatly reduced.
Authors contribution
Huang J: Writing-original draft, investigation.
Li L: Conceptualization, funding acquisition, writing-review & editing, supervision.
Conflicts of interest
The authors declare no conflicts of interest.
Ethical approval
Not applicable.
Consent to participate
Not applicable.
Consent for publication
Not applicable.
Availability of data and materials
Not appliable.
Funding
This study was supported and funded by the Innovation and Entrepreneurship Training Program for College Students in Shanghai (XJ2024384) and the USST-Essen Fiber New Materials Laboratory (Shanghai, China) (H-2023-369-013).
Copyright
© The Author(s) 2025.
References
-
1. Gibson I, Rosen D, Stucker B. Additive Manufacturing Technologies: 3D Printing, Rapid Prototyping, and Direct Digital Manufacturing. 2nd ed. New York: Springer; 2015.
-
2. Pang M, Huang Y, Meng F, Zhuang Y, Liu H, Du M, et al. Application of bacterial cellulose in skin and bone tissue engineering. Eur Polym J. 2020;122:109365.
[DOI] -
3. French A. D. The quintessential sustainable resource: cellulose, and the journal named for it. Cellulose. 2019;26(1):1-3.
[DOI] -
4. Dai L, Qiu Y, Xu YY, Song Y. Biomass Transformation of Cellulose via N-Heterocyclic Carbene-Catalyzed Umpolung of 5-(Chloromethyl)furfural. Cell Rep Phys Sci. 2020;1(6):100071.
[DOI] -
5. Yustira A, Harahap H, Nasution H, Pranata A. Isolation of cellulose from agricultural waste using different treatments: A review. IOP Conf Ser Earth Environ Sci. 2021;912:012020.
[DOI] -
6. Salthouse D, Novakovic K, Hilkens CMU, Ferreira AM. Interplay between biomaterials and the immune system: Challenges and opportunities in regenerative medicine. Acta Biomater. 2023;155:1-18.
[DOI] -
7. Gu Y, Huang J. Colorimetric detection of gaseous ammonia by polyaniline nanocoating of natural cellulose substances. Colloids Surf A Physicochem Eng Asp. 2013;433:166-172.
[DOI] -
8. Weng Z, Su Y, Wang DW, Li F, Du J, Cheng HM. Graphene-Cellulose Paper Flexible Supercapacitors. Adv Energy Mater. 2011;1(5):917-922.
[DOI] -
9. Makowski K, Leszczewicz M, Broncel N, Lipinska-Zubrycka L, Glebski A, Komorowski P, et al. Isolation, Biochemical Characterisation and Identification of Thermotolerant and Cellulolytic Paenibacillus lactis and Bacillus licheniformis. Food Technol Biotechnol. 2021;59(3):325-336.
[DOI] -
10. Hao J, Ye W, Gao C, Zhu M, Yang L, Liao R. Experimental and molecular level analysis of natural ester delaying degradation of cellulose insulation polymer. High Voltage. 2021;7(5):1001-1015.
[DOI] -
11. Liu Y, Huang H, Huo P, Gu J. Exploration of zwitterionic cellulose acetate antifouling ultrafiltration membrane for bovine serum albumin (BSA) separation. Carbohydr Polym. 2017;165:266-275.
[DOI] -
12. Jin Z, Fan H, Li BG, Zhu S. Evaluation of Octyltetramethyldisiloxane-Containing Ethylene Copolymers as Composite Lubricant for High-Density Polyethylene. Macromol Mater Eng. 2016;301(12):1494-1502.
[DOI] -
13. Li L, Zhu Y, Yang J. 3D bioprinting of cellulose with controlled porous structures from NMMO. Mater Lett. 2018;210:136-138.
[DOI] -
14. Xu W, Wang X, Sandler N, Willfor S, Xu C. Three-Dimensional Printing of Wood-Derived Biopolymers: A Review Focused on Biomedical Applications. ACS Sustain Chem Eng. 2018;6(5):5663-5680.
[DOI] [PubMed] [PMC] -
15. Garces I, Ngo TD, Ayranci C, Boluk Y. Regenerated cellulose in additive manufacturing. Cellulose. 2024;31(3):1773-1785.
[DOI] -
16. Henke K, Treml S. Wood based bulk material in 3D printing processes for applications in construction. Eur J Wood Prod. 2012;71(1):139-141.
[DOI] -
17. Truby RL, Lewis JA. Printing soft matter in three dimensions. Nature. 2016;540(7633):371-378.
[DOI] [PubMed] -
18. Hull CW inventor; 3D Systems Inc., assignee. Apparatus for Production of Three-Dimensional Objects by Stereolithography. United States patent US4575330A. 1986 Mar 11.
-
19. Hakansson KMO, Henriksson IC, de la Pena Vazquez C, Kuzmenko V, Markstedt K, Enoksson P, et al. Solidification of 3D Printed Nanofibril Hydrogels into Functional 3D Cellulose Structures. Adv Mater Technol. 2016;1(7):1600096.
[DOI] -
20. Gross BC, Erkal JL, Lockwood SY, Chen C, Spence DM. Evaluation of 3D printing and its potential impact on biotechnology and the chemical sciences. Anal Chem. 2014;86(7):3240-3253.
[DOI] [PubMed] -
21. Gunasekera DH, Kuek S, Hasanaj D, He Y, Tuck C, Croft AK, et al. Three dimensional ink-jet printing of biomaterials using ionic liquids and co-solvents. Faraday Discuss. 2016;190:509-523.
[DOI] [PubMed] -
22. Fink HP, Weigel P, Purz HJ, Ganster J. Structure formation of regenerated cellulose materials from NMMO-solutions. Prog Polym Sci. 2001;26(9):1473-1524.
[DOI] -
23. Swatloski RP, Spear SK, Holbrey JD, Rogers RD. Dissolution of cellulose with ionic liquids. J Am Chem Soc. 2002;124(18):4974-4975.
[DOI] [PubMed] -
24. Zhang C, Liu R, Xiang J, Kang H, Liu Z, Huang Y. Dissolution mechanism of cellulose in N,N-dimethylacetamide/lithium chloride: revisiting through molecular interactions. J Phys Chem B. 2014;118(31):9507-9514.
[DOI] [PubMed] -
25. Liu S, Zhang Q, Gou S, Zhang L, Wang Z. Esterification of cellulose using carboxylic acid-based deep eutectic solvents to produce high-yield cellulose nanofibers. Carbohydr Polym. 2021;251:117018.
[DOI] [PubMed] -
26. Tan X, Zhao W, Mu T. Controllable exfoliation of natural silk fibers into nanofibrils by protein denaturant deep eutectic solvent: nanofibrous strategy for multifunctional membranes. Green Chem. 2018;20(15):3625-3633.
[DOI] -
27. Cai J, Zhang L. Rapdi dissolution of cellulose in LiOH/urea and NaOH/urea aqueous solutions. Macromol Biosci. 2005;5(6):539-548.
[DOI] [PubMed] -
28. Jiang J, Oguzlu H, Jiang F. 3D printing of lightweight, super-strong yet flexible all-cellulose structure. Chem Eng J. 2021;405:126668.
[DOI] -
29. Baniasadi H, Ajdary R, Trifol J, Rojas OJ, Seppala J. Direct ink writing of aloe vera/cellulose nanofibrils bio-hydrogels. Carbohydr Polym. 2021;266:118114.
[DOI] [PubMed] -
30. Lan X, Ma Z, Szojka ARA, Kunze M, Mulet-Sierra A, Vyhlidal MJ, et al. TEMPO-Oxidized Cellulose Nanofiber-Alginate Hydrogel as a Bioink for Human Meniscus Tissue Engineering. Front Bioeng Biotechnol. 2021;9:766399.
[DOI] [PubMed] [PMC] -
31. Miao H, Liu Y, Man Y, Huang G, Huang H, Fu X, et al. High-Efficiency and Recyclable Green Molten Salt Hydrate Solvent for Cellulose Hydrogels with High Conductivity and Freeze Tolerance. ACS Sustainable Chem Eng. 2023;11(24):9225-9234.
[DOI] -
32. Zhong C, Cheng F, Zhu Y, Gao Z, Jia H, Wei P. Dissolution mechanism of cellulose in quaternary ammonium hydroxide: Revisiting through molecular interactions. Carbohydr Polym. 2017;174:400-408.
[DOI] [PubMed] -
33. Li H, Xin Q, Li X, Lu X, Zhao J. Microwave-associated ZnCl2 pretreatment followed by enzymatic hydrolysis for high-efficiency production of nanocellulose from Eucalyptus dissolving pulp. Chem Eng J. 2024;500:157280.
[DOI] -
34. Niu F, Li M, Huang Q, Zhang X, Pan W, Yang J, et al. The characteristic and dispersion stability of nanocellulose produced by mixed acid hydrolysis and ultrasonic assistance. Carbohydr Polym. 2017;165:197-204.
[DOI] [PubMed] -
35. Yang Y, Yang J, Wang R, Liu J, Zhang Y, Liu L, et al. Cooperation of hydrolysis modes among xylanases reveals the mechanism of hemicellulose hydrolysis by Penicillium chrysogenum P33. Microb Cell Fact. 2019;18(1):159.
[DOI] [PubMed] [PMC] -
36. Satyamurthy P, Vigneshwaran N. A novel process for synthesis of spherical nanocellulose by controlled hydrolysis of microcrystalline cellulose using anaerobic microbial consortium. Enzyme Microb Technol. 2013;52(1):20-25.
[DOI] [PubMed] -
37. Abdulhafiz F, Mohammed A, Reduan MH, Kari Zulhisyam A, Wei LS, Goh KW. Plant cell culture technologies: A promising alternatives to produce high-value secondary metabolites. Arabian J Chem. 2022;15(11):104161.
[DOI] -
38. Khaled SA, Burley JC, Alexander MR, Yang J, Roberts CJ. 3D printing of five-in-one dose combination polypill with defined immediate and sustained release profiles. J Control Release. 2015;217:308-314.
[DOI] [PubMed] -
39. Yang Y, Wang X, Lin X, Xie L, Ivone R, Shen J, et al. A tunable extruded 3D printing platform using thermo-sensitive pastes. Int J Pharm. 2020;583:119360.
[DOI] [PubMed] -
40. Imlimthan S, Correia A, Figueiredo P, Lintinen K, Balasubramanian V, Airaksinen AJ, et al. Systematic in vitro biocompatibility studies of multimodal cellulose nanocrystal and lignin nanoparticles. J Biomed Mater Res A. 2020;108(3):770-783.
[DOI] [PubMed] -
41. Valente AJM, Polishchuk AY, Burrows HD, Lobo VMM. Permeation of water as a tool for characterizing the effect of solvent, film thickness and water solubility in cellulose acetate membranes. Eur Polym J. 2005;41(2):275-281.
[DOI] -
42. Aziz T, Farid A, Haq F, Kiran M, Ullah A, Zhang K, et al. A Review on the Modification of Cellulose and Its Applications. Polymers. 2022;14(15):3206.
[DOI] [PubMed] [PMC] -
43. Nouri M, Abbasi M, Seraj M, Mehraz L. Fabrication and characterization of drug-loaded wet spun polycaprolactone fibers. J Text Inst. 2020;112(3):462-469.
[DOI] -
44. Brindha J, Privita Edwina RG, Rajeshb PK, Rani P. Influence of rheological properties of protein bio-inks on printability: a simulation and validation study. Mater Today Proc. 2016;3(10):3285-3295.
[DOI] -
45. Smay JE, Gratson GM, Shepherd RF, Cesarano J, Lewis JA. Directed Colloidal Assembly of 3D Periodic Structures. Adv Mater. 2002;14(18):1279-1283.
[DOI] -
46. Sun K, Wei TS, Ahn BY, Seo JY, Dillon SJ, Lewis JA. 3D printing of interdigitated Li-ion microbattery architectures. Adv Mater. 2013;25(33):4539-4543.
[DOI] [PubMed] -
47. He Y, Gao Q, Wu WB, Nie J, Fu JZ. 3D Printed Paper-Based Microfluidic Analytical Devices. Micromachines. 2016;7(7):108.
[DOI] [PubMed] [PMC] -
48. Gong J, Hou L, Ching YC, Ching KY, Hai ND, Chuah CH. A review of recent advances of cellulose-based intelligent-responsive hydrogels as vehicles for controllable drug delivery system. Int J Biol Macromol. 2024;264(Pt 2):130525.
[DOI] [PubMed] -
49. Zhang X, Li Z, Yang P, Duan G, Liu X, Gu Z, et al. Polyphenol scaffolds in tissue engineering. Mater Horiz. 2021;8(1):145-167.
[DOI] [PubMed] -
50. Ananth KP, Jayram ND. A comprehensive review of 3D printing techniques for biomaterial-based scaffold fabrication in bone tissue engineering. Ann 3D Print Med. 2024;13(10):100141.
[DOI] -
51. Kusuma HS, Yugiani P, Himana AI, Aziz A, Putra DAW. Reflections on food security and smart packaging. Polym Bull. 2023;81(1):1-47.
[DOI] [PubMed] [PMC] -
52. Bilirgen AC, Toker M, Odabas S, Yetisen AK, Garipcan B, Tasoglu S. Plant-Based Scaffolds in Tissue Engineering. ACS Biomater Sci Eng. 2021;7(3):926-938.
[DOI] [PubMed] -
53. Diedkova K, Pogrebnjak AD, Kyrylenko S, Smyrnova K, Buranich VV, Horodek P, et al. Polycaprolactone-MXene Nanofibrous Scaffolds for Tissue Engineering. ACS Appl Mater Interfaces. 2023;15(11):14033-14047.
[DOI] [PubMed] -
54. Huang B, He H, Meng S, Jia Y. Optimizing 3D printing performance of acrylonitrile-butadiene-styrene composites with cellulose nanocrystals/silica nanohybrids. Polym Int. 2019;68(7):1351-1360.
[DOI] -
55. Mussig S, Reichstein J, Miller F, Mandel K. Colorful Luminescent Magnetic Supraparticles: Expanding the Applicability, Information Capacity, and Security of Micrometer-Scaled Identification Taggants by Dual-Spectral Encoding. Small. 2022;18(13):e2107511.
[DOI] [PubMed] -
56. Jiang Y, De La Cruz JA, Ding L, Wang B, Feng X, Mao Z, et al. Rheology of regenerated cellulose suspension and influence of sodium alginate. Int J Biol Macromol. 2020;148:811-816.
[DOI] [PubMed] -
57. Cai M, Zhong H, Li C, Aliakbarlu J, Zhang H, Cui H, et al. Application of composite coating of Nostoc commune Vauch polysaccharides and sodium carboxymethyl cellulose for preservation of salmon fillets. Int J Biol Macromol. 2022;210:394-402.
[DOI] [PubMed] -
58. Zhou W, Fang J, Tang S, Wu Z, Wang X. 3D-Printed Nanocellulose-Based Cushioning-Antibacterial Dual-Function Food Packaging Aerogel. Molecules. 2021;26(12):3543.
[DOI] -
59. Li A, Huber T, Barker D, Nazmi AR, Najaf Zadeh H. An overview of cellulose aerogels and foams for oil sorption: Preparation, modification, and potential of 3D printing. Carbohydr Polym. 2024;343:122432.
[DOI] [PubMed] -
60. Qian J, Chen Q, Hong M, Xie W, Jing S, Bao Y, et al. Toward stretchable batteries: 3D-printed deformable electrodes and separator enabled by nanocellulose. Mater Today. 2022;54:18-26.
[DOI] -
61. Barras R, Cunha I, Gaspar D, Fortunato E, Martins R, Pereira L. Printable cellulose-based electroconductive composites for sensing elements in paper electronics. Flex Print Electron. 2017;2(1):014006.
[DOI] -
62. Long WJ, Tao JL, Lin C, Gu Y, Mei L, Duan H, et al. Rheology and buildability of sustainable cement-based composites containing micro-crystalline cellulose for 3D-printing. J Cleaner Prod. 2019;239:118054.
[DOI] -
63. Kim T, Bao C, Hausmann M, Siqueira G, Zimmermann T, Kim WS. Electrochemical Sensors: 3D printed disposable wireless ion sensors with biocompatible cellulose composites. Adv Electron Mater. 2019;5(2):1970007.
[DOI] -
64. Stolz B, Mülhaupt R. Cellular, Mineralized, and Programmable Cellulose Composites Fabricated by 3D Printing of Aqueous Pastes Derived from Paper Wastes and Microfibrillated Cellulose. Macromol Mater Eng. 2020;305(4):1900740.
[DOI] -
65. Kiziltas A, Kiziltas EE, Torun SB, Gardner DJ. Micro-and nanocellulose composites for automotive applications. In: Proceedings of SPE automotive composites conference and exhibition (ACCE); 2013 Sep 13; Novi, USA. 2013. p. 11-13. Available from: https://www.researchgate.net/profile/Sevda-Boran-Torun/publication/56c9f4b908ae11063709ac4d/Micro-and-nanocellulose-composites-for-automotive-applications.pdf
-
66. Guan QF, Yang HB, Han ZM, Zhou LC, Zhu YB, Ling ZC, et al. Lightweight, tough, and sustainable cellulose nanofiber-derived bulk structural materials with low thermal expansion coefficient. Sci Adv. 2020;6(18):eaaz1114.
[DOI] [PubMed] [PMC] -
67. Firmanda A, Fahma F, Syamsu K, Suprihatin S, Purnawati R, Mahardika M, et al. Cellulose and its composite for sustainable oils/water (O/W) separation: From cellulose sponge to 3D printed nanocellulose. J Environ Chem Eng. 2023;11(5):110359.
[DOI] -
68. Firmanda A, Syamsu K, Sari YW, Cabral J, Pletzer D, Mahadik B, et al. 3D printed cellulose based product applications. Mater Chem Front. 2022;6(3):254-279.
[DOI] -
69. Zhu P, Liu Y, Fang Z, Kuang Y, Zhang Y, Peng C, et al. Flexible and Highly Sensitive Humidity Sensor Based on Cellulose Nanofibers and Carbon Nanotube Composite Film. Langmuir. 2019;35(14):4834-4842.
[DOI] [PubMed] -
70. Sammut EJ, Yeap YC, Yeap JQH, Mendonca G. Automated custom-fitted 3D-printed masks using free software and face scans. Research Square [Preprint]. 2020.
[DOI] -
71. Provenzano D, Rao YJ, Mitic K, Obaid SN, Pierce D, Huckenpahler J, et al. Rapid prototyping of reusable 3D-printed N95 equivalent respirators at the George Washington University. Preprints.org [Preprint]. 2020.
[DOI] -
72. Cai M, Li H, Shen S, Wang Y, Yang Q. Customized design and 3D printing of face seal for an N95 filtering facepiece respirator. J Occup Environ Hyg. 2018;15(3):226-234.
[DOI] -
73. Koh JJ, Lim GJH, Zhou X, Zhang X, Ding J, He C. 3D-Printed Anti-Fouling Cellulose Mesh for Highly Efficient Oil/Water Separation Applications. ACS Appl Mater Interfaces. 2019;11(14):13787-13795.
[DOI] -
74. Taheri H, Samyn P. Effect of homogenization (microfluidization) process parameters in mechanical production of micro-and nanofibrillated cellulose on its rheological and morphological properties. Cellulose. 2016;23(2):1221-1238.
[DOI] -
75. Cheng E, Yu H, Ahmadi A, Cheung KC. Investigation of the hydrodynamic response of cells in drop on demand piezoelectric inkjet nozzles. Biofabrication. 2016;8(1):015008.
[DOI] -
76. Zhou Z, Yao Y, Zhang J, Shen L, Xu H, Liu J, et al. Effects of poly(vinyl alcohol) (PVA) concentration on rheological behavior of TEMPO-mediated oxidized cellulose nanofiber/PVA suspensions. Cellulose. 2022;29(15):8255-8263.
[DOI] -
77. Geng L, Mittal N, Zhan C, Ansari F, Sharma PR, Peng X, et al. Understanding the Mechanistic Behavior of Highly Charged Cellulose Nanofibers in Aqueous Systems. Macromolecules. 2018;51(4):1498-1506.
[DOI] -
78. Koponen AI. The effect of consistency on the shear rheology of aqueous suspensions of cellulose micro- and nanofibrils: a review. Cellulose. 2020;27(4):1879-1897.
[DOI] -
79. Liao J, Pham KA, Breedveld V. Rheological characterization and modeling of cellulose nanocrystal and TEMPO-oxidized cellulose nanofibril suspensions. Cellulose. 2020;27(7):3741-3757.
[DOI] -
80. Liao J, Pham KA, Breedveld V. TEMPO-CNF suspensions in the viscoelastic regime: capturing the effect of morphology and surface charge with a rheological parameter. Cellulose. 2020;28(2):813-827.
[DOI] -
81. Tang Z, Lin X, Yu M, Mondal AK, Wu H. Recent advances in TEMPO-oxidized cellulose nanofibers: Oxidation mechanism, characterization, properties and applications. Int J Biol Macromol. 2024;259(Pt 1):129081.
[DOI] [PubMed] -
82. Yang Z, Feng X, Rodrigue D. Printability and Properties of 3D-printed Poplar Fiber/Polylactic Acid Biocomposite. BioResources. 2021;16(2):2774-2788.
[DOI] -
83. Hu J, Wang JH, Wang R, Yu XB, Liu Y, Baur DA. Analysis of biomechanical behavior of 3D printed mandibular graft with porous scaffold structure designed by topological optimization. 3D Print Med. 2019;5(1):5.
[DOI] [PubMed]
Copyright
© The Author(s) 2025. This is an Open Access article licensed under a Creative Commons Attribution 4.0 International License (https://creativecommons.org/licenses/by/4.0/), which permits unrestricted use, sharing, adaptation, distribution and reproduction in any medium or format, for any purpose, even commercially, as long as you give appropriate credit to the original author(s) and the source, provide a link to the Creative Commons license, and indicate if changes were made.
Publisher’s Note
Share And Cite